溅射是一种广泛使用的沉积薄膜的物理气相沉积(PVD)技术,具有高精度、可重现性和与多种材料兼容等优点。虽然与电子束或热蒸发等其他沉积方法相比,溅射法通常被认为具有成本效益,但其成本取决于所用材料的类型、工艺的复杂性和生产规模等因素。溅射法在沉积高熔点材料、获得更好的附着力以及生产具有精确控制特性的均匀薄膜方面尤其具有优势。然而,初始设置成本、维护和能耗会影响其总体费用。对于需要高质量、耐用涂层的应用,尽管溅射法的前期投资比镀金等简单方法高,但它通常是一种具有成本效益的解决方案。
要点说明:
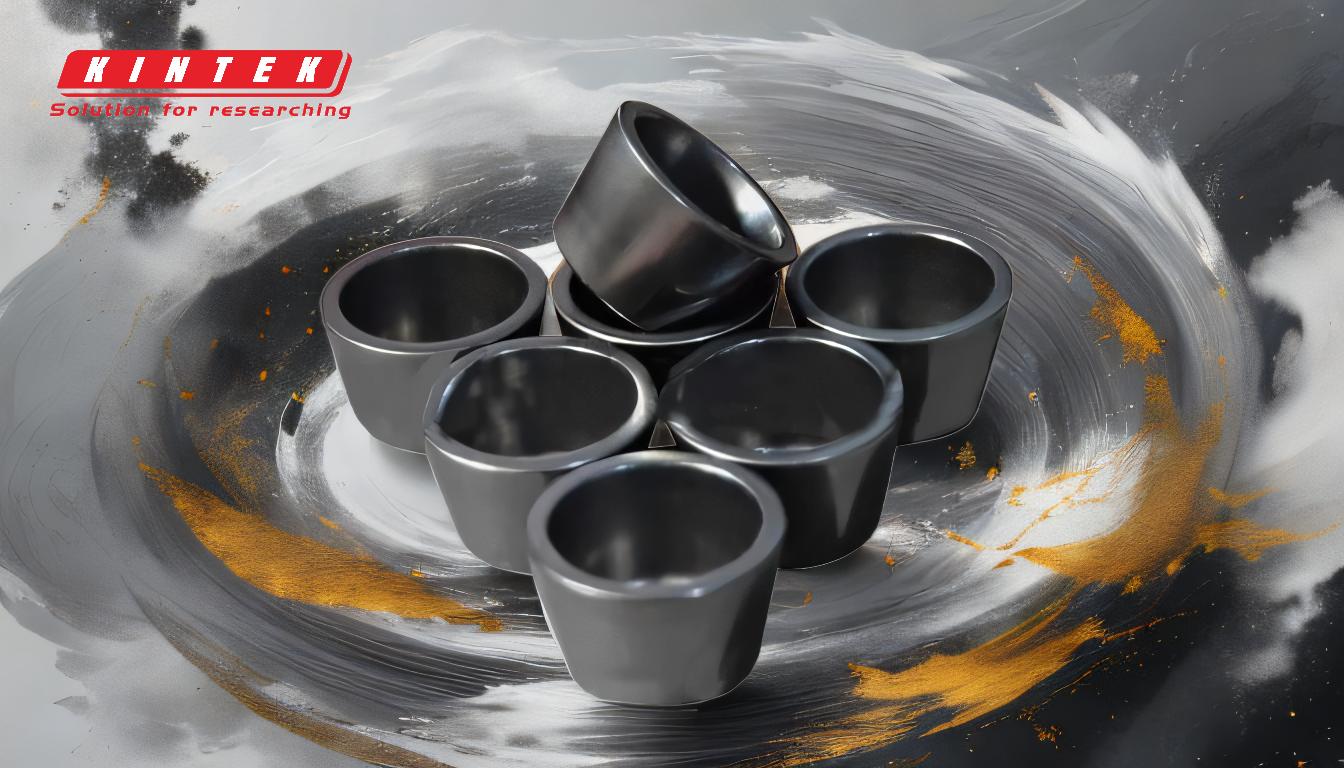
-
与其他沉积方法的成本比较:
- 与电子束或热蒸发等其他沉积技术相比,溅射技术的成本相对较低。
- 它具有更好的可重复性和更简单的工艺自动化,可降低长期运营成本。
- 镀金等方法虽然前期成本较低,但镀层较软且不耐用,因此溅射技术在高性能应用中更具成本效益。
-
材料多样性和效率:
- 溅射可以沉积熔点很高的材料,这些材料很难或根本无法蒸发。
- 它适用于多种材料,包括塑料、有机物、玻璃和金属,从而减少了对多种沉积方法的需求。
- 它能够沉积具有精确成分和特性的薄膜,最大限度地减少了材料浪费,提高了成本效益。
-
工艺优势和成本影响:
- 溅射可提供更好的附着力和更均匀的薄膜,从而减少后处理的需要并提高产量。
- 它无需维护,与反应气体兼容,可长期降低运行成本。
- 在超高真空条件下进行溅射的能力可确保获得高质量的结果,从而证明较高的初始投资是合理的。
-
能耗和生产规模:
- 溅射需要大量能源,尤其是高熔点材料,这会增加运营成本。
- 在大规模生产中,由于规模经济的作用,单位成本会降低,从而使溅射技术在工业应用中更加经济实惠。
- 通过减少缺陷和提高性能,外延生长和分子级精度等先进工艺可进一步提高成本效益。
-
环境和长期成本效益:
- 与涉及有害化学过程的镀金等方法相比,溅射更环保。
- 溅射涂层的耐久性和强度可减少频繁更换或维修的需要,从而长期节约成本。
- 在光学涂层或装饰性表面处理等应用中,精确控制薄膜特性(如颜色和硬度)的能力可增加价值并减少浪费。
-
初始设置和维护成本:
- 由于需要专门的真空系统和靶材,溅射设备的初始投资可能很高。
- 不过,随着时间的推移,该工艺的免维护特性及其与反应溅射等先进技术的兼容性可以抵消这些成本。
- 对于需要高质量、耐用涂层的应用来说,溅射薄膜的卓越性能和使用寿命往往能证明前期成本较高是合理的。
总之,虽然溅射可能涉及较高的初始成本和能耗,但其在材料多样性、工艺效率和长期耐用性方面的优势使其成为许多应用(尤其是那些需要高性能涂层的应用)的具有成本效益的选择。
汇总表:
方面 | 详细信息 |
---|---|
成本比较 | 成本低于电子束或热蒸发;重现性更好。 |
材料多样性 | 适用于高熔点材料、塑料、有机物和金属。 |
工艺优势 | 更好的附着力、均匀的薄膜和免维护操作。 |
能源消耗 | 能耗较高,但在规模化生产中具有成本效益。 |
环境效益 | 与镀金相比更环保;耐用涂层可减少浪费。 |
安装和维护成本 | 前期投资较高,但由于经久耐用,可长期节省成本。 |
有兴趣优化您的薄膜沉积工艺? 立即联系我们 了解溅射技术如何为您的应用带来益处!