回转炉的效率是影响其运行的一个关键因素,尤其是在能耗和热性能非常重要的工业领域。回转炉广泛用于熔化、热解和材料处理等工艺,但其效率普遍较低,从 23% 到 27.5% 不等。效率低的主要原因是废气造成大量热量损失,废气温度可达 1100°C 至 1315°C。然而,混合和输送技术的进步,如阿基米德螺旋的使用,提高了体积利用率和热传递,从而提高了整体效率。此外,炉温、停留时间和压力控制等因素在优化性能方面也起着至关重要的作用。将回转炉与热交换设备相结合是一种新兴趋势,可进一步提高效率并降低运营成本。
要点说明:
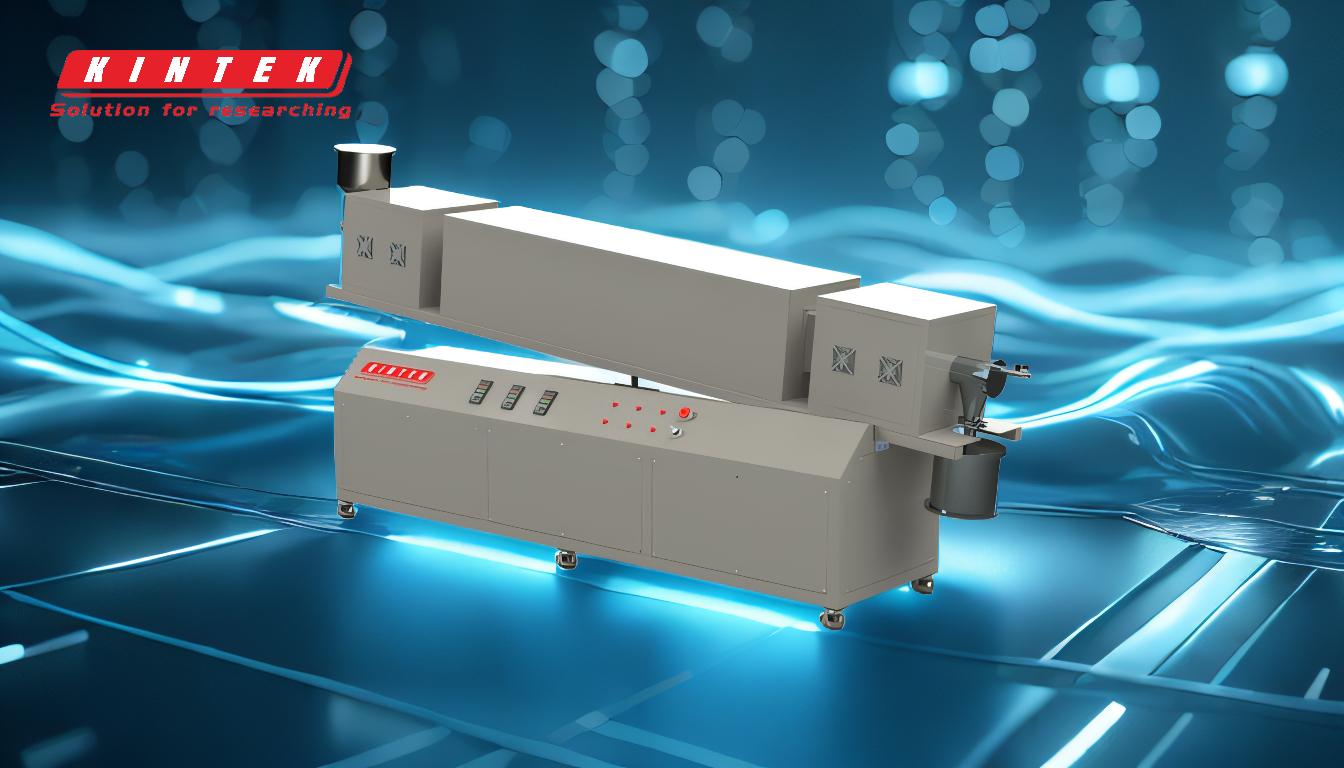
-
回转炉的热效率:
- 回转炉的热效率通常为 23% 至 27.5%,与其他工业设备相比相对较低。
- 很大一部分热量(50%-70%)通过废气散失,废气在高温(1100-1315°C)下排出炉外。
- 这种热量损失是造成回转炉整体效率较低的主要原因。
-
影响效率的因素:
- 炉温:炉子的工作温度直接影响效率。较高的温度可以提高反应速率,但也可能增加热量损失。
- 停留时间:材料在炉内停留的时间会影响反应的完整性。适当控制停留时间可确保最佳传热和反应效率。
- 压力:内部压力条件会影响炉内气体和材料的行为,从而影响热量分布和反应动力学。
-
技术进步:
- 混合技术:阿基米德螺旋等创新技术可增强混合效果,缩短热量和质量传递受限反应所需的时间。这提高了容积利用率和整体效率。
- 热交换集成:将回转炉与热交换设备相结合,可以回收废热,提高效率,降低能耗。
-
操作和维护注意事项:
- 正确的操作和维护对保持效率至关重要。定期维护可确保窑炉在最佳条件下运行,最大限度地减少能源浪费并延长设备寿命。
- 监测和控制温度、停留时间和压力等关键参数对实现高效率至关重要。
-
优缺点:
- 优点:回转炉可以处理其他类型炉子难以处理的低等级废料和渣滓。这使它们在各种工业应用中具有广泛的用途。
- 缺点:它们的效率通常较低,维护要求较高,并且会产生大量必须妥善处理的有害废物(盐饼)。
-
新趋势:
- 将回转炉与先进的热交换系统集成的趋势日益明显。这种组合提高了效率,降低了运营成本,并使窑炉设计更加紧凑。
通过解决这些关键问题,运营商可以更好地了解影响回转炉效率的因素,并实施优化其性能的策略。
汇总表:
关键因素 | 详细信息 |
---|---|
热效率 | 23% 至 27.5%,通过废气(1100-1315°C)损失 50-70% 的热量。 |
影响效率的因素 | - 炉温 |
- 停留时间
- 压力控制 | 技术进步
- | 阿基米德螺旋技术 用于余热回收的热交换集成系统 | 优势 | 处理低级废料和渣滓,可广泛用于工业应用。| | 缺点
| 效率较低、维护成本较高、产生有害废物。 | | 新趋势