钎焊是一种多功能的连接工艺,涉及熔化填充金属以连接两种或多种基材,而不熔化基材本身。这种方法因其能够创建坚固、耐用且变形最小的接头而广泛应用于各个行业。根据连接的材料、所需的接头性能和具体的应用要求,采用不同类型的钎焊技术。本文将探讨各种类型的钎焊,重点介绍它们的独特特性、优点和应用。
要点解释:
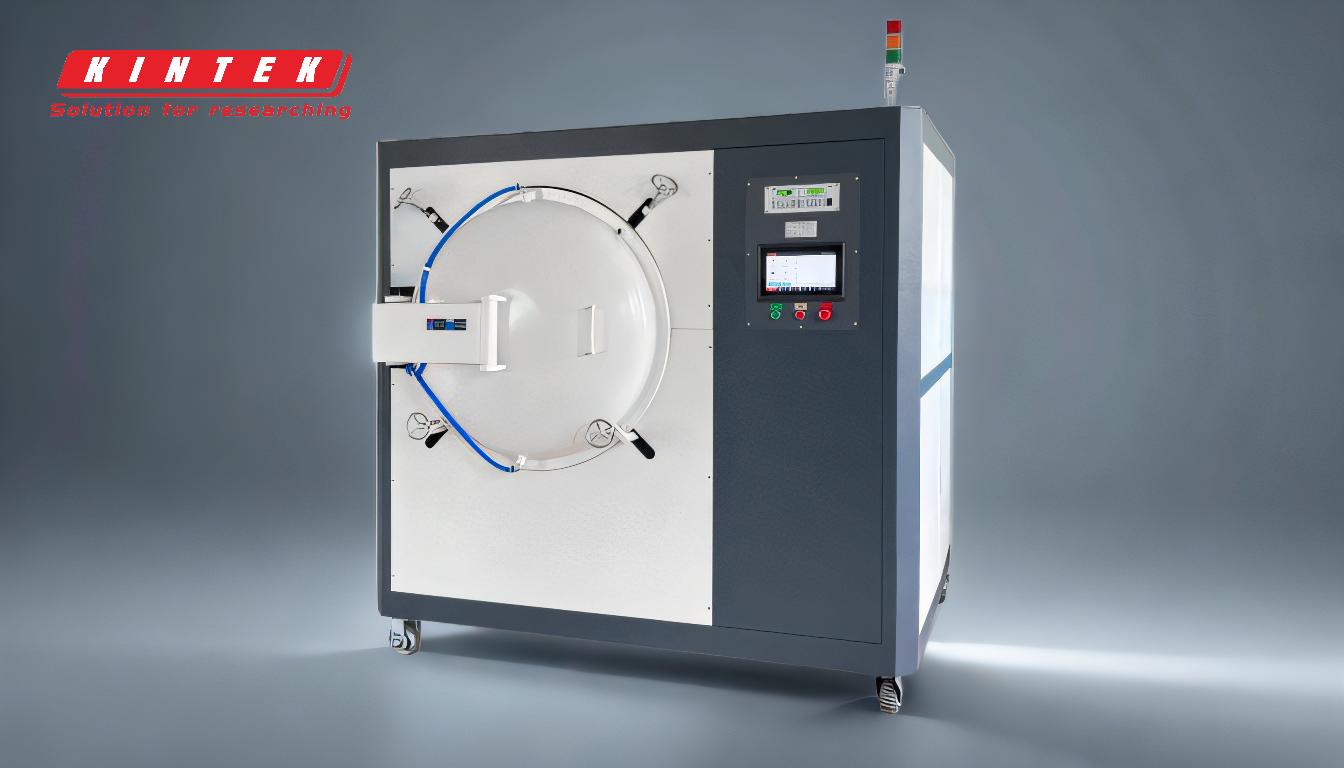
-
氩弧焊钎焊:
- 过程 :TIG(钨极惰性气体)钎焊使用钨电极产生电弧来加热工件。与传统焊接相比,该工艺的运行电流较低,这有助于防止基材熔化,特别是在使用铸铁等材料时。
- 保护气体 :氩气用于保护钎焊区域免受大气污染,从而无需使用焊剂。这使得工艺更加清洁并减少了钎焊后的清洁要求。
- 应用领域 :TIG 钎焊对于连接薄材料、修复铸铁部件以及需要精确热控制的应用特别有用。
-
氧-燃料钎焊:
- 过程 :该方法利用燃料气体(例如乙炔)与氧气燃烧产生的火焰来加热母材并熔化填充金属。火焰提供集中热源,实现局部加热。
- 通量要求 :与 TIG 钎焊不同,氧燃料钎焊通常需要使用焊剂来防止氧化并促进填充金属的流动。加热前必须将助焊剂涂抹到接缝区域。
- 应用领域 :氧燃料钎焊通常用于连接铜管、HVAC 系统以及其他需要坚固、防漏接头的应用。
-
炉内钎焊:
- 过程 :炉钎焊是将组装好的零件和填充金属放入炉中,将整个组件加热到钎焊温度。该炉提供均匀的加热,这对于实现一致的接头质量至关重要。
- 气氛控制 :可以控制炉内气氛以防止氧化,通常使用惰性气体或真空条件。这消除了对助焊剂的需求,并产生清洁、高质量的接头。
- 应用领域 :炉钎焊非常适合大规模生产需要高精度和可重复性的零部件,例如汽车零部件、航空航天零部件和电子组件。
-
感应钎焊:
- 过程 :感应钎焊利用电磁感应在工件内产生热量。在接合区域附近放置感应线圈,交流电通过线圈,在工件中感应出涡流,从而产生热量。
- 优点 :该方法加热速度快,加热控制精确,适合高速生产和局部加热。
