热蒸发是一种广泛使用的物理气相沉积(PVD)技术,但它有几个缺点,会影响其效率、可扩展性和沉积薄膜的质量。主要缺点包括杂质含量高、薄膜质量密度低、薄膜应力适中、难以实现均匀的厚度以及对污染的敏感性。此外,舟裂、热冲击和有限的可扩展性等问题也使其使用更加复杂。虽然其中一些问题可以通过离子辅助或谨慎的电源管理等技术得到缓解,但对于某些应用而言,它们仍然是重大的限制因素。
要点说明:
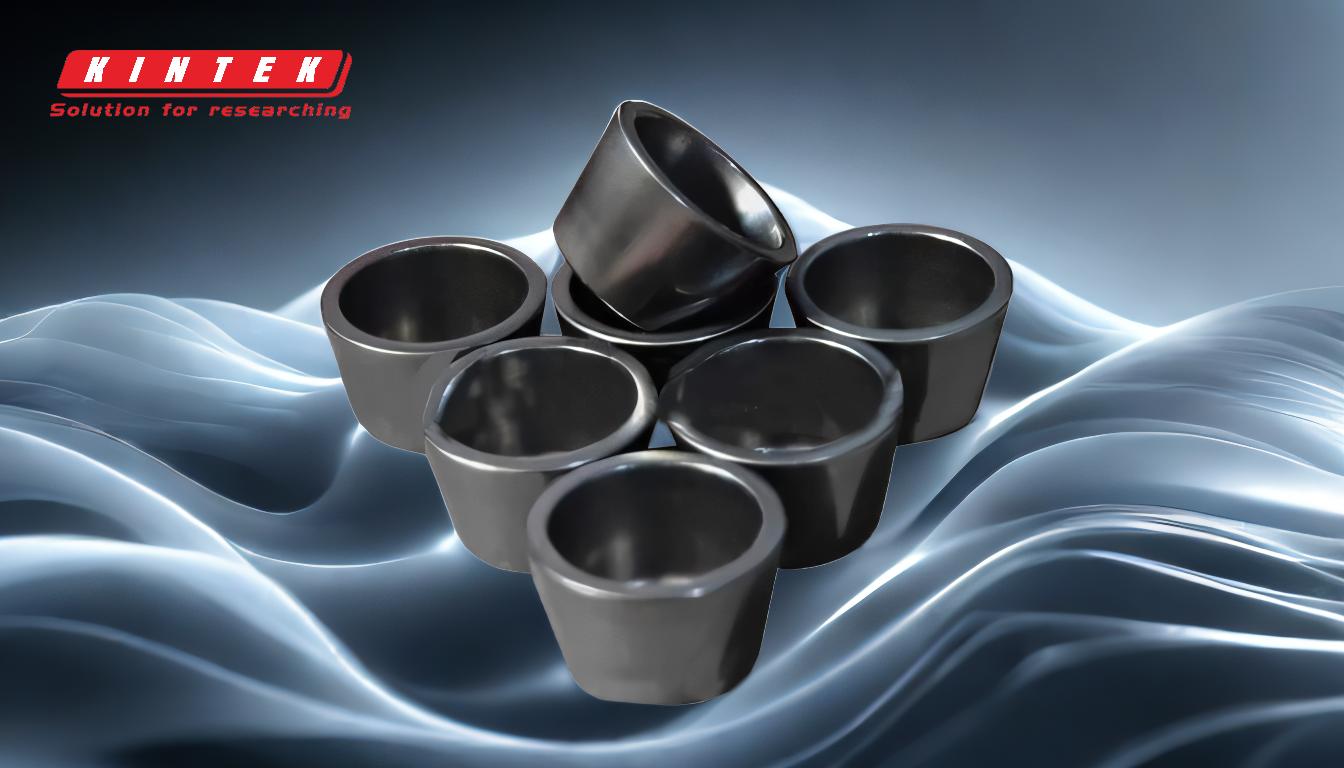
-
杂质含量高
- 众所周知,热蒸发是 PVD 方法中杂质含量最高的一种。这是由于坩埚或舟形材料可能造成污染,尤其是在高温下。
- 通常用于高温蒸发的石墨坩埚会在沉积材料中引入碳杂质。
- 无污染的坩埚价格昂贵,因此要以经济高效的方式获得高纯度涂层具有挑战性。
-
低密度薄膜质量
- 热蒸发法生产的薄膜往往密度较低,这会影响其机械和光学性能。
- 使用离子辅助技术可以部分解决这一问题,但会增加工艺的复杂性和成本。
-
适度的薄膜应力
- 热蒸发通常会产生具有中等应力水平的薄膜,随着时间的推移会导致开裂或分层。
- 这种应力主要是由冷却过程中基底和沉积材料之间的热膨胀不匹配造成的。
-
实现均匀厚度的挑战
- 如果不使用掩膜或行星系统,很难实现均匀的薄膜厚度。
- 这种限制使得热蒸发技术不太适合需要在大型或复杂表面上进行精确、均匀涂层的应用。
-
对污染的敏感性
- 该工艺需要高真空环境,以最大限度地减少污染,这增加了操作的复杂性和成本。
- 坩埚或坩埚舟材料的污染会进一步降低沉积薄膜的质量。
-
舟裂和热冲击
- 船体开裂是船体和蒸发材料在高温下合金化造成的常见问题。舟体一旦开裂,就必须更换,从而增加成本。
- 快速加热和冷却产生的热冲击也会导致艇体开裂。为了缓解这种情况,必须平稳地提升和降低功率,这就增加了工艺的复杂性。
