热压成型是一种通过同时施加热量和压力来塑造材料形状的制造工艺。它通常用于生产复合材料、塑料、陶瓷和金属。该工艺包括将材料放入模具中,加热到特定温度,然后施加压力将其塑造成所需的形状。这种方法可确保均匀的密度、更好的机械性能和精确的尺寸。关键步骤包括材料准备、模具安装、加热、压制、冷却和脱模。热压成型因其高效率和生产高质量部件的能力而广泛应用于汽车、航空航天和电子等行业。
要点说明:
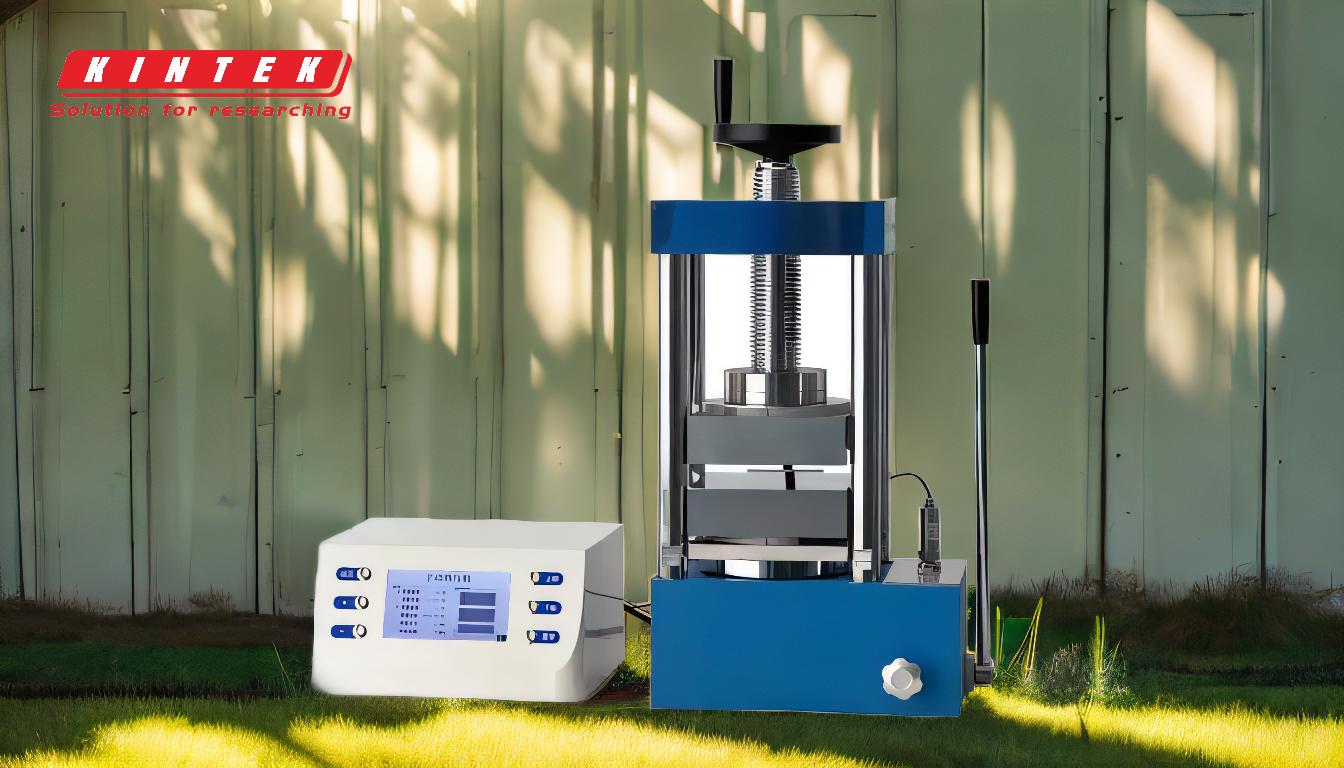
-
材料准备:
- 热压成型的第一步是准备原材料。原材料可以是复合材料、塑料、陶瓷或金属粉末。材料通常经过预处理,以确保均匀性并去除任何杂质。
- 对于复合材料来说,碳纤维或玻璃纤维通常与树脂基体相结合。树脂通常处于半固态,因此可以在压力下流动并填充模具。
-
模具设置:
- 模具是根据最终产品的规格设计的。模具通常由钢材等高强度材料制成,以承受高温高压。
- 模具经过清洁并涂有脱模剂,以防止材料粘在模具表面。这样可以确保在加工后轻松脱模。
-
加热:
- 将材料放入模具内,然后将组件加热到特定温度。温度取决于所使用的材料,对于实现所需的性能至关重要。
- 加热可采用各种方法,包括电加热器、蒸汽或油。加热可以软化材料,使其变得柔韧,更容易在压力下成型。
-
压制:
- 材料达到所需温度后,使用热压机施加压力 热压机 .压力可确保材料完全填充模具,并达到所需的密度和形状。
- 压力的大小取决于材料和模具的复杂程度。高压通常用于消除气穴,确保结构均匀。
-
冷却:
- 压制阶段结束后,对模具进行冷却。冷却可以自然进行,也可以使用水或空气喷射等冷却系统。冷却速度需要控制,以防止最终产品出现翘曲或内应力。
- 适当的冷却可确保材料凝固成所需形状,并保持其机械性能。
-
脱模:
- 材料冷却凝固后,打开模具,取出最终产品。脱模过程中要注意避免损坏产品。
- 产品可能还要经过其他后加工步骤,如修剪、抛光或表面处理,以达到最终规格。
-
应用:
- 热压成型广泛应用于各行各业。在汽车行业,它被用来生产轻质高强的部件,如车身面板和结构件。
- 在航空航天业,热压成型用于生产能承受极端条件的高强度复合材料部件。
- 电子行业使用热压成型生产绝缘部件和电路板。
-
优势:
- 均匀密度:加热和加压可确保材料具有均匀的密度,从而提高其机械性能。
- 精度:热压成型可生产尺寸精确、形状复杂的零件。
- 效率:流程相对较快,可实现自动化,适合大批量生产。
-
局限性:
- 费用:由于需要专门的模具和热压机,热压成型的初始设置成本可能很高。 热压机 .
- 材料限制:并非所有材料都适合热压成型。材料必须能够承受所涉及的高温和高压。
- 复杂性:设计和制造复杂形状的模具具有挑战性,可能需要先进的工程专业知识。
总之,热压成型是一种多功能、高效的制造工艺,具有众多优势,尤其适用于需要高强度和精密部件的行业。然而,它也有一些局限性,在选择它作为制造方法时需要加以考虑。
汇总表:
步骤 | 说明 |
---|---|
材料制备 | 通过预处理准备原材料(复合材料、塑料、陶瓷、金属)。 |
模具安装 | 设计和清洁模具,使用脱模剂以方便脱模。 |
加热 | 将材料加热到特定温度,使其柔韧。 |
压制 | 使用热压机施加压力,使材料成型。 |
冷却 | 冷却模具,使材料凝固,防止翘曲。 |
脱模 | 取出最终产品,必要时进行后处理。 |
应用 | 用于汽车、航空航天和电子领域的高强度部件。 |
优点 | 密度均匀,精度高,大批量生产效率高。 |
局限性 | 初始成本高、材料限制多、模具设计复杂。 |
了解热压成型如何提高您的生产工艺 立即联系我们的专家 !