硬质合金刀片的涂层方法对于提高其性能、耐用性和加工效率至关重要。这些方法包括在硬质合金基体上沉积薄层材料,以提高耐磨性、减少摩擦和增加热稳定性。最常见的涂层技术包括化学气相沉积 (CVD)、物理气相沉积 (PVD) 和两者结合的混合方法。每种方法都有其独特的优势,例如 CVD 具有出色的附着力和厚度,而 PVD 则具有出色的表面光洁度和精度。了解这些方法有助于为特定加工需求选择合适的涂层,确保最佳的工具性能和使用寿命。
要点说明:
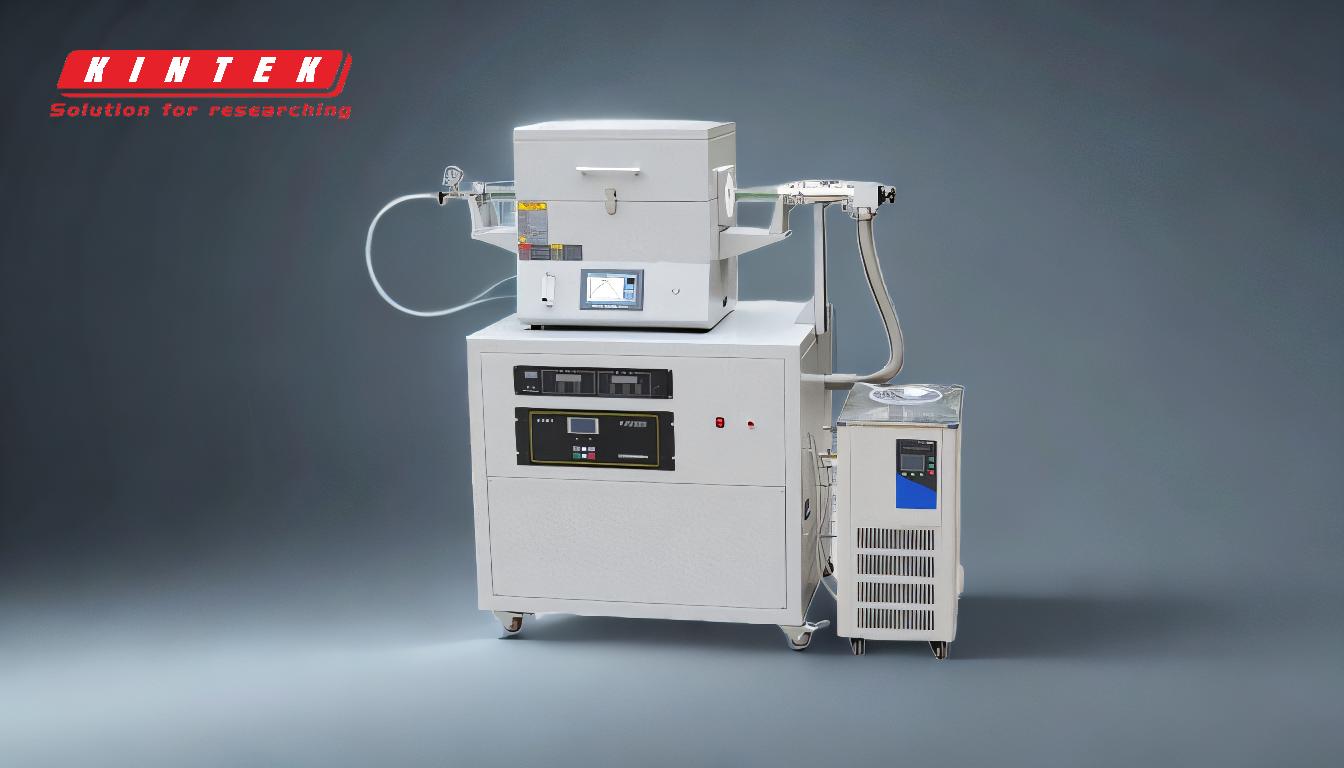
-
化学气相沉积(CVD):
- 过程:CVD 是指气态前驱体在高温(800-1000°C)下发生化学反应,在硬质合金刀片上沉积一层固态涂层。常见的涂层包括氮化钛 (TiN)、碳氮化钛 (TiCN) 和氧化铝 (Al₂O₃)。
-
优点:
- 与基材的附着力极佳。
- 能沉积厚而均匀的涂层(5-15 微米)。
- 热稳定性高,适合高速加工。
- 应用领域:适用于需要高耐磨性的粗加工和半精加工。
-
物理气相沉积(PVD):
- 过程:PVD 包括在真空环境中将材料从靶材物理转移到硬质合金嵌入件。技术包括溅射和电弧蒸发,涂层包括氮化钛铝 (TiAlN) 和氮化铬 (CrN)。
-
优点:
- 可形成较薄的涂层(2-5 微米),表面光滑。
- 沉积温度较低(200-500°C),可降低基底变形的风险。
- 边缘更锋利、更精确,适合精加工。
- 应用范围:适用于表面光洁度和尺寸精度要求较高的精密加工。
-
混合涂层方法:
- 过程:混合方法结合了 CVD 和 PVD 技术,以发挥两种技术的优势。例如,可以先使用 CVD 层来提高耐磨性,然后再使用 PVD 层来提高表面光洁度。
-
优点:
- 结合了 CVD 的厚度和附着力以及 PVD 的精度和光滑度。
- 适用于多种加工应用。
- 应用范围:用于既要求耐用性又要求高精度的复杂加工任务。
-
涂层方法的选择标准:
- 加工条件:考虑切割速度、进料速度和工件材料等因素。CVD 更适合高速、高温操作,而 PVD 则适合精加工。
- 涂层特性:根据应用评估耐磨性、热稳定性和摩擦降低率。
- 成本和效率:平衡涂层成本与预期工具寿命和性能改进之间的关系。
-
涂层技术的新趋势:
- 纳米结构涂层:这些涂层(如纳米复合 TiAlN)具有优异的硬度和热稳定性,可在要求苛刻的应用中提高工具寿命。
- 多层涂层:不同材料的交替涂层(如 TiN/TiCN)可增强韧性和耐磨性。
- 自适应涂层:这些涂层可根据加工条件进行自我调整,以优化性能。
通过了解这些涂层方法及其应用,采购商可以做出明智的决定,选择最适合其特定加工需求的硬质合金刀片,确保提高生产率和成本效益。
汇总表:
涂层方法 | 工艺 | 优势 | 应用 |
---|---|---|---|
化学气相沉积 | 气体前驱体在 800-1000°C 下发生化学反应 | 极佳的附着力、厚涂层(5-15 µm)、高热稳定性 | 粗加工、半精加工 |
PVD | 在 200-500°C 真空条件下进行物理转移 | 薄涂层(2-5 微米)、光滑表面、更高精度 | 精密加工、精加工 |
混合型 | 结合 CVD 和 PVD | CVD 的厚度、PVD 的光滑度、多功能性 | 复杂的加工任务 |
准备好优化您的加工工具了吗? 立即联系我们的专家 为您的硬质合金刀片找到完美的涂层解决方案!