-
可扩展性有限
- 与其他 PVD 方法相比,热蒸发的可扩展性较差,尤其是在沉积速率较低的情况下。
- 这一限制使其不太适合需要高产量的大规模工业应用。
-
温度限制和冷却应力
- 沉积过程受到温度限制的制约,这会影响可蒸发材料的类型。
- 冷却过程中可能会产生不良应力,进一步损害沉积薄膜的完整性。
-
适度的系统复杂性和成本
- 虽然热蒸发系统总体上比其他一些 PVD 方法简单,但仍有一定的复杂性和成本,尤其是在需要离子辅助或行星系统等附加功能时。
-
材料兼容性有限
- 并非所有材料都适合热蒸发,尤其是熔点极高或与坩埚材料发生反应的材料。
- 这就限制了热蒸发技术在某些高级应用中的通用性。
总之,虽然热蒸发是一种用途广泛的沉积技术,但其缺点--如杂质含量高、薄膜密度低、应力适中以及难以实现均匀性--使其不太适合某些高精度或大规模应用。谨慎的工艺优化和辅助技术的使用可以缓解其中的一些问题,但它们仍然是该方法固有的局限性。
汇总表:
缺点 | 说明 |
---|---|
杂质含量高 | 来自坩埚或船只的污染,尤其是在高温条件下。 |
低密度薄膜质量 | 薄膜密度不足,影响机械和光学性能。 |
适度的薄膜应力 | 热膨胀不匹配产生的应力可导致开裂或分层。 |
均匀厚度的挑战 | 没有掩膜或行星系统难以实现。 |
对污染敏感 | 需要高真空环境,增加了复杂性和成本。 |
舟裂和热冲击 | 合金化或热冲击导致开裂,需要谨慎的电源管理。 |
可扩展性有限 | 由于沉积率降低,不太适合大规模应用。 |
温度限制 | 材料限制和冷却压力会影响薄膜的完整性。 |
系统复杂程度适中 | 离子辅助等附加功能会增加成本和复杂性。 |
材料兼容性有限 | 并非所有材料都适用,尤其是高熔点或活性材料。 |
需要帮助优化您的热蒸发工艺吗? 立即联系我们的专家 !