真空浇注和注塑成型是用于生产塑料或树脂零件的两种不同制造工艺,各有其优势、局限性和应用。真空浇注是一种低压工艺,非常适合原型设计和小批量生产,可提供高细节和材料多样性。另一方面,注塑成型是一种高压工艺,适合大规模生产,具有高精度、可重复性和成本效益。两者之间的选择取决于生产量、材料要求、预算和所需零件质量等因素。下面将详细介绍这两种工艺的主要区别。
要点说明
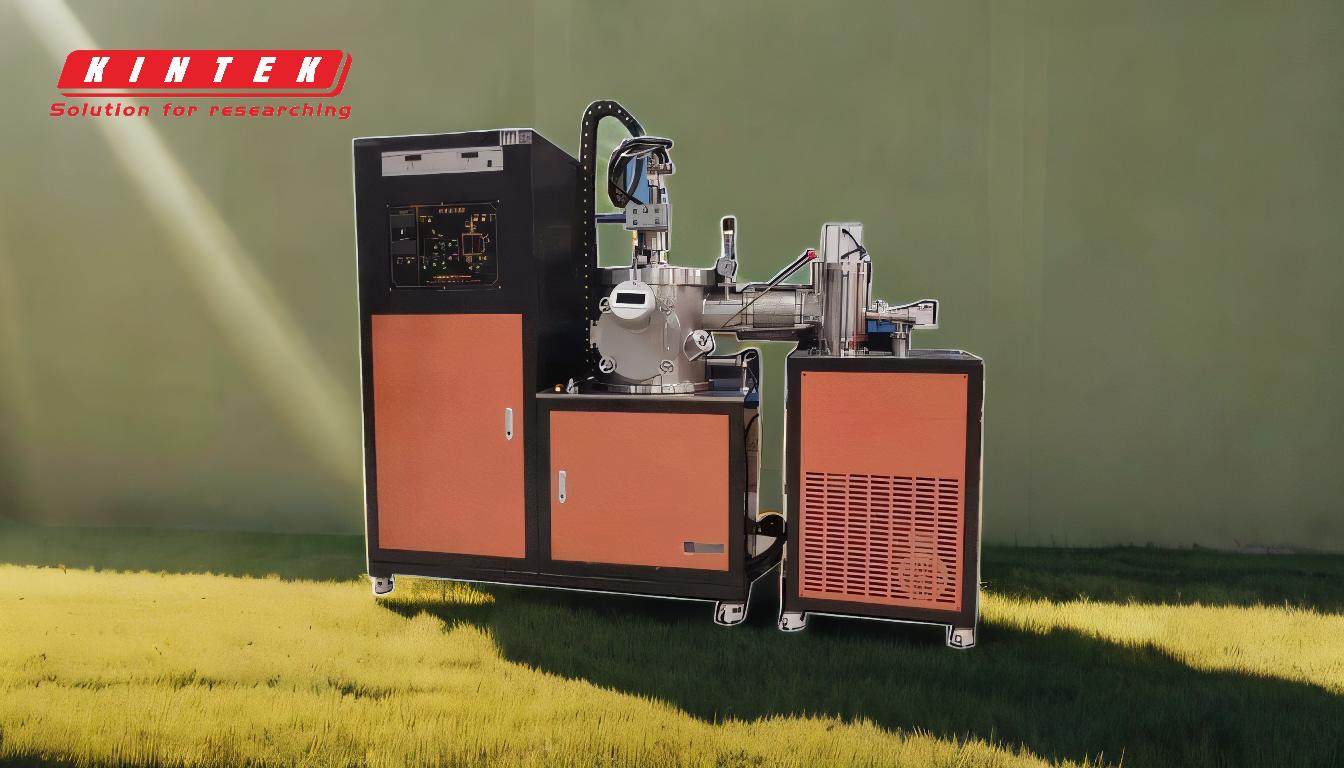
-
流程机制:
-
真空铸造:
- 使用根据母模(通常是 3D 打印)制作的硅胶模。
- 将液态树脂倒入模具中,然后用真空去除气泡,确保表面光滑细致。
- 然后将模具放入烘箱中固化,使树脂凝固。
-
注塑成型:
- 包括在高压下将熔融塑料或树脂注入钢模或铝模。
- 材料在模具内冷却凝固后,零件被顶出。
- 这一过程高度自动化,可重复进行。
-
真空铸造:
-
生产量:
-
真空铸造:
- 最适合中低产量(通常为每个模具 10-50 个零件)。
- 硅胶模具会随着时间的推移而退化,从而限制了可生产零件的数量。
-
注塑成型:
- 专为大批量生产(数千到数百万个零件)而设计。
- 金属模具经久耐用,可以承受无数次循环而不会出现明显磨损。
-
真空铸造:
-
材料选择:
-
真空铸造:
- 提供各种聚氨酯树脂,可模拟各种工程塑料(如 ABS、PP、PC)。
- 仅限于可在相对较低温度下固化的材料。
-
注塑成型:
- 与各种热塑性塑料和某些热固性材料兼容。
- 可处理 PEEK、尼龙和聚碳酸酯等高性能材料。
-
真空铸造:
-
成本考虑因素:
-
真空铸造:
- 硅胶模具价格低廉,降低了初始成本。
- 由于模具退化和人工劳动,生产量较大时单位成本较高。
-
注塑成型:
- 模具(金属模具)前期成本高。
- 通过自动化和提高材料效率,降低大批量生产的单位成本。
-
真空铸造:
-
部件质量和精度:
-
真空铸造:
- 生产出表面光洁度极佳、细节精致的零件。
- 由于手工操作和模具的灵活性,可能会出现细微的差异。
-
注塑成型:
- 实现所有部件的高精度和一致性。
