射频磁控溅射虽然具有在非导电材料上沉积薄膜的能力和高沉积率的优点,但也有一些明显的缺点。这些缺点包括有效镀膜面积有限、薄膜基底的粘合强度差,以及会形成多孔、粗糙的柱状结构。此外,由于强烈的离子轰击,该工艺还可能导致基底升温和结构缺陷增加。由于涉及众多控制参数,针对特定应用优化薄膜特性也会耗费大量时间。尽管这种技术用途广泛,但在选择这种薄膜沉积技术时必须仔细考虑这些缺点。
要点说明:
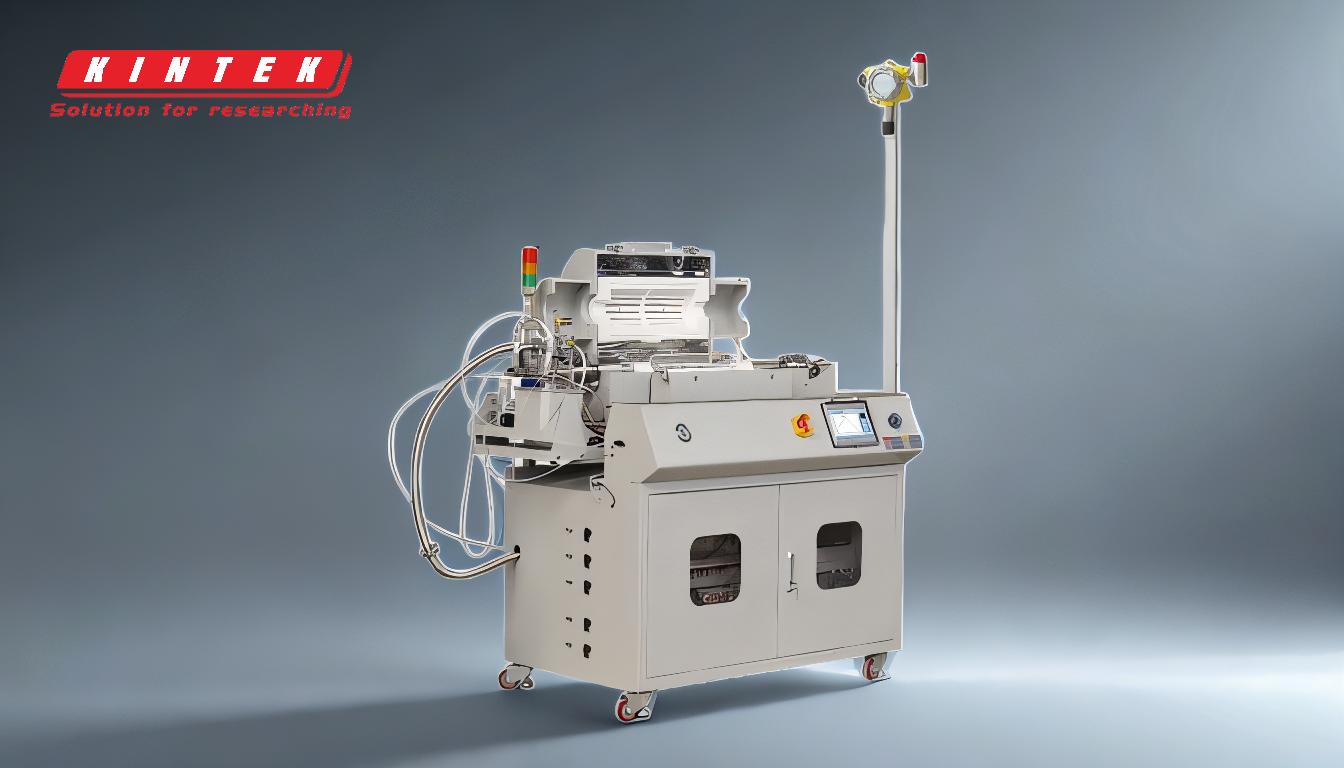
-
有限的有效涂层面积:
- 射频磁控溅射的有效镀层面积较小,这限制了可镀工件的几何尺寸。等离子体浓度在距离目标表面 60 毫米以外迅速降低,从而限制了工件的放置位置。对于较大或较复杂的基底,这种限制可能会造成问题,因为均匀镀膜变得具有挑战性。
-
目标粒子能量低:
- 射频磁控溅射中飞行靶粒子的能量相对较低。这导致薄膜与基材之间的结合强度较差,从而影响涂层材料的耐用性和性能。低能量颗粒还容易形成多孔和粗糙的柱状结构,这对于需要光滑致密薄膜的应用来说可能并不理想。
-
高基底加热:
- 射频磁控溅射的一个明显缺点是基片加热温度较高,最高可达 250°C。这种高温对热敏材料不利,限制了可有效镀膜的基底范围。此外,高温还会导致某些材料产生热应力和变形。
-
结构缺陷增加:
- 在射频磁控溅射过程中,基片上强烈的离子轰击会导致沉积薄膜的结构缺陷增加。这些缺陷会对薄膜的机械、电气和光学性能产生负面影响,使其不太适合高性能应用。
-
复杂的优化过程:
- 在射频磁控溅射中,针对特定应用优化薄膜特性是一个复杂而耗时的过程。该技术涉及许多控制参数,如功率、压力和气体成分,需要仔细调整才能达到所需的薄膜特性。这种复杂性会增加与工艺开发相关的时间和成本。
-
材料限制:
- 虽然射频磁控溅射在非导电材料上沉积薄膜方面具有优势,但在可有效镀膜的材料类型方面仍有局限性。有些材料可能无法承受工艺中的高温或强烈离子轰击,从而限制了它们在某些应用中的适用性。
-
多孔和粗糙薄膜的形成:
- 由于溅射粒子的能量较低,通常会在沉积薄膜中形成多孔和粗糙的柱状结构。与致密光滑的薄膜相比,这些结构可能具有较差的机械和光学性能,这对于需要高质量涂层的应用来说可能是一个重大的不利因素。
总之,虽然射频磁控溅射具有一些优点,如沉积速率高和能够为非导电材料镀膜,但它也有一些必须考虑的缺点。这些缺点包括镀膜面积有限、结合强度差、基材发热高、结构缺陷增加、优化过程复杂、材料限制以及会形成多孔和粗糙的薄膜。在为特定薄膜沉积应用选择射频磁控溅射时,应仔细评估这些因素。
总表:
缺点 | 描述 |
---|---|
有效涂层面积有限 | 等离子浓度超过 60 毫米就会降低,从而限制了涂层的均匀性。 |
目标粒子能量低 | 薄膜的粘合强度差、多孔、柱状结构粗糙。 |
基底温度过高 | 高达 250°C 的温度会损坏热敏材料。 |
结构缺陷增加 | 强烈的离子轰击会导致机械和光学性能缺陷。 |
复杂的优化过程 | 需要对功率、压力和气体成分进行耗时的调整。 |
材料限制 | 某些材料无法承受高温或离子轰击。 |
形成多孔、粗糙的薄膜 | 薄膜通常具有较差的机械和光学特性。 |
需要帮助选择正确的薄膜沉积技术吗? 立即联系我们的专家 获取个性化指导!