与热蒸发或电子束蒸发等老式方法相比,溅射这种现代真空沉积技术具有多种优势。主要优势包括:可沉积多种材料(包括高熔点材料)、可精确控制薄膜成分和特性、溅射原子动能更高,因而附着力更强,以及可与用于高级工艺的反应气体兼容。此外,溅射的可重复性更高,更容易实现自动化,适合超高真空应用。它还能实现分子级精度,即使在低温条件下也能形成原始界面和具有高堆积密度的均匀薄膜。
要点说明:
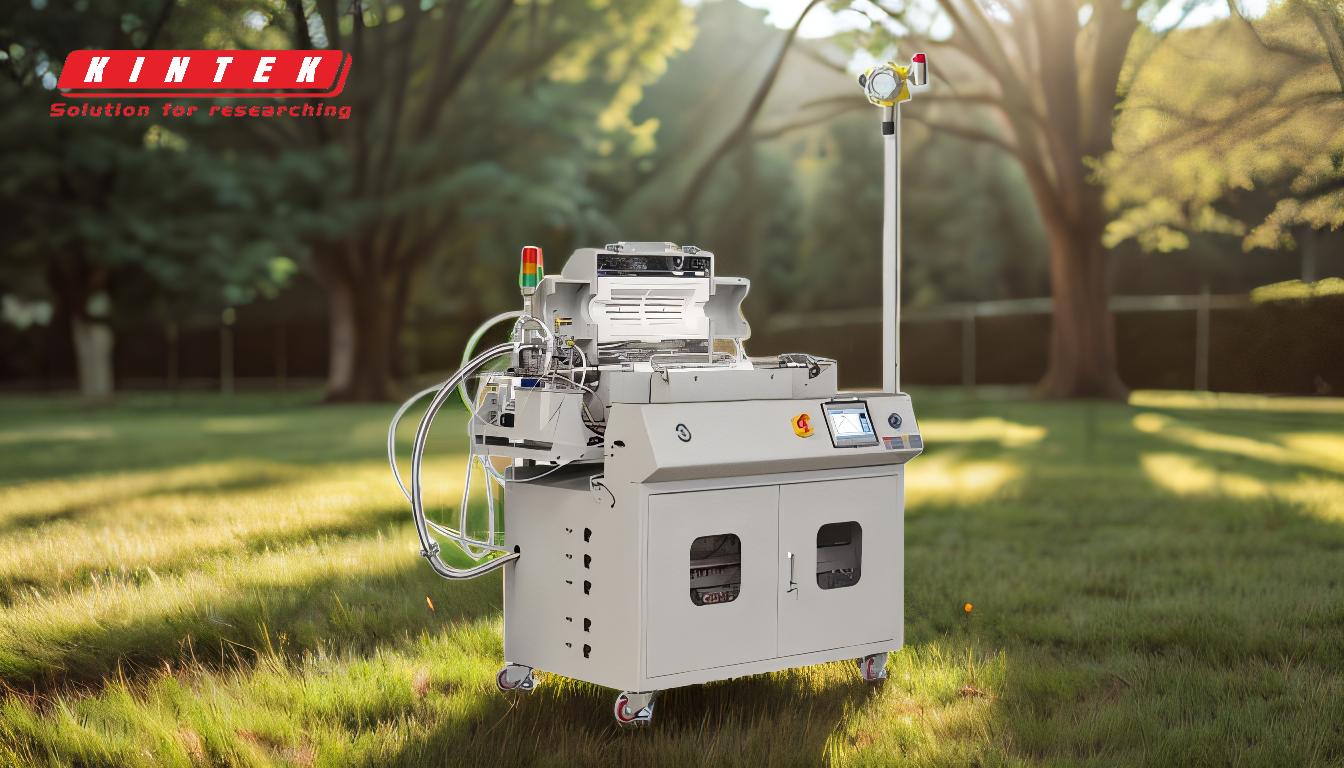
-
各种材料的沉积:
- 溅射可以沉积熔点极高的材料,而使用热蒸发等旧方法很难或根本无法蒸发这些材料。
- 它能很好地处理各种材料,包括金属、合金、化合物、塑料、有机物和玻璃,因此比传统的真空沉积技术用途更广。
-
更好的附着力和薄膜质量:
- 与蒸发材料相比,溅射出的原子具有更高的动能,因此能更好地附着在基底上。
- 即使在低温条件下,溅射产生的薄膜也更均匀、堆积密度更高、表面附着力更好。
-
精度和控制:
- 溅射技术具有分子级精度,可在材料之间形成原始界面。
- 通过控制气体成分、压力和功率等工艺参数,可精确调整薄膜特性。
-
可重复性和自动化:
- 与电子束或热蒸发等老式方法相比,溅射沉积的可重复性高,更易于实现自动化。
- 溅射靶材提供了稳定、长效的气化源,可确保长期获得一致的结果。
-
反应沉积和先进工艺:
- 使用等离子体中活化的反应性气体可轻松实现反应沉积,从而形成具有所需成分的氧化物或氮化物薄膜。
- 溅射与外延生长等先进工艺兼容,可在超高真空条件下进行。
-
成本效益和维护:
- 与其他沉积工艺相比,溅射沉积的成本相对较低。
- 该工艺无需维护,可降低运营成本和停机时间。
-
紧凑灵活的设置:
- 溅射沉积室的容积可以很小,源和基片的距离可以很近,从而最大限度地减少辐射热并简化设置。
- 溅射靶材的形状(如线形、棒形或圆柱形)可根据具体应用进行调整。
-
广泛的材料兼容性:
- 与热蒸发等方法相比,溅射法适用于更广泛的材料,包括混合物和合金。
- 它适用于通过对溅射金属离子进行氧化或氮化来沉积光学薄膜,从而获得所需的薄膜成分。
利用这些优势,溅射技术已成为现代真空沉积的首选方法,与旧技术相比,它具有卓越的性能、灵活性和成本效益。
汇总表:
优势 | 描述 |
---|---|
材料范围广 | 可沉积高熔点材料、金属、合金、化合物等。 |
更好的附着力和薄膜质量 | 更高的动能可确保薄膜均匀一致,附着力极佳。 |
精度与控制 | 分子级精度,实现原始界面和可调薄膜特性。 |
可重复性和自动化 | 可重复性高,易于自动化,且长期保持一致。 |
反应沉积 | 与用于氧化物/氮化物薄膜和先进工艺的反应气体兼容。 |
成本效益 | 相对便宜,无需维护。 |
结构紧凑、设置灵活 | 腔室尺寸小,辐射热最小,可定制目标形状。 |
广泛的材料兼容性 | 适用于各种应用的混合物、合金和光学薄膜。 |
准备好改进您的沉积工艺了吗? 今天就联系我们 了解溅射解决方案的更多信息!