热蒸发和溅射是两种广泛使用的物理气相沉积(PVD)技术,各有不同的机理、优势和局限性。热蒸发依赖于将材料加热到其汽化点,形成强大的蒸汽流,从而实现高沉积率和短运行时间。相比之下,溅射则是用高能离子轰击目标材料,喷射出单个原子或原子团,这种方法的沉积速率较低,但具有更好的均匀性、附着力和材料兼容性。如何选择这些方法取决于所需的沉积速率、材料类型、基底兼容性和应用要求等因素。
要点说明:
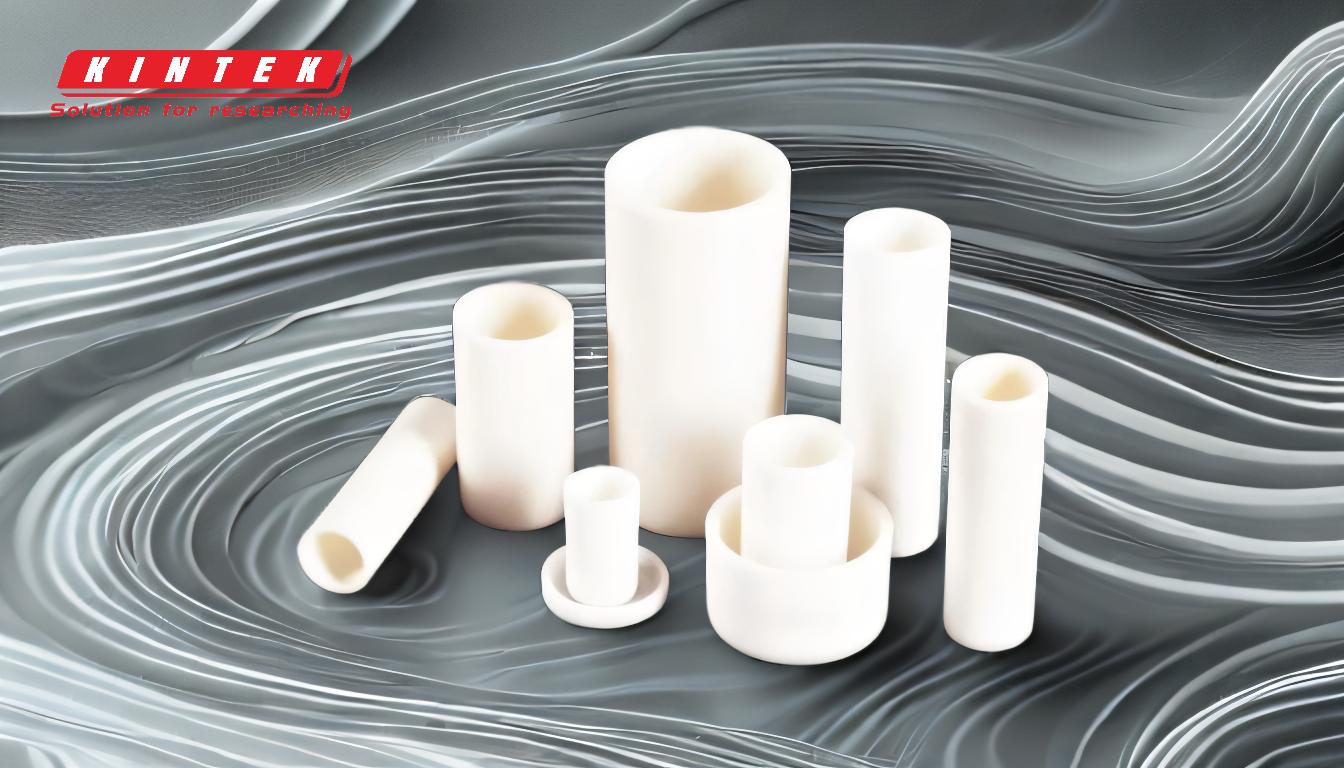
-
沉积机制:
- 热蒸发:该工艺包括在真空中加热源材料,直至其汽化。然后蒸汽在基底上凝结成薄膜。气化所需的高温使这种方法适用于熔点相对较低的材料。
- 溅射:在溅射法中,目标材料在真空室中受到高能离子(通常为氩离子)的轰击。碰撞将原子或原子团撞离靶材,然后沉积到基底上。这种工艺无需加热,因此适用于更多材料,包括塑料和有机物等热敏基底。
-
沉积速率:
- 热蒸发:热蒸发以高沉积率著称,是需要快速涂层工艺的应用领域的理想选择。强大的蒸汽流可确保快速成膜。
- 溅射:一般来说,溅射法由于喷射的是单个原子或小原子团,因此沉积速率较低。不过,这种较慢的工艺通常能使薄膜具有更好的均匀性和附着力。
-
材料兼容性:
- 热蒸发:仅限于能承受高温而不分解的材料。因此,它不太适合热敏基底或熔点较高的材料。
- 溅射:可沉积多种材料,包括金属、合金、陶瓷,甚至塑料和玻璃等热敏基底。该工艺无需高温,因此适用范围更广。
-
薄膜质量和附着力:
- 热蒸发:虽然沉积速率高,但薄膜可能缺乏溅射法所达到的均匀性和附着质量。这对于需要精确薄膜特性的应用来说是一个限制。
- 溅射:生成的薄膜具有极佳的均匀性、附着力和致密性。该工艺的高能特性确保了沉积原子与基底的良好结合,使其适用于高性能涂层。
-
颜色和美学选择:
- 热蒸发:通常仅限于源材料(如铝)的真实颜色。要获得其他颜色通常需要额外的步骤,如喷漆。
- 溅射:通过调节沉积过程,可提供更多的色彩多样性。这使其成为装饰涂层和需要特定美学特性的应用的首选。
-
加工温度:
- 热蒸发:需要高温使源材料气化,这可能会限制其在温度敏感基底上的应用。
- 溅射:工作温度较低,因此适用于塑料、有机物和玻璃等材料的涂层,而不会有损坏的风险。
-
应用范围:
- 热蒸发:常用于对沉积速率要求较高的应用领域,如光学镀膜、太阳能电池和简单金属膜的生产。
- 溅射:适用于要求薄膜质量高、均匀、附着力强的应用领域,如半导体制造、装饰涂层和功能薄膜。
通过了解这些关键差异,设备和耗材采购人员可以根据其应用的具体要求做出明智的决定,确保最佳性能和成本效益。
汇总表:
特征 | 热蒸发 | 溅射 |
---|---|---|
机理 | 在真空中将材料加热至汽化点。 | 用高能离子轰击目标材料,喷射出原子或原子团。 |
沉积速率 | 沉积速率高,是快速涂层工艺的理想选择。 | 沉积速率较低,但均匀性和附着力更好。 |
材料兼容性 | 仅限于低熔点材料;不适用于热敏基底。 | 与金属、合金、陶瓷和热敏材料兼容。 |
薄膜质量 | 与溅射法相比,可能缺乏均匀性和附着力。 | 生产的薄膜具有极佳的均匀性、附着力和密度。 |
颜色选项 | 仅限于源材料的真实颜色。 | 为装饰和美学应用提供更大的色彩多样性。 |
加工温度 | 需要高温,限制了与热敏性基底的配合使用。 | 工作温度较低,适用于塑料、有机物和玻璃。 |
应用 | 光学镀膜、太阳能电池和简单金属膜。 | 半导体制造、装饰涂层和功能薄膜。 |
需要帮助选择适合您应用的 PVD 技术吗? 立即联系我们的专家 获取个性化指导!