溅射和热沉积是用于不同行业的两种不同的薄膜沉积技术,每种技术都有独特的机制、优势和应用。溅射是利用高能离子将原子从目标材料中物理移出,然后沉积到基底上。这种工艺的工作温度较低,因此适用于对热敏感的材料。另一方面,热沉积依靠加热目标材料来产生蒸汽流,蒸汽流凝结在基底上。这种方法以较高的沉积速率和较短的运行时间而著称,非常适合需要快速镀膜的应用。这些技术之间的选择取决于材料兼容性、所需薄膜特性和生产要求等因素。
要点说明:
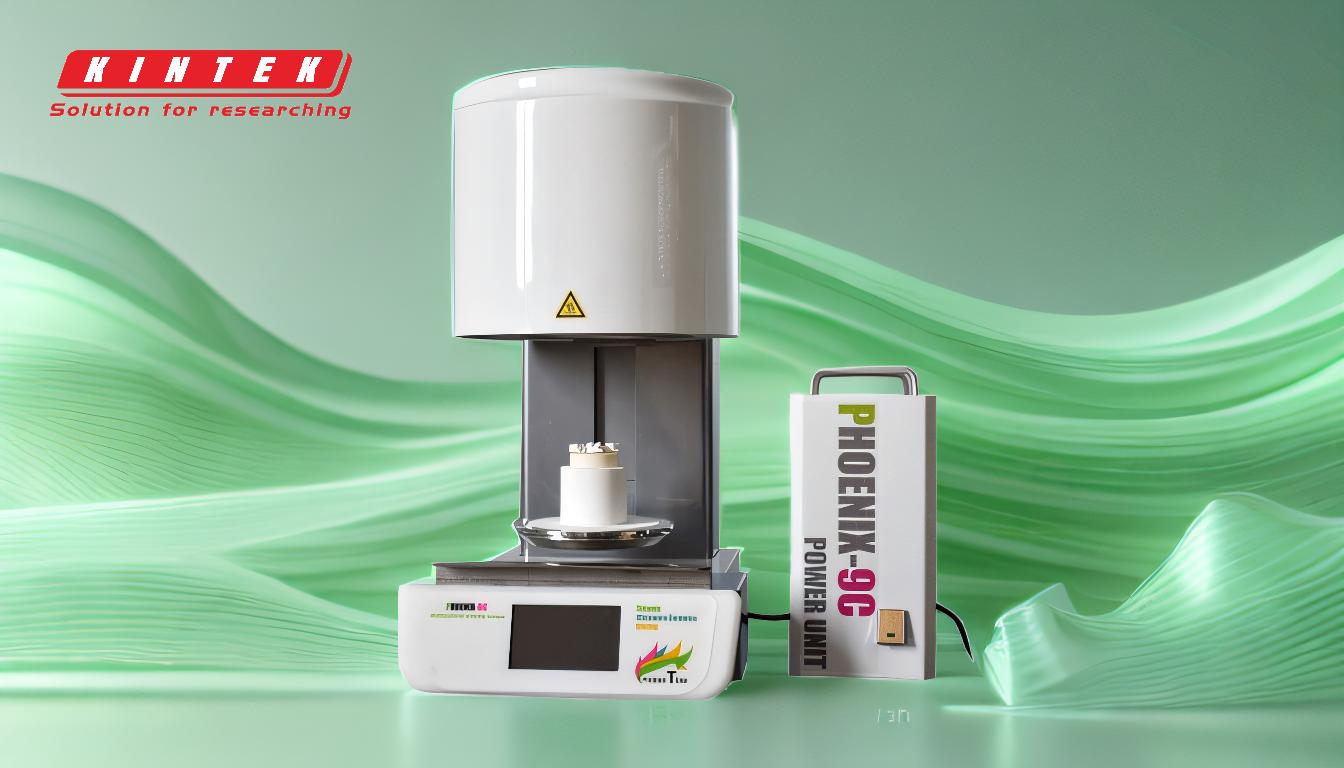
-
沉积机制:
-
溅射:
- 利用在充满受控气体(通常为氩气)的真空室中给阴极通电产生的等离子体。
- 带正电的气体离子被加速冲向目标材料,使原子或分子发生物理脱落。
- 喷出的原子形成蒸汽流,以薄膜的形式沉积在基底上。
-
热沉积:
- 将目标材料加热至蒸发点,形成强大的蒸汽流。
- 蒸汽凝结在基底上,形成薄膜。
- 对于能承受较高温度的材料来说,这种工艺通常更快、更有效。
-
溅射:
-
温度敏感性:
-
溅射:
- 工作温度较低,适用于热敏性材料的涂层,如塑料、有机物和某些金属。
- 非常适合热应力可能损坏基材或改变材料特性的应用。
-
热沉积:
- 需要较高的温度来蒸发目标材料。
- 最适合可承受热应力的基底和材料,如金属和陶瓷。
-
溅射:
-
沉积速率和效率:
-
溅射:
- 喷射单个原子或小原子团,与热方法相比,沉积速度较慢。
- 可精确控制薄膜厚度和均匀性,非常适合需要高质量涂层的应用。
-
热沉积:
- 产生稳定的蒸汽流,从而实现更高的沉积率和更短的运行时间。
- 对于大规模生产或对速度要求较高的应用领域,该设备更为高效。
-
溅射:
-
应用:
-
溅射:
- 常用于电气和光学生产,如制造薄膜晶体管、有机发光二极管和反射涂层。
- 适用于需要精确控制薄膜特性并与热敏基底兼容的应用。
