物理气相沉积 (PVD) 和化学气相沉积 (CVD) 是两种广泛使用的在基材上沉积薄膜和涂层的技术。虽然这两种方法都旨在创造高质量的涂层,但它们在机制、材料和应用方面存在显着差异。 PVD 依靠蒸发或溅射等物理过程将固体材料沉积到基材上,而 CVD 涉及气态前体和基材之间的化学反应以形成固体涂层。 PVD 和 CVD 之间的选择取决于所需的涂层性能、基材兼容性和加工条件等因素。
要点解释:
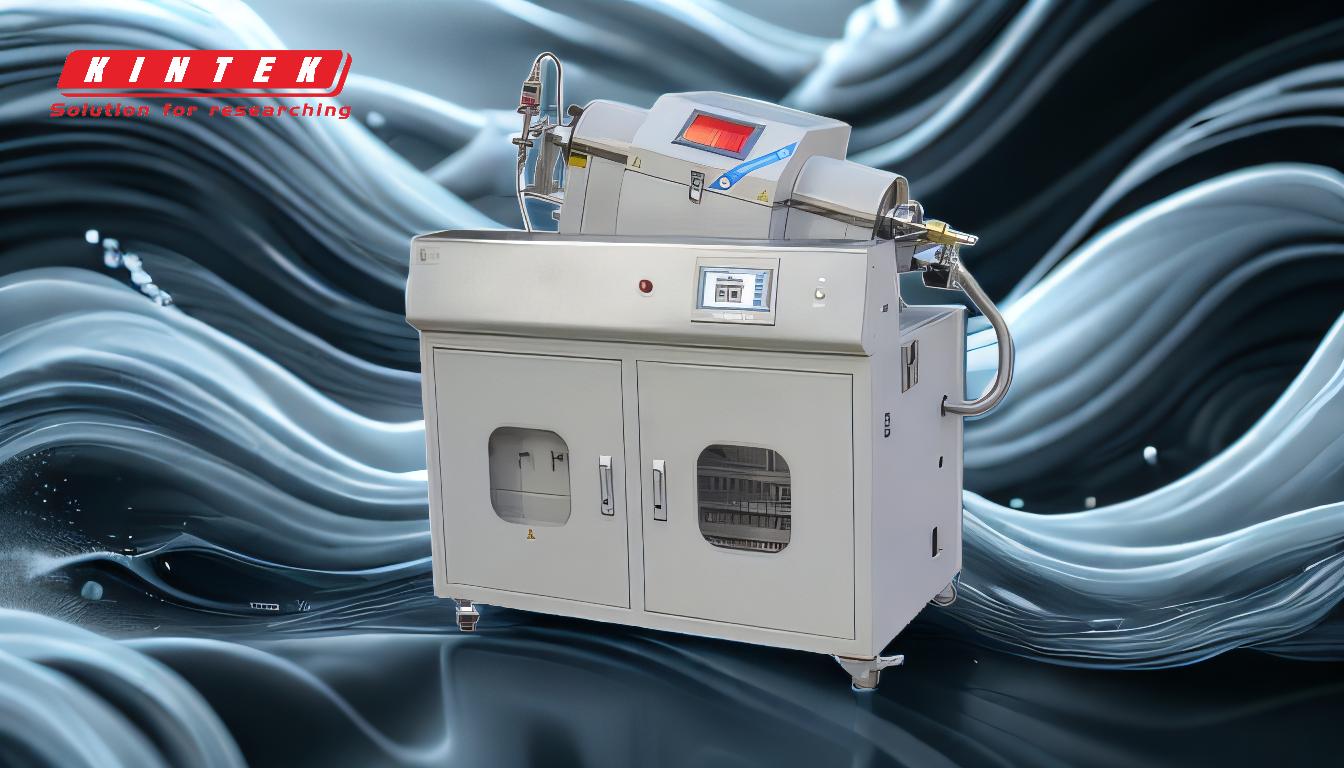
-
沉积机制:
- 物理气相沉积 :PVD 是一种物理过程,其中固体材料被汽化(通过蒸发、溅射或升华),然后沉积到基材上。该过程是视线式的,这意味着材料直接从源传输到基材。
- CVD :CVD 是一种化学工艺,气态前体在加热的基材上发生反应或分解,形成固体涂层。该过程是多向的,即使在复杂的几何形状上也能实现均匀的覆盖。
-
材料来源:
- 物理气相沉积 :使用汽化的固体材料(目标)来形成涂层。常见的技术包括溅射和蒸发。
- CVD :使用气态前体在基材表面发生化学反应形成涂层。气态前体通常是含有所需涂层材料的挥发性化合物。
-
温度要求:
- 物理气相沉积 :与 CVD 相比,通常在较低的温度下运行。这使得 PVD 适用于温度敏感基材。
- CVD :需要高温 (500°C–1100°C) 以促进沉积所需的化学反应。这限制了它在不能承受高温的基材上的使用。
-
沉积率:
- 物理气相沉积 :与 CVD 相比,通常具有较低的沉积速率。然而,电子束 PVD (EBPVD) 等技术可以在相对较低的基板温度下实现高沉积速率(0.1 至 100 μm/min)。
- CVD :由于涉及化学反应,可提供更高的沉积速率,但这可能会因具体的 CVD 工艺和所使用的材料而异。
-
涂层性能:
- 物理气相沉积 :产生具有优异附着力的致密、高纯度涂层。 PVD 的视线特性可能会导致复杂形状的覆盖不均匀。
