热蒸发虽然是一种具有成本效益的薄膜沉积方法,但也有一些明显的缺点。其中包括材料兼容性方面的挑战,例如舟裂和热冲击,以及薄膜质量方面的问题,包括均匀性差、杂质含量高和薄膜密度低。此外,由于成分的蒸汽压力不同,沉积合金也很困难,而且该方法的可扩展性有限。尽管与溅射法相比,热蒸发法的沉积率更高,但这些缺点使其不太适合某些应用,尤其是那些需要高纯度、均匀和致密薄膜的应用。
要点说明:
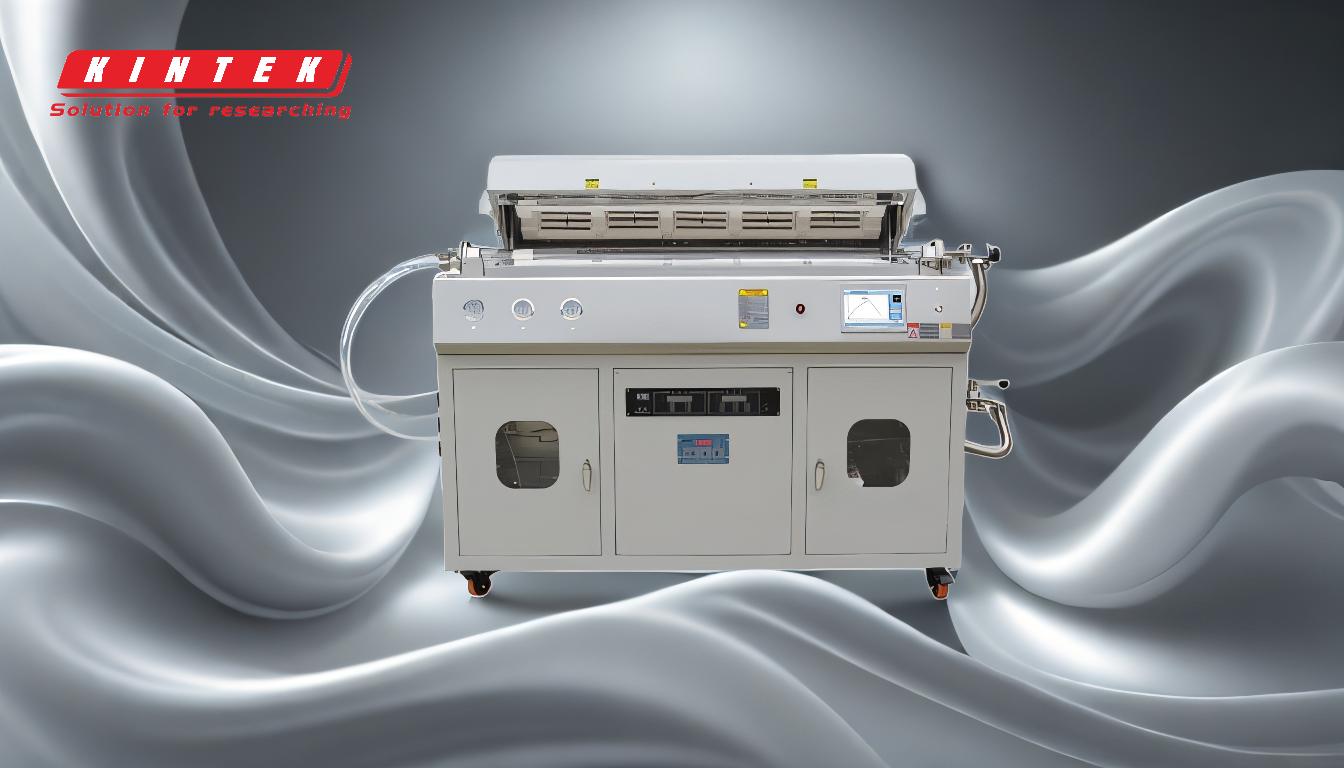
-
船体开裂和热冲击:
- 船体裂缝:出现这种情况的原因是蒸发舟材料和蒸发剂在高温下发生合金化。一旦出现裂纹,舟必须丢弃,从而导致成本增加和停机时间延长。
- 热冲击:快速加热和冷却会造成热冲击,导致艇体开裂。为缓解这一问题,必须平稳地升高和降低加热源的功率,以确保加热均匀。
-
薄膜质量问题:
- 均匀性差:如果不使用行星系统和掩膜,要实现均匀的薄膜厚度是一项挑战。
- 杂质含量高:在物理气相沉积 (PVD) 方法中,热蒸发法的杂质含量往往最高。
- 低密度薄膜:生产的薄膜通常密度较低,但可通过离子辅助技术加以改进。
- 中等薄膜应力:薄膜可能会产生适度应力,从而影响其机械性能。
-
合金沉积的挑战:
- 不同的蒸汽压力:合金中含有不同蒸汽压的材料,因此很难控制每种成分的蒸发率。
- 复杂工艺:其中一种方法是在不同的坩埚中同时熔化两种原料,并分别控制每种原料的蒸发率,这种方法既复杂又难以管理。
-
可扩展性有限:
- 可扩展性问题:热蒸发不易扩展,因此不太适合大规模工业应用。
-
与溅射法的比较:
- 更高的沉积率:与溅射法相比,热蒸发法的沉积率更高,但上述缺点抵消了这一优势。
总之,虽然热蒸发在某些应用中是一种经济有效的方法,但其缺点(如舟裂、薄膜质量差、合金沉积困难和可扩展性有限)使其不太适合高精度和大规模应用。有关热蒸发的更多详细信息,请参阅以下内容 热蒸发 资源。
汇总表:
缺点 | 说明 |
---|---|
船只开裂 | 艇体材料与蒸发剂之间的合金化会导致开裂,从而增加成本。 |
热冲击 | 快速加热/冷却导致开裂;需要平稳的功率斜坡。 |
薄膜均匀性差 | 如果没有行星系统或掩膜,很难实现均匀的厚度。 |
杂质含量高 | 在 PVD 方法中杂质含量最高。 |
低密度薄膜 | 薄膜通常密度较低,但可通过离子辅助技术加以改进。 |
合金沉积面临的挑战 | 不同的蒸汽压力使蒸发率难以控制。 |
可扩展性有限 | 不易扩展至大规模工业应用。 |
需要更好的薄膜沉积解决方案? 立即联系我们的专家 探讨替代方案!