石墨烯是由碳原子按六角形晶格排列而成的单层物质,因其卓越的电学、热学和机械特性而备受关注。目前已开发出多种制备石墨烯的方法,每种方法都有自己的优势和局限性。最常见的技术包括机械剥离、化学气相沉积(CVD)、氧化石墨烯还原和碳化硅分解。其中,化学气相沉积法是生产大面积、高质量石墨烯最有前途的方法,而机械剥离法主要用于基础研究。液相剥离和激光烧蚀等其他方法也被采用,但它们往往面临可扩展性和质量方面的挑战。本答案将详细探讨这些方法,重点是它们的工艺、优势和局限性。
要点说明
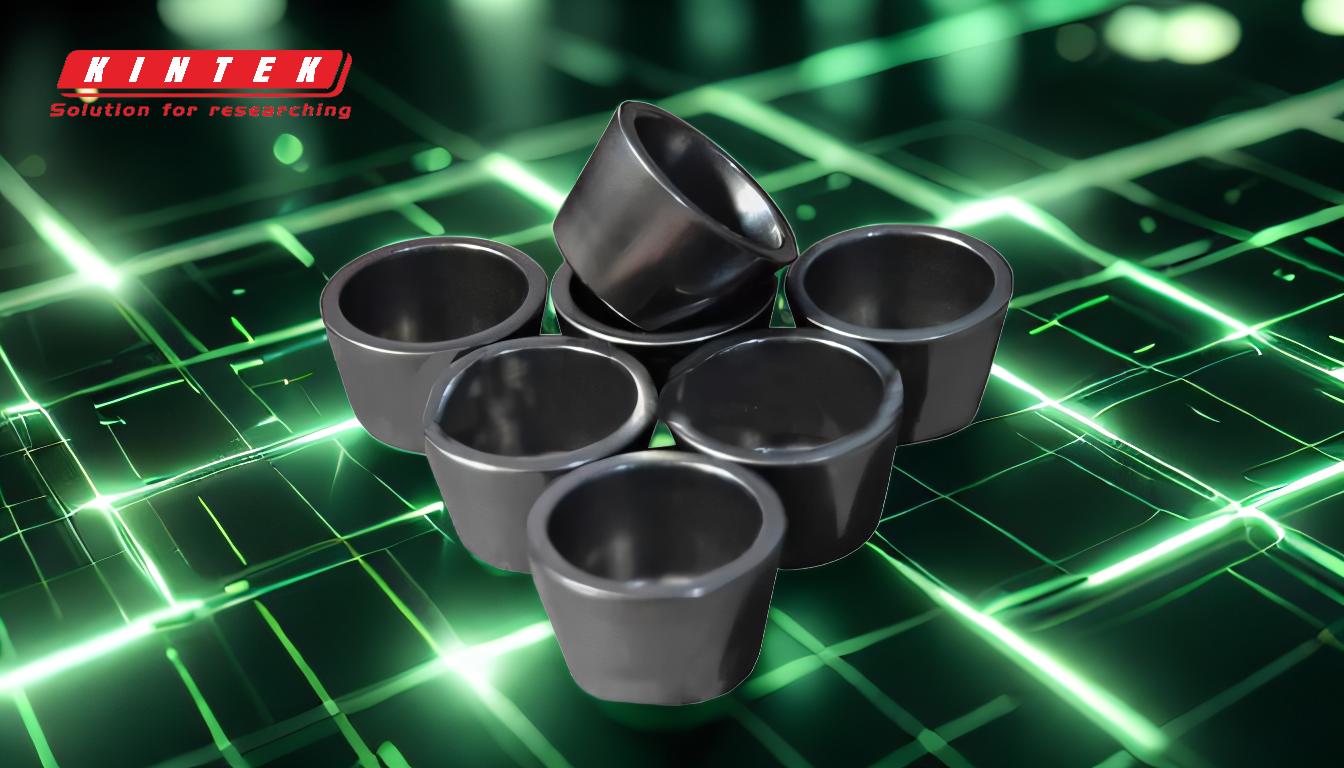
-
机械去角质
- 过程:这种方法是利用胶带或其他机械手段从石墨上剥离石墨烯层。这是一种简单而经济有效的技术。
- 优势:生产出缺陷极少的高质量石墨烯,是基础研究和小规模应用的理想选择。
- 局限性:无法进行大规模生产,只能获得小片石墨烯。
-
化学气相沉积(CVD)
- 过程:CVD 是指在高温下将含碳前驱体(如甲烷)在基底(如铜或镍)上热解。碳原子解离后在基底上形成石墨烯层。
- 优势:能够生产大面积、高质量、具有良好电气性能的石墨烯。适合工业规模生产。
- 局限性:需要精确控制温度、压力和基质条件。使用金属催化剂会引入杂质。
-
氧化石墨烯的还原
- 过程:氧化石墨烯首先通过氧化石墨合成,然后通过化学或热还原生成石墨烯。
- 优势:相对简单、可扩展,适合大规模生产。
- 局限性:由此产生的石墨烯往往含有缺陷和残留氧基,从而降低其电气和机械性能。
-
碳化硅(SiC)的分解
- 过程:将碳化硅加热到高温,使硅原子升华,在表面留下石墨烯层。
- 优势:无需金属催化剂即可生产高质量石墨烯。
- 局限性:由于碳化硅晶圆成本高昂和工艺耗能,因此价格昂贵。大面积生产的可扩展性有限。
-
液相去角质
- 过程:利用超声或剪切力在液体介质中剥离石墨,生成石墨烯薄片。
- 优势:具有可扩展性和成本效益,可大量生产石墨烯。
