粉末冶金(P/M)是一种多功能制造工艺,具有效率高、成本低、废料少等众多优点。然而,与其他制造方法一样,粉末冶金也并非没有挑战。P/M 零件最常见的缺陷包括弹射裂纹、密度变化、微层和烧结不良。这些缺陷可能产生于 P/M 工艺的不同阶段,包括粉末制备、压制和烧结。要提高 P/M 零件的质量并确保其在汽车和航空航天工业等关键应用中的可靠性,了解这些缺陷至关重要。
要点说明:
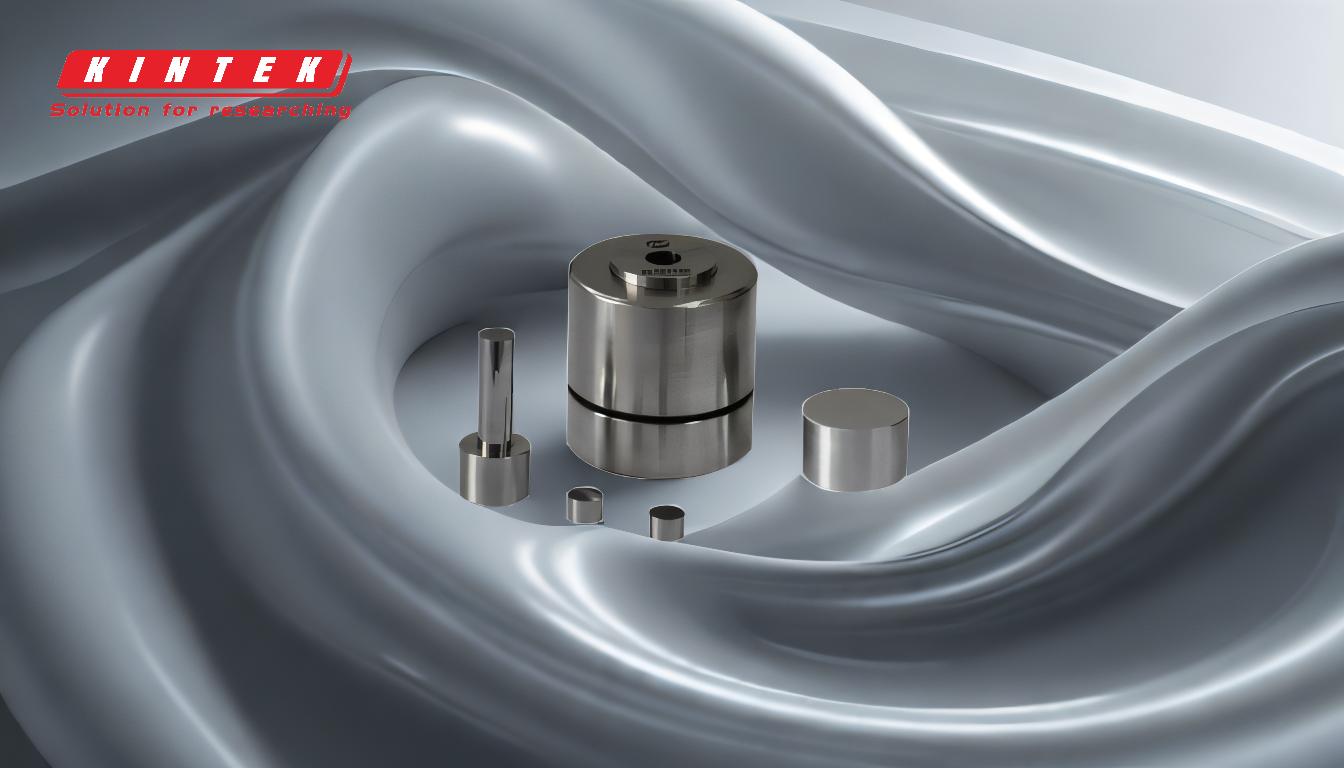
-
弹射裂缝:
- 原因:当压制好的粉末部件从模具中弹出时,就会产生弹射裂纹。部件与模具之间的摩擦力加上压制过程中产生的残余应力会导致裂纹的形成。
- 影响:这些裂纹会破坏部件的结构完整性,导致受力失效。
- 预防措施:适当的模具设计、润滑和控制的顶出力有助于最大限度地减少顶出裂纹的出现。
-
密度变化:
- 原因:密度变化是由于粉末在压制过程中分布不均匀造成的。这可能是由于模具填充不当、压制力不足或粉末特性变化造成的。
- 影响:密度不均匀会导致整个部件的机械性能(如强度和耐磨性)不一致。
- 预防措施:确保粉末分布均匀、优化压制参数和使用优质粉末有助于获得更一致的密度。
-
微层压:
- 原因:微层状结构是粉末颗粒之间的孔隙或不完全结合的薄层。出现这种现象的原因可能是压实压力不足或烧结条件不当。
- 影响:这些缺陷会成为应力集中点,降低零件的疲劳寿命和整体耐用性。
- 预防措施:足够的压实压力、适当的烧结温度和时间对减少微层状结构至关重要。
-
烧结不良:
- 原因:烧结不良的原因是烧结过程中加热不充分。这可能是由于温度不正确、时间不足或气氛控制不当造成的。
- 影响:烧结不良会导致颗粒间的结合力减弱,从而导致零件强度低、机械性能差。
- 预防措施:烧结温度、时间和气氛的精确控制对于确保适当的粘合和达到理想的机械性能至关重要。
-
工艺变化及其对缺陷的影响:
- 传统方法:由于粉末分布和模具设计的限制,传统的 P/M 工艺容易产生密度变化和射出裂纹等缺陷。
- 注塑成型:这种方法可以减少密度变化,但如果控制不当,可能会产生其他缺陷,如翘曲或填充不完全。
- 等静压:这种技术可以生产出密度更均匀的零件,从而降低出现密度相关缺陷的可能性。
- 金属增材制造:作为最新进展,这种方法通过精确的逐层构造有可能减少缺陷,但也带来了新的挑战,如气孔和残余应力。
-
粉末冶金的优点:
- 尽管存在这些缺陷,P/M 仍然具有显著的优势,例如能够高精度地生产复杂形状的产品,材料浪费少,成本效益高。
- 这种工艺对环境友好,所用材料的 97% 都会成为最终产品的一部分,因此是汽车和航空航天等行业的可持续发展之选。
总之,虽然粉末冶金是一种高效、经济的制造工艺,但必须了解并解决常见缺陷,以确保生产出高质量的零件。通过优化粉末/金属加工工艺的每个阶段(粉末制备、压制和烧结),制造商可以最大限度地减少缺陷,提高粉末/金属零件在关键应用中的性能。
汇总表:
缺陷 | 原因 | 影响 | 预防 |
---|---|---|---|
弹射裂缝 | 弹射过程中的摩擦、残余应力 | 结构完整性受损,零件在应力作用下失效 | 适当的模具设计、润滑、可控的顶出力 |
密度变化 | 粉末分布不均匀、模具填充不当、压制不当 | 机械性能(强度、耐磨性)不一致 | 均匀的粉末分布、优化的压制、高质量的粉末 |
微层压 | 压实压力不足,烧结条件不当 | 应力集中、疲劳寿命缩短、耐久性差 | 足够的压实压力、适当的烧结温度和时间 |
烧结不良 | 温度不正确、时间不足、气氛控制不当 | 颗粒间结合力弱、强度低、机械性能差 | 精确控制烧结温度、时间和气氛 |
需要帮助优化粉末冶金工艺? 立即联系我们的专家 获取量身定制的解决方案!