沉积碳纳米管(CNT)的三种主要方法是化学气相沉积法(CVD)、激光烧蚀法和电弧放电法。其中,化学气相沉积法因其成本效益、结构可控性和可扩展性而得到最广泛的应用。激光烧蚀和电弧放电是传统方法,但由于成本较高和效率较低,在商业应用中不太受欢迎。为了减少对环境的影响,人们正在探索新兴的方法,如使用绿色或废弃原料。每种方法都有其独特的优势和局限性,因此适合不同的应用和研究环境。
要点说明:
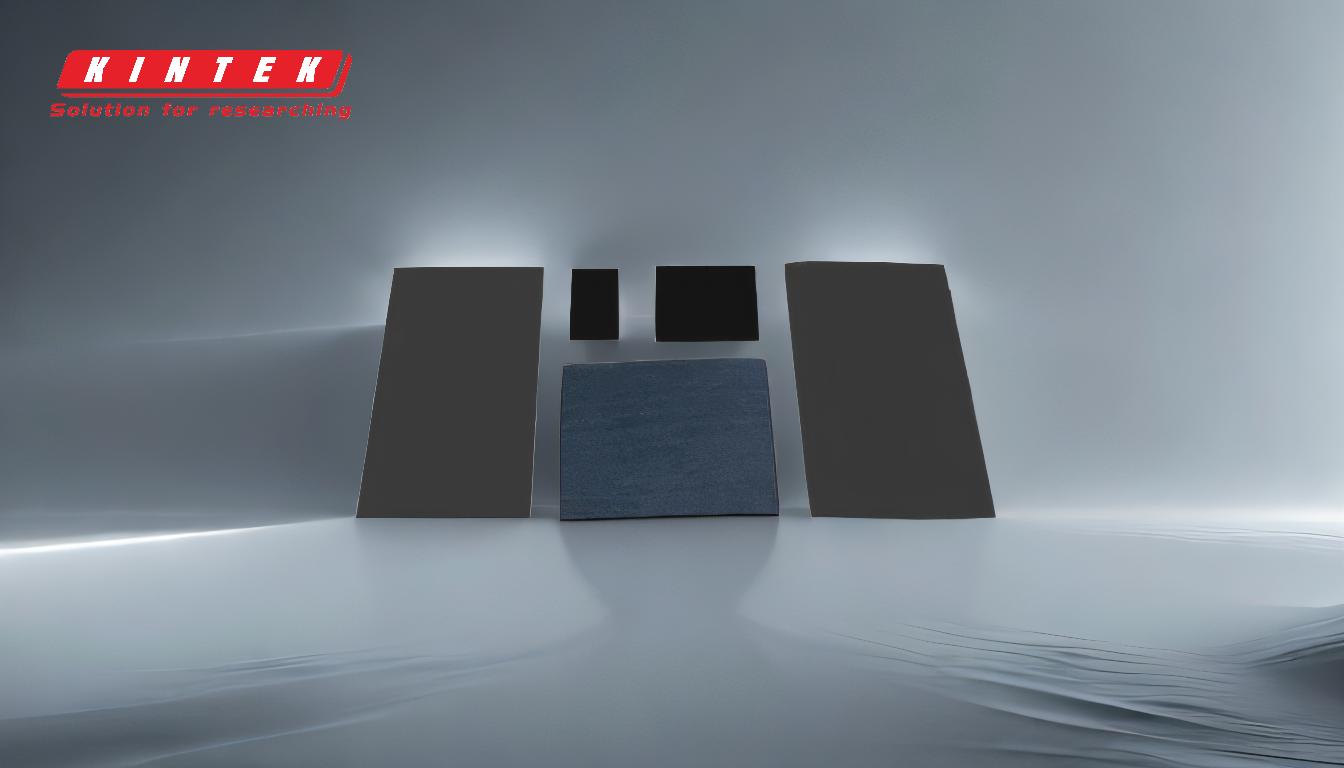
-
化学气相沉积(CVD):
- 过程:CVD 是指在催化剂(通常是金属纳米颗粒)作用下,碳氢化合物气体在高温下分解形成 CNT。
-
优点:
- 结构可控性高,可合成特定直径和长度的 CNT。
- 具有成本效益和可扩展性,使其成为主流商业方法。
- 可进行优化,通过限制材料和能源消耗来减少对环境的影响。
-
局限性:
- 需要精确控制温度和气体流速。
- 由于使用催化剂和碳氢化合物气体,可能会对生态环境造成影响。
-
激光烧蚀:
- 过程:激光烧蚀是指在催化剂的作用下,使用高功率激光使碳靶汽化,从而产生碳纳米管。
-
优点:
- 与其他方法相比,可生产出缺陷较少的高质量 CNT。
- 适用于需要高纯度的研究目的。
-
限制条件:
- 能耗高、成本高,不适合大规模生产。
- 可扩展性和效率有限。
-
电弧放电:
- 过程:电弧放电是指在惰性气体环境中,在两个碳电极之间产生电弧,从而形成碳纳米管。
-
优点:
- 设置简单,成本相对较低。
- 生产的多壁 CNT 具有良好的结构完整性。
-
局限性:
- 产量低,难以控制碳纳米管的尺寸和结构。
- 能耗高,副产品为无定形碳。
-
新兴方法:
- 绿色或废弃原料:新出现的方法侧重于使用可持续原料,如通过熔盐电解或甲烷热解捕获的二氧化碳来生产碳纳米管。
-
优势:
- 利用废料或可再生资源,有可能减少对环境的影响。
- 符合材料科学日益强调的可持续发展。
-
局限性:
- 仍处于研发阶段,商业可行性有限。
- 需要进一步优化,以实现成本效益和可扩展性。
总之,虽然化学气相沉积仍然是最实用、应用最广泛的 CNT 沉积方法,但激光烧蚀和电弧放电对于特定的研究应用也很有价值。使用绿色或废弃原料的新兴方法是减少 CNT 生产对环境影响的一个有前途的方向。
总表:
方法 | 过程 | 优势 | 局限性 |
---|---|---|---|
化学气相沉积(CVD) | 利用催化剂在高温下分解碳氢化合物气体。 | 成本效益高、可扩展、结构可控性强。 | 需要精确控制;潜在生态毒性。 |
激光烧蚀 | 使用高功率激光使带有催化剂的碳目标气化。 | 生产出缺陷较少的高质量碳纳米管。 | 能耗高;可扩展性有限。 |
电弧放电 | 在惰性气体环境中的碳电极之间产生电弧。 | 设置简单;生产的多壁 CNT 具有良好的结构完整性。 | 产量低;能耗高;副产品为无定形碳。 |
新兴方法 | 使用绿色或废弃原料进行可持续 CNT 生产。 | 减少对环境的影响;符合可持续发展目标。 | 商业可行性有限;需要进一步优化。 |
有兴趣进一步了解碳纳米管沉积方法? 今天就联系我们 讨论您的具体需求!