- 局限性:以这种方式生产的石墨烯通常电学质量较低且含有缺陷。
-
激光烧蚀和电弧放电
- 过程:这些方法包括使用高能激光或电弧蒸发碳源,然后使其凝结形成石墨烯。
- 优势:可生产高纯度石墨烯,污染最小。
- 局限性:复杂的能源密集型流程,可扩展性有限。
-
心血管疾病的基质治疗
- 过程:对铜等基底进行化学处理,以降低催化活性、增大晶粒尺寸并改善表面形态,从而使石墨烯生长得更好。
- 优势:通过减少缺陷和瑕疵,提高 CVD 石墨烯的质量。
- 局限性:增加了 CVD 工艺的复杂性,可能需要额外的后处理步骤。
总之,石墨烯制备方法的选择取决于预期应用。对于高质量、小规模的应用,机械剥离是理想的选择,而对于适合工业用途的大面积、高质量石墨烯,CVD 是最佳选择。氧化石墨烯还原和液相剥离提供了可扩展的替代方案,但往往在质量上大打折扣。碳化硅分解和激光烧蚀是具有特定优势和局限性的利基方法。了解了这些方法,就可以根据所需的石墨烯特性和应用要求做出明智的决策。
总表:
方法 | 优势 | 局限性 |
---|---|---|
机械去角质 | 高质量石墨烯,缺陷极少,是研究的理想材料 | 不可扩展,产生的薄片较小 |
化学气相沉积(CVD) | 大面积、高质量石墨烯,适用于工业用途 | 需要精确控制,金属催化剂可能会引入杂质 |
氧化石墨烯的还原 | 可扩展的简单工艺,适合大规模生产 | 石墨烯含有缺陷,残余氧基降低其性能 |
碳化硅的分解 | 高质量石墨烯,无需金属催化剂 | 昂贵、可扩展性有限、耗能 |
液相去角质 | 可扩展,成本效益高,适合大批量生产 | 石墨烯的低电气质量和缺陷 |
激光烧蚀/弧形放电 | 高纯度石墨烯,污染最小化 | 复杂、能源密集、可扩展性有限 |
心血管疾病的基质治疗 | 提高石墨烯质量,减少缺陷 | 增加复杂性,可能需要额外的后期处理 |
需要帮助选择最适合您的石墨烯制备方法吗? 立即联系我们的专家 获取个性化建议!