化学气相沉积(CVD)是一种广泛用于沉积薄膜和涂层的技术,但它也有一些明显的缺点。其中包括由于蒸气压力、成核和生长速度的变化导致颗粒成分不均匀,从而给合成多组分材料带来挑战。该工艺通常需要较高的温度,这会导致基底热不稳定,并限制可使用的材料类型。此外,CVD 所需的化学前体可能具有剧毒性、挥发性和危险性,而且副产品通常具有毒性和腐蚀性,使得中和成本高昂且问题重重。此外,该工艺还受到真空室尺寸的限制,难以对较大的表面进行镀膜,而且无法在现场进行,需要将零件运送到镀膜中心。这些因素使得 CVD 成为一种复杂的方法,有时在某些应用中并不实用。
要点说明:
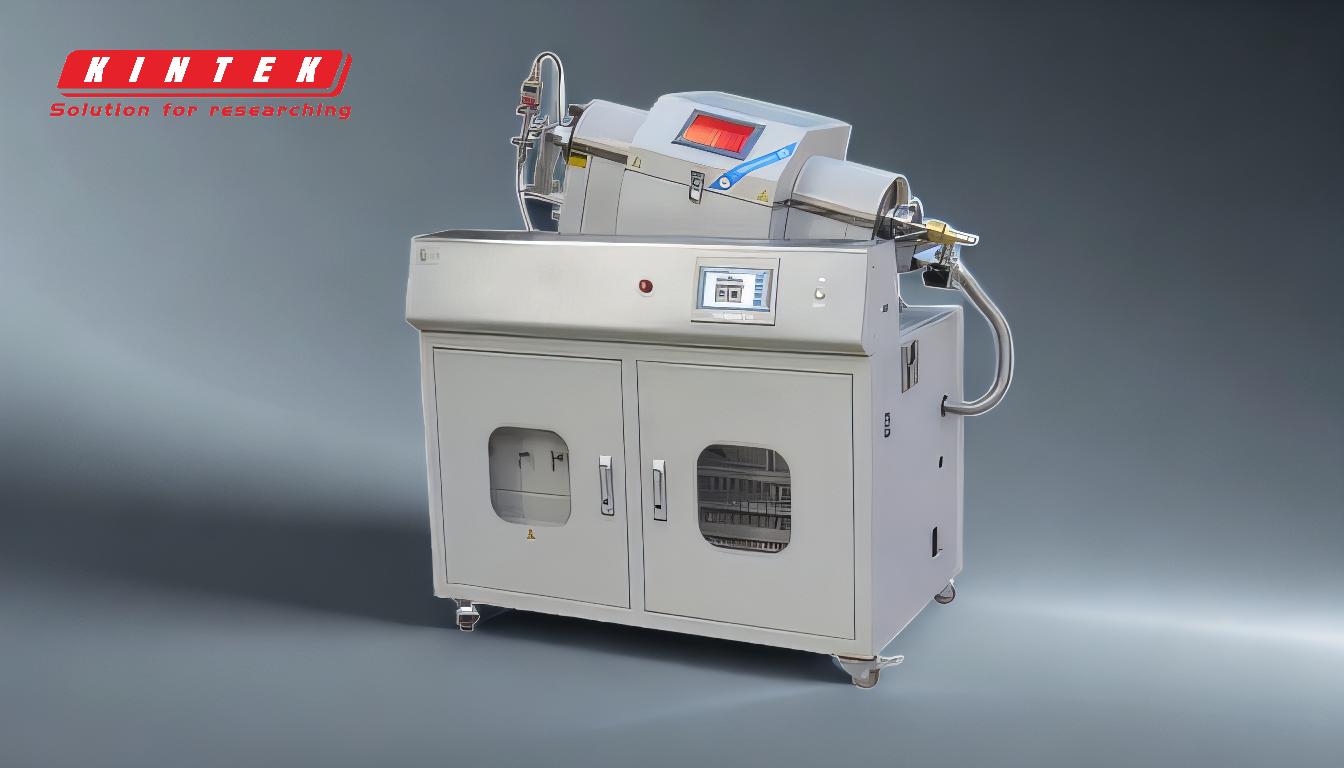
-
合成多组分材料的困难:
- 由于气体到颗粒转换过程中蒸汽压力、成核和生长率的变化,CVD 在制造多组分材料方面面临挑战。这些变化会导致颗粒组成不均匀,从而难以实现统一的材料特性。当试图制造具有特定、明确特征的材料时,这种情况尤为棘手,因为这种工艺会导致最终产品的不一致性。
-
工作温度高:
- CVD 通常在高温下运行,这会导致许多基底材料出现热不稳定性。这就限制了可使用的材料类型,因为某些基底可能会在这些条件下降解或损坏。高温也会增加能源消耗,使工艺变得更加昂贵和不那么环保。
-
有毒和危险的前体:
- 化学气相沉积所需的化学前体通常具有很高的蒸汽压,可能具有剧毒性、挥发性和危险性。处理这些化学物质需要采取严格的安全措施,使用它们会对健康和环境造成重大风险。此外,由于缺乏极易挥发、无毒和不发热的前驱体,使得该工艺更加复杂,在某些应用中更难以使用。
-
有毒和腐蚀性副产品:
- 化学气相沉积的副产品通常具有毒性和腐蚀性,需要仔细中和和处理。这增加了工艺的总体成本和复杂性,因为需要专门的设备和程序来安全处理这些副产品。这些副产品对环境的影响也是一个令人担忧的问题,尤其是在以可持续发展为优先考虑的行业中。
-
大面积涂层的局限性:
