溅射和电子束(e-beam)蒸发都是用于制造薄膜的物理气相沉积(PVD)技术,但它们在机理、操作条件和所产生的薄膜特性上有很大不同。溅射是利用通电等离子体原子将原子从目标材料中分离出来,然后沉积到基底上。它的工作温度较低,对复杂基底的附着力和覆盖率较好,生产的薄膜晶粒较小。另一方面,电子束蒸发法使用聚焦电子束蒸发高温材料,沉积率较高,但均匀性和附着力较差。这些差异使得每种方法都适合特定的应用,具体取决于所需的薄膜特性。
要点说明:
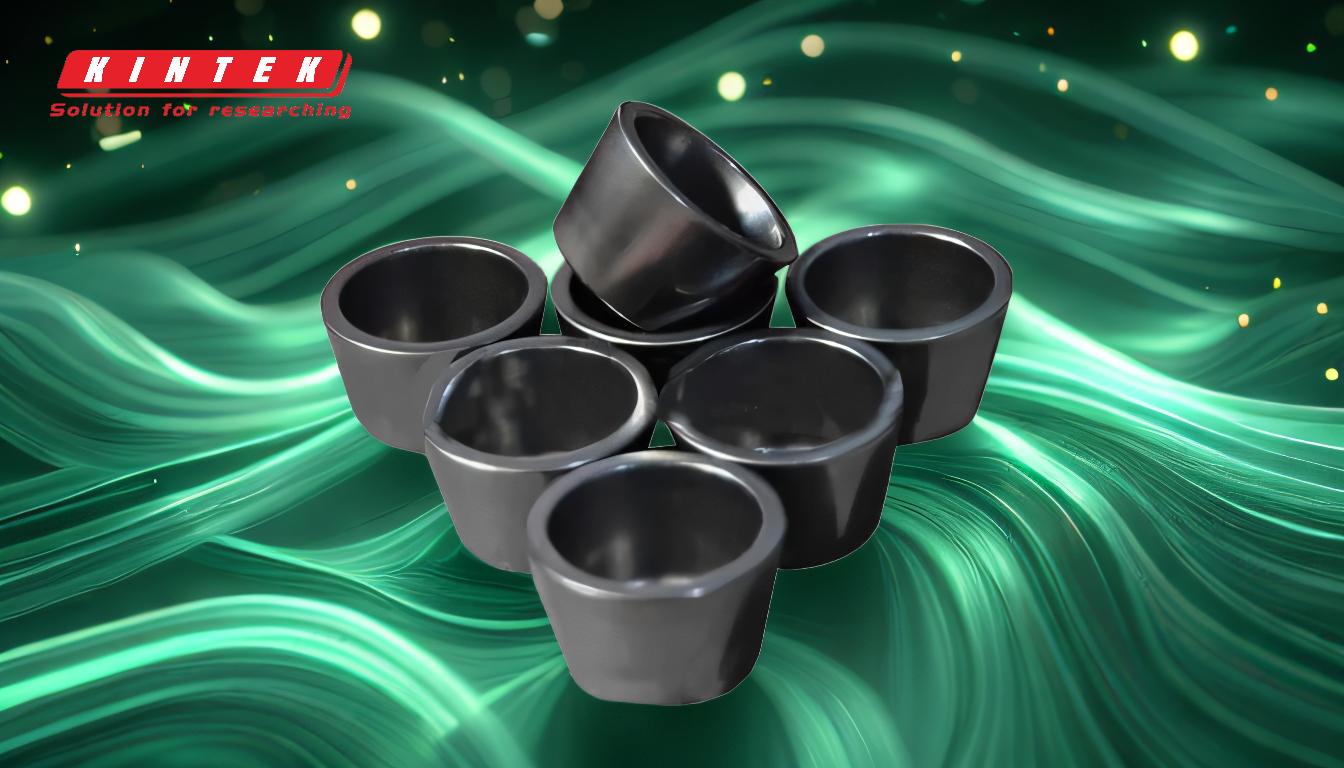
-
沉积机制:
- 溅射:用高能等离子体原子(通常是氩离子)轰击目标材料,使原子脱落,然后沉积到基底上。这种工艺不依赖蒸发,而且温度较低。
- 电子束蒸发:使用聚焦电子束加热和汽化目标材料,使其蒸发并沉积到基底上。这是一种热蒸发过程,需要较高的温度。
-
真空要求:
- 溅射:与电子束蒸发相比,其真空度相对较低。
- 电子束蒸发:需要高真空环境,以尽量减少污染并确保高效汽化。
-
沉积速率:
- 溅射:通常沉积率较低,尤其是电介质材料,但纯金属的沉积率可能较高。
- 电子束蒸发:具有更高的沉积率,在许多应用中都能更快地发挥作用。
-
附着力和覆盖率:
- 溅射:附着力更强,覆盖更均匀,尤其适用于复杂或三维基材。
- 电子束蒸发:附着力较低,覆盖不均匀,尤其是在复杂的表面上。
-
薄膜特性:
- 溅射:产生的薄膜晶粒更小、更均匀、沉积物能量更高,从而使薄膜更致密、更耐用。
- 电子束蒸发:导致薄膜晶粒尺寸增大,均匀度降低,从而影响薄膜的机械和光学特性。
-
吸收气体和纯度:
- 溅射:通常会吸收较多的气体,从而影响薄膜的纯度。不过,只要控制得当,也能生产出高纯度的薄膜。
- 电子束蒸发:吸收更少的气体,有助于在最佳条件下获得更高纯度的薄膜。
-
可扩展性和自动化:
- 溅射:可扩展性强,易于实现大规模自动化生产。
- 电子束蒸发:虽然沉积率很高,但与溅射法相比,其可扩展性较差,自动化难度较大。
-
应用领域:
- 溅射:非常适合需要在复杂几何形状上进行高质量均匀镀膜的应用,如半导体、光学镀膜和装饰性表面处理。
- 电子束蒸发:适用于需要高沉积速率和高纯度薄膜的应用,如微电子和太阳能电池的金属化。
通过了解这些差异,设备和耗材购买者可以在平衡沉积速率、薄膜质量和可扩展性等因素的基础上,就哪种 PVD 方法最适合其特定应用需求做出明智的决定。
汇总表:
特征 | 溅射 | 电子束蒸发 |
---|---|---|
机制 | 用高能等离子体原子轰击目标 | 使用电子束汽化目标材料 |
温度 | 较低温度 | 较高温度 |
沉积速率 | 电介质较低,金属较高 | 较高 |
附着力和覆盖率 | 附着力更强,覆盖范围更均匀,适用于复杂基材 | 附着力较低,覆盖不均匀 |
薄膜特性 | 晶粒较小,均匀性较高,薄膜较致密 | 晶粒较大,均匀度较低 |
纯度 | 吸收气体较多,但可实现高纯度 | 吸收气体少,纯度更高 |
可扩展性 | 可扩展性高,易于自动化 | 可扩展性低,难以自动化 |
应用领域 | 半导体、光学镀膜、装饰性表面处理 | 金属化、微电子、太阳能电池 |
需要帮助在溅射和电子束蒸发之间做出选择? 立即联系我们的专家 找到满足您需求的最佳 PVD 解决方案!