- 应用领域 :感应钎焊通常用于电气工业中连接铜和铝部件,以及医疗设备和珠宝的生产。
-
浸焊:
- 过程 :在浸焊中,将组装好的零件浸入熔盐浴或熔融填充金属浴中。来自熔池的热量熔化填充金属,然后填充金属通过毛细管作用流入接头。
- 助焊剂用量 :如果使用熔盐浴,盐既充当热源又充当助熔剂,无需额外涂抹助熔剂。
- 应用领域 :浸焊通常用于连接铝和其他有色金属,特别是在航空航天和汽车行业。
-
电阻钎焊:
- 过程 :电阻钎焊涉及使电流通过接头区域,由于材料的电阻而产生热量。热量熔化填充金属,然后填充金属流入接头。
- 优点 :这种方法可以精确控制热量的施加,适合连接小型、精密的部件。
- 应用领域 :电阻钎焊通常用于电子行业,用于连接连接器、端子和其他小型部件。
-
激光钎焊:
- 过程 :激光钎焊使用聚焦激光束加热接头区域并熔化填充金属。激光提供高度集中的热源,可以精确控制钎焊过程。
- 优点 :激光钎焊精度高、热影响区最小,并且能够连接不同材料。
- 应用领域 :这种方法在汽车工业中用于连接车身面板,以及在医疗和电子行业中用于连接小型、复杂的部件。
每种类型的钎焊都有其自身的优点,并且适合特定的应用。钎焊方法的选择取决于所连接的材料、所需的接头性能、产量和具体应用要求等因素。了解不同类型的钎焊可以选择最合适的方法,以在各种工业应用中实现高质量、耐用的接头。
汇总表:
钎焊类型 | 主要特点 | 应用领域 |
---|---|---|
氩弧焊钎焊 | 使用氩气,无需助焊剂 | 薄材料、铸铁修复 |
氧-燃料钎焊 | 需要助焊剂、局部加热 | 铜管、暖通空调系统 |
炉内钎焊 | 均匀加热,可控气氛 | 汽车、航空航天、电子 |
感应钎焊 | 快速加热,精确控制 | 电气、医疗器械、珠宝 |
浸焊 | 使用熔盐或填充金属浴 | 铝、航空航天、汽车 |
电阻钎焊 | 电流加热接头 | 电子产品、连接器、端子 |
激光钎焊 | 高精度、热影响区最小 | 汽车车身板、医疗器械 |
需要帮助为您的项目选择正确的钎焊方法吗? 立即联系我们的专家 寻求个性化建议!