物理气相沉积(PVD)和化学气相沉积(CVD)都是广泛使用的薄膜制造技术,但它们在工艺和所产生的特性上有很大不同。物理气相沉积是在真空中蒸发固体材料并将其沉积到基底上,而化学气相沉积则是利用化学反应将气态前驱体沉积成薄膜。与 CVD 相比,PVD 具有多种优势,包括几乎可以沉积任何无机材料和某些有机材料,与基底相比,材料性能更佳,而且比电镀等替代方法更环保。此外,PVD 涂层以其耐用性、耐腐蚀性和优异的耐磨性而著称,适合高温和高冲击应用。另一方面,CVD 擅长不规则表面的保形涂层,通常是需要精确控制薄膜成分和均匀性的应用的首选。然而,PVD 对环境的影响较小,而且在材料沉积方面具有多功能性,因此在许多工业应用中成为首选。
要点说明:
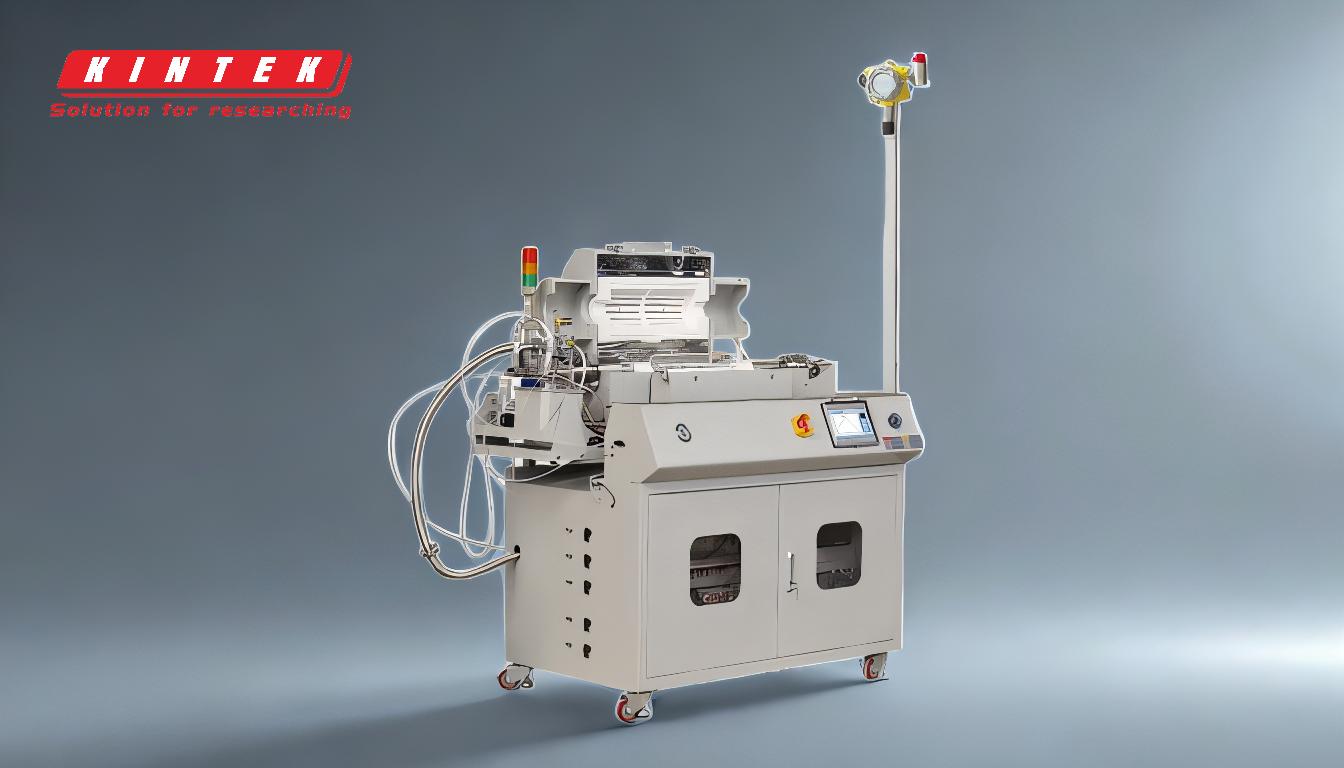
-
材料多样性:
- PVD 几乎可以沉积任何类型的无机材料和某些有机材料,为涂层应用提供了更大的灵活性。这种多功能性使得涂层可以根据基材的需求量身定制具有特定性能的涂层。
- CVD 虽然也具有多功能性,但往往受到前驱体的化学反应性和特定反应条件的限制。
-
改善材料性能:
- 与基底材料相比,PVD 涂层通常具有更高的耐久性、耐腐蚀性和耐磨性。这些特性使 PVD 涂层成为要求在恶劣条件下具有持久性能的应用的理想选择。
- CVD 涂层也能提供出色的性能,但其机械强度和耐磨性可能无法与 PVD 涂层相媲美。
-
环保性:
- PVD 被认为比电镀和喷漆等传统涂层技术更环保。它产生的有害副产品更少,而且不需要使用有毒化学品。
- CVD 虽然有效,但通常需要使用有毒气体,并需要大量的气体管理基础设施,这可能会增加环境和安全问题。
-
耐用性和耐腐蚀性:
- PVD 涂层以其卓越的耐久性和耐腐蚀性而著称,因此适用于高温和高冲击应用。这些涂层很少需要保护性面漆,从而降低了维护和长期成本。
- CVD 涂层也能提供良好的耐腐蚀性,但其耐久性不一定能达到 PVD 涂层的水平,尤其是在高压力环境中。
-
耐磨性:
- PVD 涂层具有优异的耐磨性,非常适合涂层经常磨损的应用。这一特性在汽车、航空航天和工具制造等行业尤为重要。
- CVD 涂层具有良好的耐磨性,但在高磨损环境中,其性能可能无法与 PVD 涂层相媲美。
