退火工艺虽然广泛应用于冶金和材料科学领域,以提高金属和合金的性能,但也存在一些局限性。其中包括与温度控制、时间要求、特定材料的挑战、能源消耗和潜在的表面氧化有关的限制。此外,由于微观结构复杂或参数选择不当,退火工艺不一定能达到理想的材料性能。了解这些限制因素对于优化退火工艺和确保特定应用获得理想结果至关重要。
要点说明:
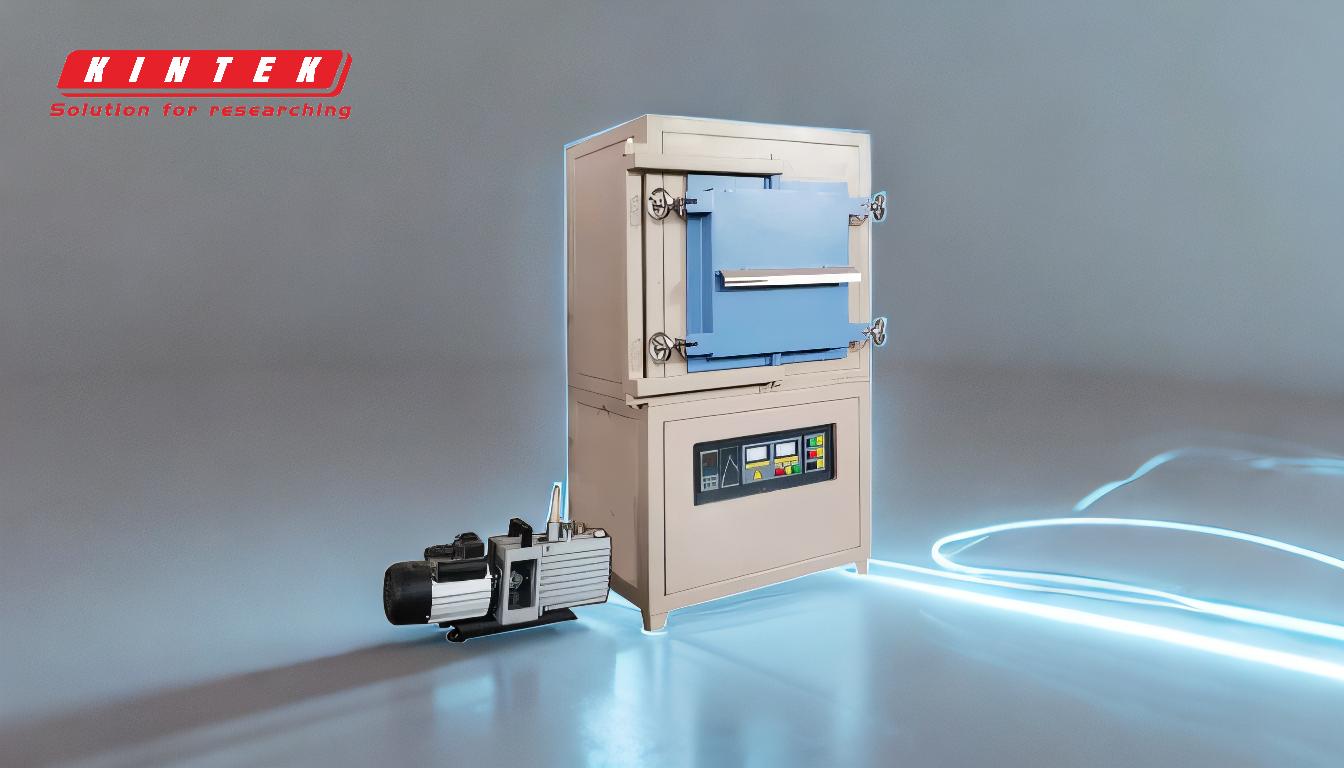
-
温度控制挑战:
- 精度要求:退火需要精确的温度控制,以达到所需的材料特性。稍有偏差就会导致不完全再结晶或晶粒长大问题。
- 设备限制:并非所有窑炉都能在大型或复杂工件上保持均匀的温度,从而导致结果不一致。
- 材料敏感性:某些材料,如高碳钢或某些合金,有效退火的温度范围较窄,使工艺更具挑战性。
-
时间限制:
- 处理时间长:退火通常需要长时间的加热和冷却循环,这对于大批量生产来说既耗时又低效。
- 冷却速率敏感性:某些材料需要慢速冷却,以避免产生内应力,但这会进一步延长加工时间。
-
特定材料的限制:
- 非均匀微结构:成分不均匀或以前加工过的材料可能对退火反应不一致。
- 晶粒生长问题:过度退火会导致晶粒过度生长,降低材料强度和韧性。
- 适用范围有限:某些材料,如非金属复合材料或陶瓷,退火效果并不明显。
-
能源消耗:
- 高能量要求:长时间保持高温会消耗大量能源,使加工过程成本高昂且不环保。
- 批量加工效率低下:批量退火虽然常见,但与连续退火工艺相比能效较低。
-
表面氧化和脱碳:
- 氧化风险:在有氧气的情况下暴露在高温下会导致表面氧化,降低材料质量。
- 脱碳:在钢中,长时间加热会导致表面碳流失,从而降低硬度和耐磨性。
-
工艺复杂性和技能要求:
- 参数优化:选择正确的退火温度、时间和冷却速度需要专业知识和实验。
- 退火后处理:可能需要淬火或回火等附加工艺才能达到所需的性能,从而增加了复杂性。
-
经济和实际限制:
- 设备成本:高质量退火炉和温度控制系统的购买和维护费用可能很高。
- 空间要求:大规模退火操作需要很大的占地面积,这对于较小的设备来说可能是不可行的。
-
结果不一致:
- 材料响应的可变性:即使控制了参数,材料成分或先前加工过程的变化也会导致结果不一致。
- 人为错误:人工控制退火工艺会增加出错的风险,如温度设置或时间安排不正确。
-
对某些性能的改善有限:
- 硬度和强度的权衡:退火通常会降低硬度和强度,以提高延展性,但这并不适合所有应用。
- 对缺陷的影响有限:虽然退火可以减少内应力,但不一定能消除所有缺陷,如空洞或夹杂物。
-
环境和安全问题:
- 热量与排放:高温工艺会产生热量和废气,需要适当的通风和安全措施。
- 工人安全:处理高温材料和操作高温设备会带来安全风险。
通过了解这些限制因素,制造商和工程师可以更好地设计退火工艺、选择合适的材料并实施辅助处理,以达到最佳效果。
汇总表:
限制类别 | 主要挑战 |
---|---|
温度控制 | 精度要求、设备限制、材料敏感性 |
时间限制 | 加工时间长,冷却速度敏感 |
特定材料问题 | 微结构不均匀、晶粒长大、适用性有限 |
能源消耗 | 能耗高,批量处理效率低 |
表面氧化 | 氧化风险、钢材脱碳 |
工艺复杂性 | 参数优化、退火后处理 |
经济限制 | 设备成本、空间要求 |
结果不一致 | 材料反应不稳定,人为错误 |
有限的性能改进 | 硬度-强度权衡,有限的缺陷消除 |
环境问题 | 热量和排放、工人安全风险 |
需要帮助优化退火工艺? 立即联系我们的专家 获取量身定制的解决方案!