- CVD :提供具有优异保形性的均匀涂层,非常适合涂覆复杂的几何形状。然而,由于涉及化学反应,CVD 涂层可能含有杂质。
-
应用领域:
- 物理气相沉积 :常用于装饰涂料、耐磨涂料、光学薄膜。它还用于半导体制造中沉积薄膜。
- CVD :广泛应用于半导体行业,用于沉积介电层、导电层和保护涂层。它还用于制造硬质涂层,例如类金刚石碳 (DLC) 薄膜。
-
环境和安全考虑:
- 物理气相沉积 :通常被认为更安全、更环保,因为它不涉及危险的化学反应或腐蚀性副产品。
- CVD :会产生腐蚀性或有毒副产品,需要小心处理和处置。高温也带来安全隐患。
-
材料利用效率:
- 物理气相沉积 :由于工艺的视线性质,通常材料利用率较低。然而,EBPVD 等技术的材料利用率很高。
- CVD :气态前驱体可以充分反应并沉积在基材上,因此材料利用效率高。
总之,PVD 和 CVD 在机理、材料和应用方面都有所不同。 PVD 非常适合温度敏感基材和需要高纯度涂层的应用,而 CVD 则擅长涂覆复杂的几何形状并实现高沉积速率。两者之间的选择取决于应用的具体要求,包括基材兼容性、所需的涂层性能和加工条件。
汇总表:
方面 | 物理气相沉积 | CVD |
---|---|---|
机制 | 物理过程(蒸发、溅射) | 化学过程(气态反应) |
材料来源 | 固体材料(靶材) | 气态前体 |
温度 | 较低的温度(适用于敏感基材) | 高温(500°C–1100°C) |
沉积率 | 一般较低(EBPVD 除外) | 更高的沉积速率 |
涂层性能 | 致密、高纯度、附着力优异 | 均匀、保形性极佳,可能含有杂质 |
应用领域 | 装饰、耐磨、光学薄膜、半导体 | 半导体、介电层、硬涂层(例如 DLC) |
环境影响 | 更安全、更少的危险副产品 | 可能产生有毒/腐蚀性副产品 |
材料效率 | 较低(视线),EBPVD 除外 | 高(气态前体完全反应) |
需要帮助选择正确的沉积技术吗? 立即联系我们的专家 获取量身定制的建议!