与溅射方法相比,热蒸发方法具有多种优点,特别是在简单性、效率和特定应用的适用性方面。热蒸发涉及在真空中加热材料直至蒸发,使蒸发的原子沉积到基板上,形成薄膜。该方法以其温差小和产品接触时间短而闻名,非常适合热敏产品。它对于除气和重新装载金属电荷也很有效,并且它会在较少的挥发性杂质污染薄膜之前自动终止蒸发。相比之下,溅射涉及用离子轰击靶材料以喷射原子,然后将原子沉积到基板上。虽然溅射具有高度可重复性和环境友好性,但热蒸发通常因其制造合金的能力、简单性和较低的操作复杂性而受到青睐。
要点解释:
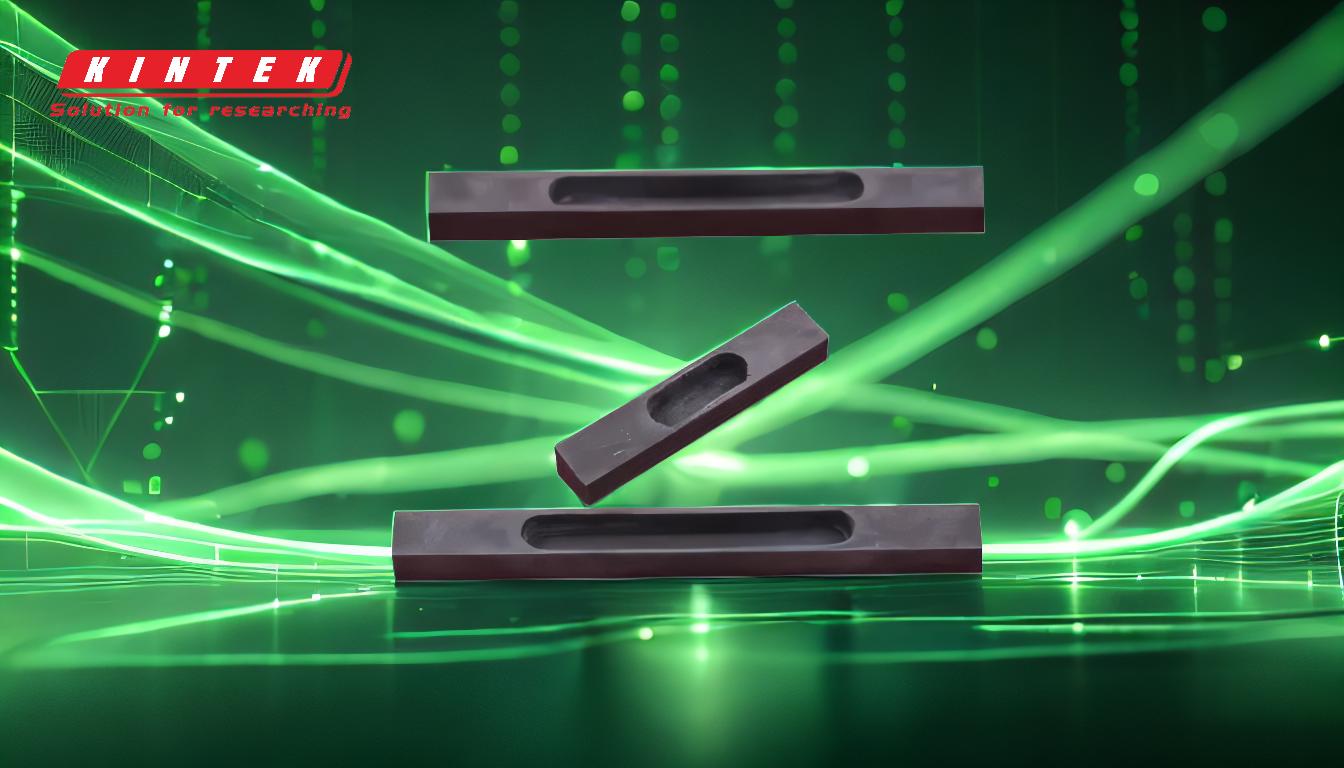
-
简单易用:
- 热蒸发很简单,涉及在真空中加热材料,直到其蒸发并沉积到基材上。与溅射相比,该过程不太复杂,溅射需要精确控制离子轰击和等离子体生成。
- 在热蒸发中使用阻力船或线圈简化了设置,使其更易于操作和维护。
-
效率和排气:
- 热蒸发效率高,能够有效排出材料中的气体,确保沉积过程清洁。这对于需要高纯度薄膜的应用尤其重要。
- 该方法在挥发性较小的杂质蒸发之前自动终止蒸发,确保沉积薄膜的纯度。
-
适用于热敏产品:
- 由于温差小且产品接触时间短,热蒸发非常适合热敏产品。这最大限度地减少了基材或沉积材料的热损坏风险。
-
合金和连续涂层的创建:
- 热蒸发允许使用多种来源来制造合金,从而能够沉积复杂的材料成分。
- 根据镀膜机的配置,可以使用蒸发或溅射进行顺序镀膜,从而提供薄膜沉积的灵活性。
-
工业应用:
- 热蒸发广泛应用于各种工业应用,包括在太阳能电池、薄膜晶体管、半导体晶圆和碳基 OLED 中创建金属键合层。其多功能性使其成为许多薄膜沉积工艺的首选。
-
与溅射的比较:
- 虽然溅射具有高度可重复性并且可以精确沉积少量氧化物、金属和合金,但它更复杂并且需要更精密的设备。
- 另一方面,热蒸发更简单、更具成本效益,并且更适合需要高纯度和最小热影响的应用。
总之,热蒸发方法比溅射方法具有显着的优势,特别是在简单性、效率和热敏应用的适用性方面。其制造合金和执行连续涂层的能力进一步增强了其在薄膜沉积工艺中的多功能性。有关热蒸发的更多详细信息,您可以访问 热蒸发 。
汇总表:
方面 | 热蒸发 | 溅射 |
---|---|---|
简单 | 流程简单,设置复杂性最小。 | 需要精确控制离子轰击和等离子体生成。 |
效率 | 高效除气和自动终止,确保薄膜的高纯度。 | 重现性高,但脱气效率较低。 |
热敏度 | 由于温差较低,非常适合热敏产品。 | 可能会对敏感基材造成热损坏。 |
合金创造 | 允许使用多种来源创建合金。 | 合金制造的灵活性有限。 |
工业应用 | 广泛应用于太阳能电池、薄膜晶体管、半导体晶圆和OLED。 | 适用于氧化物、金属和合金的精确沉积。 |
成本和复杂性 | 成本效益高且操作更简单。 | 比较复杂,需要精密的设备。 |
有兴趣在您的应用中利用热蒸发吗? 立即联系我们的专家 了解更多!