- CVD 所用真空室的大小限制了可镀膜表面的尺寸。这使得 CVD 涂层难以应用于大型或复杂的结构,从而限制了它在某些行业的应用。此外,该工艺通常是 "全有或全无",这意味着在某些情况下,对材料进行部分涂层或实现完全覆盖具有挑战性。
-
无法现场施工:
- CVD 通常不能在现场进行,需要将部件运送到涂层中心。这增加了该工艺的物流复杂性和成本,尤其是对于大型或重型部件。由于需要将部件分解成单个组件进行涂覆,这进一步增加了工艺的复杂性,降低了某些应用的效率。
-
生产高质量石墨烯面临的挑战:
- 由于需要多种生长条件,使用 CVD 技术生产单层石墨烯极具挑战性。要获得高质量的石墨烯薄膜,需要对生长机制和最佳条件进行精确控制,而这很难始终如一。这就限制了利用 CVD 技术生产石墨烯的可扩展性和可重复性。
-
硬聚集体的形成:
- 气相沉积过程中的气相团聚会导致形成坚硬的聚集体,从而难以合成高质量的块状材料。在试图制造具有特定机械或结构特性的材料时,这个问题尤其棘手,因为聚集体的存在会损害最终产品的完整性。
总之,虽然 化学气相沉积 虽然化学气相沉积是一种强大的薄膜和涂层沉积技术,但它也有一些明显的缺点,可能会限制其在某些情况下的应用。这些缺点包括材料合成方面的挑战、工作温度高、使用有毒前驱体以及在大表面镀膜方面的局限性。了解这些缺点对于为特定应用选择合适的沉积方法至关重要。
汇总表:
缺点 | 说明 |
---|---|
多组分合成的困难 | 蒸汽压力和生长率的变化导致材料特性不一致。 |
工作温度高 | 基底热不稳定,能耗增加。 |
有毒和危险前体 | 需要采取严格的安全措施,对健康/环境构成风险。 |
有毒和腐蚀性副产品 | 昂贵的中和与处理过程。 |
大面积涂层的局限性 | 受到真空室尺寸的限制,难以进行局部镀膜。 |
无法在现场进行 | 需要运输到涂层中心,增加了物流的复杂性。 |
生产高质量石墨烯的挑战 | 单层石墨烯难以达到一致的生长条件。 |
形成硬聚集体 | 气相中的结块会损害材料的完整性。 |
需要帮助选择正确的沉积方法? 立即联系我们的专家 获取个性化建议!