烧结过程的持续时间因材料、技术和最终产品的具体要求不同而有很大差异。一般来说,烧结时间从几毫秒到 24 小时不等。烧结过程本身可能只需几秒钟,但成型后的烧结步骤可将总时间延长至数小时。温度、加热速率、压力、颗粒大小、成分和烧结气氛(如空气、真空或惰性气体)等因素在决定烧结时间方面起着至关重要的作用。高温烧结可以提高材料的性能,如拉伸强度和冲击能,但也需要对烧结环境进行精确控制。在许多应用中,烧结过程通常需要 15 到 20 个小时,具体取决于材料和最终零件所需的密度。
要点说明:
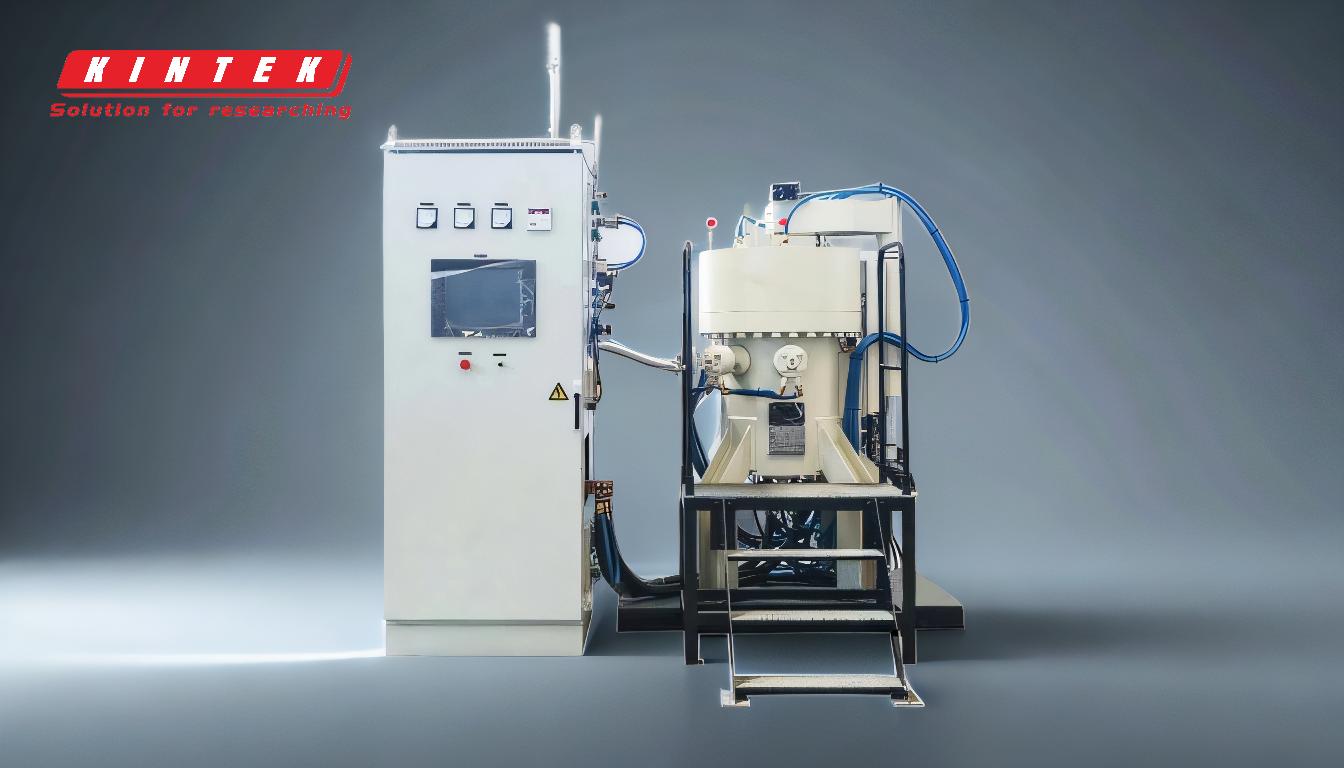
-
烧结时间范围:
- 烧结时间从几毫秒到 24 小时不等。
- 烧结过程本身可能只需要几秒钟,但成型后的烧结步骤可将总时间延长至数小时。
-
影响烧结时间的因素:
- 温度:决定烧结动力学和材料特性。较高的温度可以加快烧结过程,但必须小心控制,以避免材料降解。
- 加热速度:影响致密化。较快的加热速度可缩短烧结时间,但可能导致致密化不均匀。
- 压力:增强颗粒重排,消除气孔,从而缩短烧结时间。
- 颗粒尺寸和成分:较小的颗粒和均匀的成分可提高致密性,从而缩短烧结时间。
-
烧结气氛:
- 气氛(如空气、真空或氩气/氮气)会对烧结过程产生重大影响。惰性气氛通常用于防止氧化和其他不良反应,这些反应会影响烧结时间和最终材料性能。
-
材料和密度要求:
- 烧结炉的温度和时间取决于所使用的材料和最终部件的密度要求。不同的材料有不同的烧结要求,要达到更高的密度可能需要更长的烧结时间。
-
典型烧结持续时间:
- 在许多工业应用中,烧结过程通常需要 15 到 20 个小时。时间长短会因具体材料、所需性能和所用烧结炉类型(如带式输送机、推入式或间歇式烧结炉)的不同而变化。
-
成型后烧结:
- 虽然最初的烧结过程可能很快,但成型后的烧结步骤可能需要几个小时。这些步骤对于实现烧结零件的最终预期性能和尺寸至关重要。
-
对材料性能的影响:
- 高温烧结可以提高拉伸强度、弯曲疲劳强度和冲击能量。然而,要实现这些特性往往需要对烧结环境进行精确控制,并可能延长整个烧结时间。
总之,烧结时间变化很大,取决于多种因素,包括材料特性、预期结果和工艺条件。了解这些因素对于优化烧结工艺以高效实现所需的材料特性至关重要。
汇总表:
因素 | 对烧结时间的影响 |
---|---|
温度 | 温度越高,烧结速度越快,但需要精确控制,以避免材料降解。 |
加热速度 | 加热速度越快,时间越短,但可能导致密度不均匀。 |
压力 | 促进颗粒重新排列,缩短烧结时间。 |
颗粒大小 | 颗粒越小,致密化速度越快。 |
烧结气氛 | 惰性气体可防止氧化,从而影响时间和最终性能。 |
材料/密度 | 密度较大的材料或密度要求较高的材料会增加烧结时间。 |
典型持续时间 | 15-20 小时,适用于多种工业应用,取决于材料和炉型。 |
需要帮助优化烧结工艺? 立即联系我们的专家 获取量身定制的解决方案!