-
热沉积:
- 常用于太阳能电池板制造、玻璃镀膜和金属膜沉积等行业。
- 非常适合需要快速镀膜和高产能的应用。
-
溅射:
-
材料兼容性:
-
溅射:
- 可沉积多种材料,包括金属、合金和陶瓷,无需高温。
- 对于难以热蒸发的材料尤其有效。
-
热沉积:
- 仅限于可蒸发而不会分解或降解的材料。
- 适用于蒸发点明确的金属和简单化合物。
-
溅射:
-
设备和工艺复杂性:
-
溅射:
- 需要专门的设备来产生和控制等离子体,因此工艺更复杂,成本可能更高。
- 在目标材料和基底兼容性方面具有更大的灵活性。
-
热沉积:
- 设备设置更简单,主要涉及加热元件和真空室。
- 更易于进行大批量生产,但材料选择的多样性较少。
-
溅射:
总之,溅射和热沉积是互补的技术,在特定情况下各有优势。溅射技术适用于精密、低温应用和热敏材料,而热沉积技术则因其速度快、效率高和适用于耐高温基底而受到青睐。两者之间的选择取决于项目的具体要求,包括材料属性、所需薄膜特性和生产限制。
汇总表:
特征 | 溅射 | 热沉积 |
---|---|---|
机理 | 利用高能离子将原子从目标材料中分离出来。 | 加热目标材料,形成用于沉积的蒸汽流。 |
温度敏感性 | 在较低温度下工作,适合热敏材料。 | 需要较高温度,适合耐热基底。 |
沉积速率 | 速度较慢,但可精确控制薄膜厚度和均匀性。 | 沉积速度更快,是高吞吐量应用的理想选择。 |
应用 | 电子/光学生产(如有机发光二极管、薄膜晶体管)。 | 太阳能电池板、玻璃镀膜、金属膜沉积。 |
材料兼容性 | 适用于金属、合金、陶瓷和热敏材料。 | 仅限于可蒸发而不降解的材料。 |
设备复杂性 | 需要专门的等离子体生成设备,设置较为复杂。 | 使用加热元件和真空室,设置更简单。 |
需要帮助选择正确的薄膜沉积技术? 立即联系我们的专家 获取量身定制的解决方案!