物理气相沉积(PVD)和化学气相沉积(CVD)是两种广泛应用于基底薄膜涂层的技术。虽然这两种方法都旨在增强表面特性,但它们在机理、操作条件和所产生的涂层特性方面存在很大差异。PVD 通常是在真空条件下将材料从固体源物理转移到基体上,而 CVD 则是依靠气态前驱体与基体之间的化学反应形成涂层。这些差异会影响涂层厚度、均匀性、温度要求和材料兼容性等因素。
要点说明:
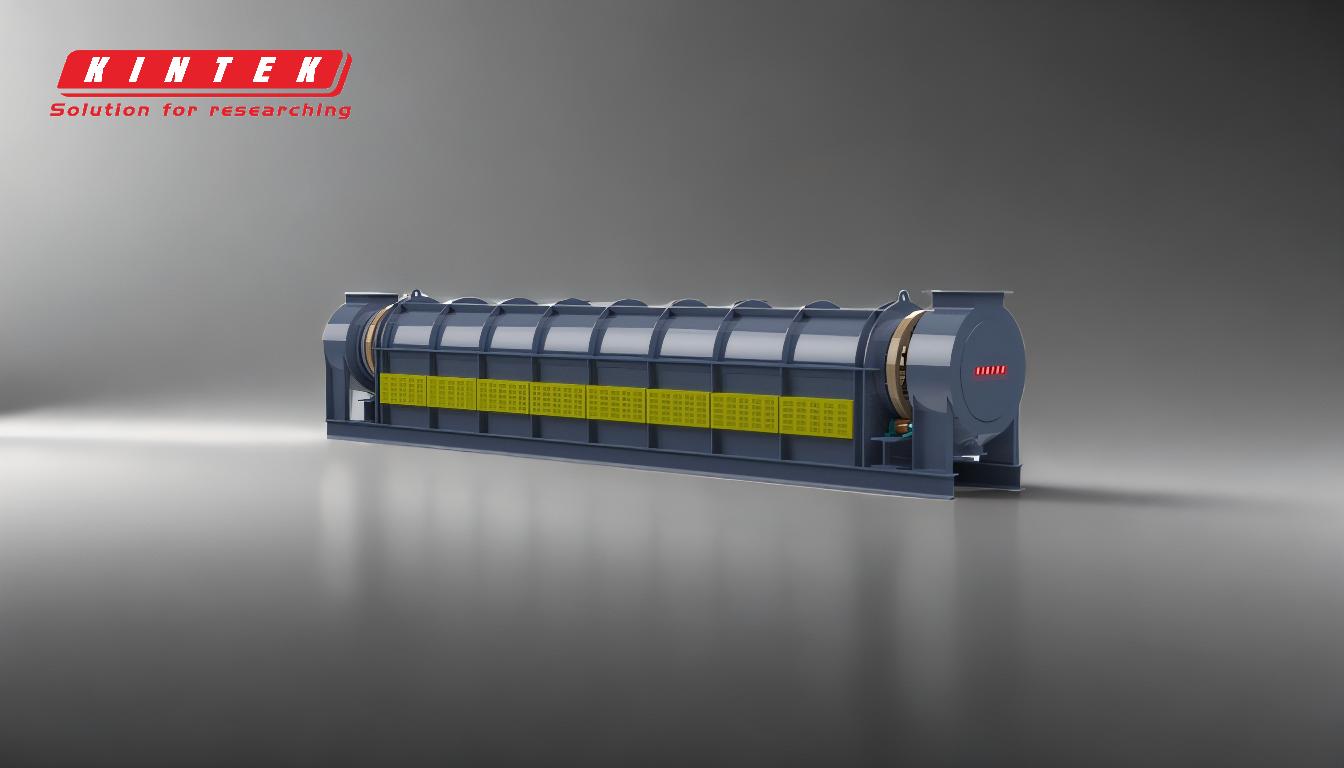
-
沉积机制:
- PVD:PVD 是一种视线工艺,材料从固体靶材中物理气化并沉积到基底上。该工艺不涉及目标材料和基底之间的化学反应。相反,原子或分子从目标材料中喷射出来,凝结在基底表面。
- CVD:CVD 涉及气体前驱体与基底之间的化学反应。气体在基底表面发生反应,形成固体涂层。该工艺具有多向性,这意味着涂层可以覆盖复杂的几何形状和隐蔽区域。
-
工作温度:
- PVD:PVD 的工作温度通常较低,从 250°C 到 500°C。因此,它适用于无法承受高温的基底。
- CVD:CVD 需要更高的温度,通常在 450°C 至 1050°C 之间。高温是推动形成涂层的化学反应所必需的。不过,这也限制了它在对温度敏感的材料上的应用。
-
涂层厚度和均匀性:
- PVD:PVD 镀膜通常较薄(3~5μm),而且由于工艺的视线特性,均匀性较差。不过,它们的应用速度更快,而且可以获得超硬薄膜。
- 化学气相沉积:CVD 涂层更厚(10~20μm)、更均匀,因为化学反应可以更好地覆盖复杂的形状。该工艺虽然速度较慢,但能产生更致密的涂层。
-
材料兼容性:
- PVD:PVD 可以沉积多种材料,包括金属、合金和陶瓷。这种多功能性使其适用于各种应用。
- CVD:由于所涉及化学反应的性质,CVD 通常仅限于陶瓷和聚合物。就材料兼容性而言,它的通用性较差。
-
应力和表面特性:
- PVD:PVD 涂层通常会产生压应力,从而提高涂层的耐久性和附着力。该工艺还能使表面更加光滑。
- CVD:CVD 涂层由于加工温度高,可能会产生拉伸应力,从而导致细微裂纹。涂层密度较高,但可能需要进行后处理才能达到平滑。
-
应用:
- PVD:PVD 通常用于需要薄而硬涂层的应用,如切削工具、装饰性表面和耐磨表面。
- CVD:对于需要厚而均匀涂层的应用,如半导体制造、保护涂层和高温部件,CVD 是首选。
通过了解这些关键差异,采购人员和工程师可以根据材料兼容性、涂层厚度和操作条件等具体要求选择合适的沉积技术。
汇总表:
指标角度 | PVD | 气相沉积 |
---|---|---|
沉积机制 | 材料从固体源(视线)的物理转移。 | 气态前驱体与基底之间的化学反应。 |
工作温度 | 250°C 至 500°C(较低温度)。 | 450°C 至 1050°C(高温)。 |
涂层厚度 | 较薄(3~5μm),不够均匀。 | 较厚(10~20μm),更均匀。 |
材料兼容性 | 金属、合金、陶瓷(通用)。 | 陶瓷和聚合物(通用性有限)。 |
应力和表面 | 压应力,表面更光滑。 | 拉伸应力,涂层更致密,可能需要后处理。 |
应用 | 切削工具、装饰性表面、耐磨表面。 | 半导体制造、保护涂层、高温部件。 |
需要在 PVD 和 CVD 之间做出选择吗? 立即联系我们的专家 获取量身定制的建议!