粉末冶金术中的烧结是一种极具优势的制造工艺,具有众多优点,包括能够生产出高精度的复杂形状、改善材料性能、成本效益和环境可持续性。这种工艺是将金属粉末压制成所需形状,然后加热至熔点以下,将颗粒粘合在一起。其结果是生产出坚固、耐用和精确的部件,并可根据特定应用进行定制。其主要优势包括:可加工高熔点金属、减少孔隙、提高机械和热性能,以及在制造过程中实现高重复性。
要点说明:
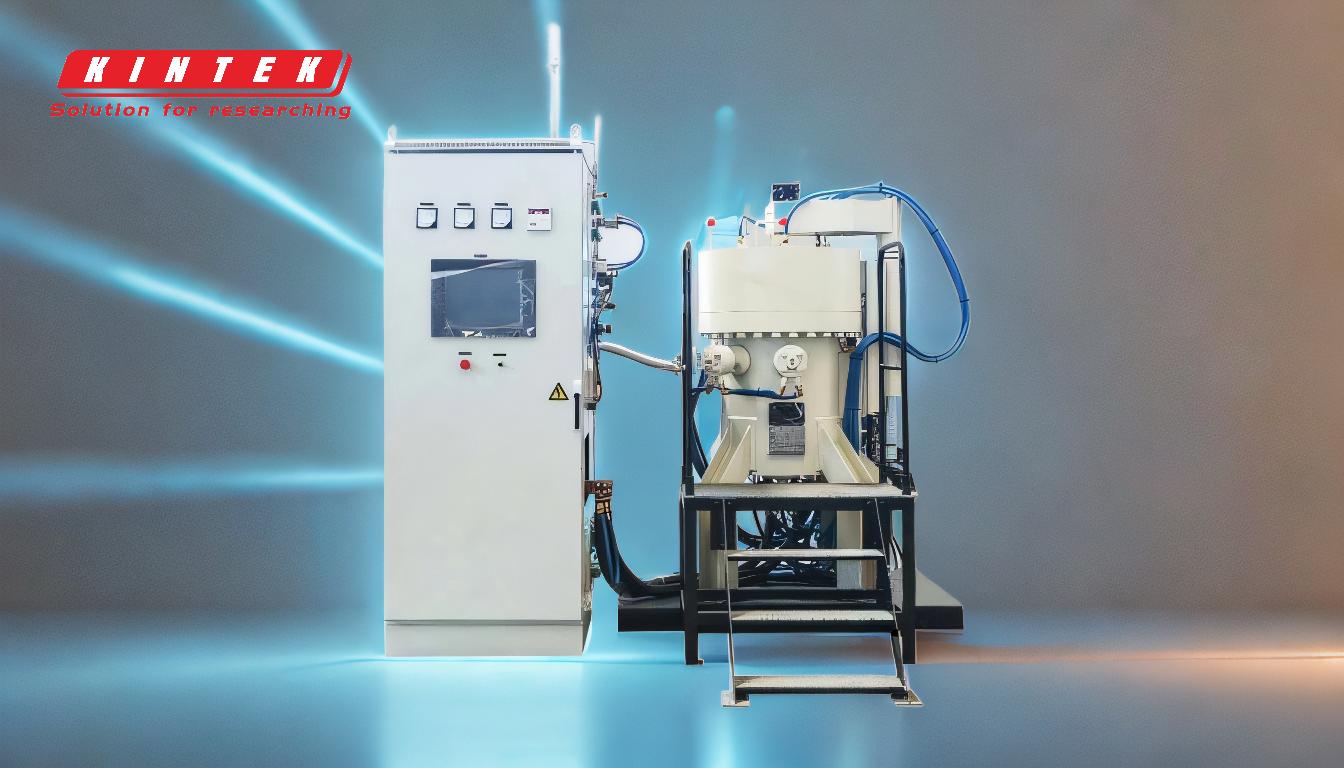
-
以高精度生产复杂形状的产品
- 烧结技术可以制造出复杂的外部和内部几何形状,而传统制造方法很难或根本无法实现这些形状。
- 使用线切割放电加工(EDM)制造的模具和冲模可以实现厘米级公差(0.01 毫米)。
- 例如,在汽车、航空航天和医疗设备等行业中,具有内部通道、凹槽或复杂表面纹理的部件至关重要。
-
改善材料性能
- 烧结可减少最终产品的孔隙率,提高强度、耐久性、导电性和导热性等性能。
- 该工艺在颗粒之间形成烧结颈,这些烧结颈粘合在一起,形成一个空隙极小的固体结构。
- 这对于轴承、齿轮和结构部件等需要高机械性能的应用尤其有用。
-
定制材料成分
- 烧结可在金属粉末混合物中加入镍、铜和石墨等合金元素,从而实现定制的材料特性。
- 这种灵活性对于满足客户的特殊要求非常重要,例如增强耐磨性、提高导热性或控制过滤器和催化剂的孔隙率。
-
成本效益
- 烧结是一种接近净成形的制造工艺,这意味着最终产品只需极少的机加工或精加工,从而减少了材料浪费和生产成本。
- 此外,与熔化金属相比,烧结能耗更低,是一种既环保又经济的选择。
-
材料选择的多样性
- 烧结技术尤其适用于熔点高、组成元素熔点差异大、可铸性差的材料。
- 例如,钨、钼和陶瓷,这些材料都很难用传统方法进行加工。
-
高重复性和一致性
- 烧结工艺具有很高的可重复性,可确保大批量生产的质量始终如一。
- 这种可靠性对于电子和医疗设备等对精度和均匀性要求极高的行业至关重要。
-
环境和能源效率
- 与熔化相比,烧结的操作温度更低,从而减少了能源消耗和温室气体排放。
- 压制粉末时不使用润滑剂,减少了表面氧含量,这些都进一步促进了烧结技术的环保特性。
-
跨行业应用
- 烧结技术可用于制造各种产品,包括轴承、珠宝、热管、霰弹枪外壳和过滤器。
- 它能够生产具有特定孔隙度的部件,因此非常适合催化剂和过滤系统等应用。
利用这些优势,粉末冶金中的烧结技术为众多行业和应用提供了多功能、高效和可持续的制造解决方案。
汇总表:
优势 | 描述 |
---|---|
高精度的复杂形状 | 以厘米级公差(0.01 毫米)实现复杂几何形状。 |
改善材料性能 | 减少孔隙率,提高强度、耐用性和导电性。 |
量身定制的材料成分 | 利用镍、铜和石墨等合金元素定制特性。 |
成本效益 | 近净成形工艺可减少材料浪费和能源消耗。 |
材料选择的多样性 | 是高熔点金属和陶瓷等高难度材料的理想之选。 |
高重复性和一致性 | 确保大批量生产的统一质量。 |
环保节能 | 更低的温度和更少的排放使其更加环保。 |
跨行业应用 | 用于汽车、航空航天、医疗设备等。 |
准备好探索烧结技术如何改变您的制造工艺了吗? 今天就联系我们 了解更多信息!