无芯感应炉具有温度控制精确、热量分布均匀、合金更换灵活等优点,但也有明显的缺点。主要缺点包括与效率高达 98% 的有芯炉相比,功率效率较低(约 75%)。此外,频繁更换合金会加速耐火衬的磨损,缩短其使用寿命。无芯炉中没有焊剂集中芯,这进一步降低了其效率。这些因素使得无芯感应炉不太适合高产量操作或要求连续生产且停机时间最短的环境。
要点说明:
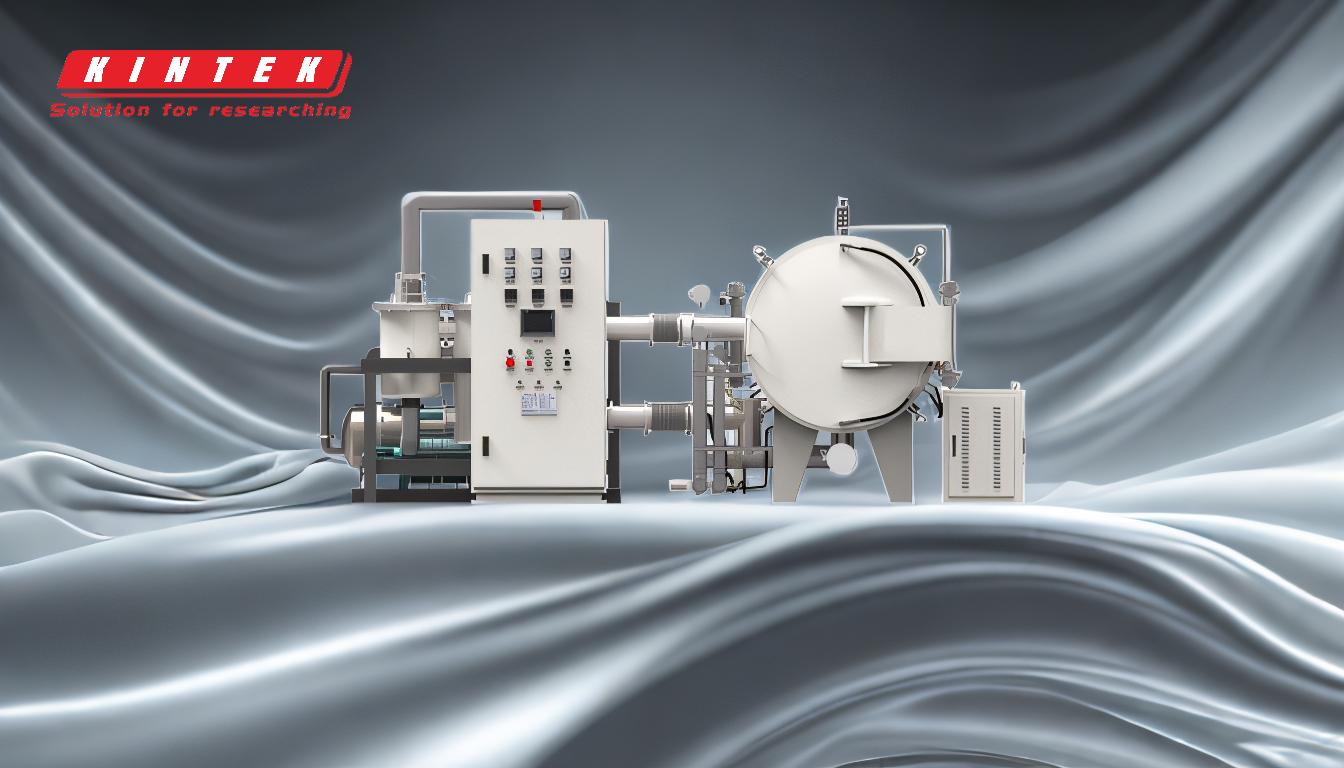
-
功率效率降低
- 无芯感应炉的功率效率约为 75%,明显低于磁芯式感应炉,后者的效率可达 98%。
- 由于无芯炉中没有磁通量集中的铁芯,磁场无法有效集中在金属炉料上,从而导致能量损失。
- 这种较低的效率会导致较高的能源消耗和运营成本,因此无芯炉对于高产量或能源密集型应用来说不太经济。
-
耐火衬磨损
- 频繁更换合金是无芯炉的常见做法,这会加速耐火衬的降解。
- 耐火衬暴露在热循环和与不同合金的化学反应中,导致裂纹、侵蚀和寿命缩短。
- 更换耐火衬既费钱又费时,增加了维护费用和停机时间。
-
对连续操作的适用性有限
- 无芯感应炉的设计具有灵活性,可以在冷态下关闭和启动,这对合金更换非常有利。
- 然而,这种设计使其不太适合连续、高产的操作,因为在这种操作中,保持恒定的熔融金属池是至关重要的。
- 相比之下,铁芯式窑炉由于效率更高且能够连续运行,因此更适合此类应用。
-
能耗较高
- 无芯炉的效率较低,这意味着需要更多的能源才能达到与有芯炉相同的熔化效果。
- 能源需求的增加会导致运营成本上升,尤其是在电费昂贵的地区。
- 对于旨在尽量减少能源开支的企业来说,无芯炉可能不是最具成本效益的选择。
-
冷却系统依赖性
- 无芯感应电炉依靠水冷铜线圈来防止运行时过热。
- 冷却系统增加了窑炉设计的复杂性,需要定期维护以确保正常运行。
- 冷却系统的任何故障都可能导致线圈损坏或窑炉停产,从而影响生产。
-
操作限制
- 虽然无芯炉在合金变化和频率范围(50 赫兹至 10 千赫兹)方面具有灵活性,但在较低频率下效率较低。
- 有芯型窑炉的效率更高,更适合需要在宽频率范围内保持稳定性能的应用。
总之,虽然无芯感应炉能很好地控制温度和金属化学性质,但其功率效率较低、易受耐火衬磨损以及能耗较高,因此不太适合高产量或连续操作。在为特定工业应用选择窑炉时,应仔细考虑这些缺点。
汇总表:
缺点 | 说明 |
---|---|
降低能效 | 运行效率约为 75%,而芯式炉为 98%,因此能耗更高。 |
耐火衬磨损 | 频繁更换合金会加速衬里退化,增加维护成本和停机时间。 |
连续使用受限 | 由于设计限制,不太适合高吞吐量或连续运行。 |
能耗较高 | 效率降低会增加运营成本,尤其是在电费昂贵的地区。 |
冷却系统依赖性 | 依赖水冷线圈,增加了复杂性和维护需求。 |
运行限制 | 在频率较低时效率较低,因此芯式炉更适合实现稳定的性能。 |
需要帮助选择适合您的炉子吗? 立即联系我们的专家 !