传递模塑是一种主要用于热固性塑料和橡胶的制造工艺,先将材料预热,然后在压力作用下将其压入加热的模腔。这种方法广泛应用于要求高精度和复杂形状的行业,如电子、汽车和航空航天。这种工艺有几个优点,如生产率高、表面光洁度好、能生产复杂的零件。然而,它也有缺点,包括初始模具成本较高、材料选择受限以及可能造成材料浪费。了解传递模塑的优缺点对于制造商就其在特定应用中的适用性做出明智决策至关重要。
要点说明:
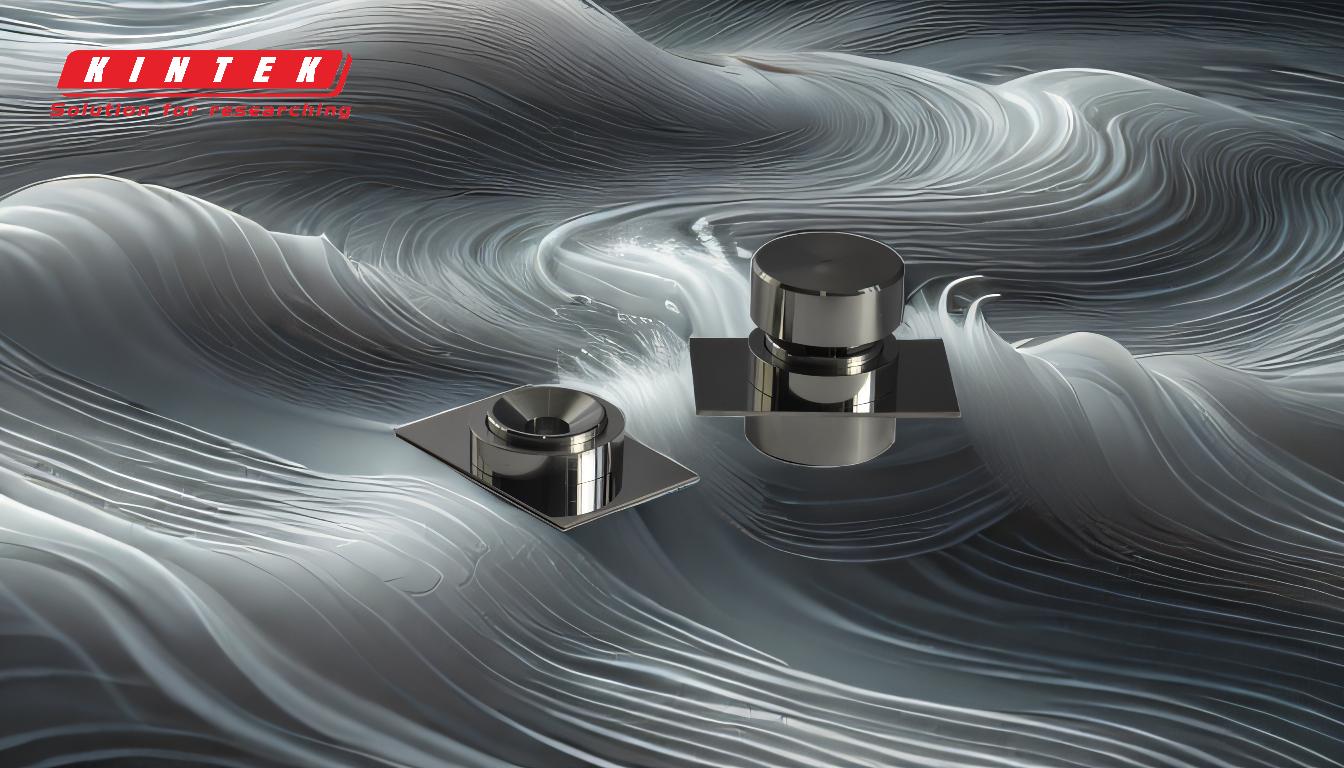
-
传递模塑的优势:
- 高生产率:传递模塑法生产周期短,适合大批量生产。预热后的材料迅速流入模具,与压缩成型等其他方法相比,可缩短生产周期。
- 出色的表面光洁度:该工艺生产的零件表面光滑、细节精细,非常适合要求美观或精度的应用,如电气连接器或汽车零部件。
- 生产复杂形状的能力:传递模塑能够制造出复杂的几何形状和薄壁零件,而使用其他模塑技术可能会遇到困难。
- 减少闪光:受控的压力和材料流动可最大限度地减少成型部件边缘的多余材料(飞边),从而降低后处理要求。
-
传递模塑的缺点:
- 初始模具成本高:传递模塑所使用的模具通常比压缩模塑所使用的模具昂贵,因为它们非常复杂,而且需要精确对齐。
- 材料限制:传递模塑主要适用于热固性材料,这些材料在固化后不能再熔化或重新成型。与注塑成型相比,这限制了可使用材料的范围。
- 材料浪费:加工过程会产生废料,尤其是浇口和流道,这些废料不一定能重复使用。
- 安装时间较长:与压缩成型等简单工艺相比,为传递成型准备模具和材料可能更耗时。
-
与其他成型技术的比较:
- 压缩成型:与压缩成型相比,传递成型能更好地控制材料流动和零件细节,但成本和复杂程度更高。
- 注塑成型:注塑成型在材料选择方面更为广泛,可处理较大的生产量,而传递模塑则更适合热固性材料和较小、复杂的零件。
-
传递模塑的应用:
- 电子产品:用于封装集成电路和连接器等电子元件,因其精度高且能保护易损件。
- 汽车:是生产垫片、密封件和其他需要高耐久性、耐热性和耐化学性的部件的理想选择。
- 航空航天:适用于制造具有复杂几何形状的轻质高强度零件。
-
选择传递模塑时应考虑的因素:
- 部件复杂性:传递模塑最适合设计复杂或壁薄的零件。
- 材料要求:确保材料与热固工艺兼容。
- 生产量:评估产量是否能证明较高的模具成本是合理的。
- 成本效益分析:权衡精度和表面光洁度的优势与材料浪费和安装时间的劣势。
总之,传递模塑是一种多功能、高效的制造工艺,在精度和表面光洁度方面具有明显优势。但是,其适用性取决于材料兼容性、零件复杂性和产量等因素。通过仔细评估这些方面,制造商可以确定传递模塑是否是满足其特定需求的正确选择。
汇总表:
方面 | 优点 | 缺点 |
---|---|---|
生产率 | 生产率高,适合大批量生产。 | 与简单工艺相比,设置时间较长。 |
表面光洁度 | 出色的表面光洁度,光滑的表面和精细的细节。 | 以浇口和流道形式浪费材料。 |
复杂形状 | 能够制造复杂几何形状和薄壁零件。 | 由于模具复杂,初始模具成本较高。 |
材料兼容性 | 热固性材料的理想选择。 | 仅限于热固性材料,限制了材料的选择。 |
想知道传递模塑是否适合您的项目? 今天就联系我们的专家 进行咨询!