-
高温和冲击强度:
- PVD 涂层能够承受高温和冲击力,适合在极端条件下使用。这使它们成为航空航天等行业应用的首选,因为这些行业的部件需要承受高应力和温度波动。
- CVD 涂层在高温下也有良好的表现,但其抗冲击性可能不如 PVD 涂层。
-
共形涂层:
- CVD 在保形涂层方面具有优势,因为它可以在表面不规则的基底或大量紧密排列的基底上沉积薄膜。这是由于 CVD 具有较高的压力和层流特性,即使在复杂的几何形状上也能均匀沉积。
- PVD 虽然有效,但通常是一种视线工艺,这意味着它可能无法像 CVD 那样有效地在隐蔽或凹陷区域进行涂层。
-
成本和基础设施:
- PVD 通常需要高真空环境,这会增加初始设置成本。不过,由于减少了维护,涂层的寿命也更长,因此长期成本通常较低。
- CVD 虽然在初始基础设施方面可能成本较低(由于操作压力较高),但在气体管理和安全措施方面可能成本较高,特别是在处理有毒前体时。
总之,与 CVD 相比,PVD 具有多种优势,特别是在材料多样性、材料性能改善、环保和耐用性方面。这些优势使 PVD 成为许多工业应用的首选,尤其是那些需要在极端条件下进行高性能涂层的应用。然而,对于需要保形涂层和精确控制薄膜成分的应用来说,CVD 仍然是一项非常有价值的技术。
汇总表:
指标角度 | PVD | CVD |
---|---|---|
材料多样性 | 几乎可以沉积任何无机材料和某些有机材料。 | 受化学反应性和特定反应条件的限制。 |
耐久性 | 卓越的耐用性和耐腐蚀性。 | 耐久性好,但在高压力环境下可能无法与 PVD 相比。 |
环境影响 | 更环保,有害副产品更少。 | 涉及有毒气体,需要广泛的气体管理。 |
耐磨性 | 卓越的耐磨性,适用于高磨损应用。 | 具有良好的耐磨性,但在高磨损环境中可能无法与 PVD 相媲美。 |
高温使用 | 适用于高温和高冲击应用。 | 高温下性能良好,但可能缺乏抗冲击性。 |
共形涂层 | 受视线工艺的限制 | 适用于不规则表面的保形涂层。 |
成本 | 初始设置成本较高,但长期维护成本较低。 | 初始成本可能较低,但气体管理费用较高。 |
准备好在您的应用中利用 PVD 的优势了吗? 今天就联系我们 了解更多信息!