- 适用于复杂几何形状和公差要求严格的场合。
-
真空铸造:
-
准备时间:
-
真空铸造:
- 模具制作周期更短(通常为 1-2 周)。
- 适用于快速原型和快速周转项目。
-
注塑成型:
- 模具设计和制造周期较长(数周至数月)。
- 只有在大规模生产时才经济实惠。
-
真空铸造:
-
应用:
-
真空铸造:
- 是原型设计、功能测试和小批量生产的理想之选。
- 常用于汽车、消费电子和医疗设备等行业。
-
注塑成型:
- 最适合大规模生产消费品、汽车零部件和工业零件。
- 广泛应用于需要大批量、稳定输出的行业。
-
真空铸造:
-
环境影响:
-
真空铸造:
- 与注塑成型相比,产生的废料更少。
- 硅胶模具不可回收利用,但加工过程中使用的能源较少。
-
注塑成型:
- 会产生大量材料浪费(如浇口和流道)。
- 由于需要高压机械和加热,因此能源密集。
-
真空铸造:
通过了解这些关键差异,制造商和设计人员可以在平衡成本、产量、材料和零件质量等因素的基础上,就哪种工艺最适合其特定需求做出明智的决定。
总表:
方面 | 真空铸造 | 注塑成型 |
---|---|---|
流程机制 | 使用硅胶模具,真空去除气泡,树脂在烤箱中固化。 | 在高压下将熔融塑料注入金属模具。 |
生产量 | 低到中等(10-50 份/模)。 | 大批量(数千到数百万个零件)。 |
材料选择 | 模仿工程塑料的聚氨酯树脂。 | 各种热塑性塑料和高性能材料(如 PEEK)。 |
成本考虑因素 | 初始成本较低,批量较大时单位成本较高。 | 前期模具成本高,批量生产单件成本低。 |
部件质量 | 表面光洁度极佳,因手工操作而略有差异。 | 精度高、一致性好、公差小。 |
准备时间 | 时间更短(1-2 周制作模具)。 | 时间较长(模具制造需要数周至数月)。 |
应用 | 原型设计、功能测试、小批量生产。 | 消费品、汽车和工业零部件的大规模生产。 |
环境影响 | 减少浪费,降低能耗,硅胶模具不可回收。 | 大量材料浪费,能源密集型工艺。 |
还不确定哪种工艺最适合您的项目? 立即联系我们的专家 获取个性化建议!