物理气相沉积(PVD)和化学气相沉积(CVD)是先进的涂层技术,用于增强材料的表面特性,如硬度、耐磨性和耐腐蚀性。PVD 是在真空中蒸发固体材料并将其沉积到基材上,而 CVD 则是利用气态前驱体的化学反应形成涂层。两种工艺都有不同的步骤、优势和应用。PVD 速度更快,操作温度更低,适用于更广泛的材料,而 CVD 可产生更致密、更均匀的涂层,但需要更高的温度和更长的加工时间。
要点说明:
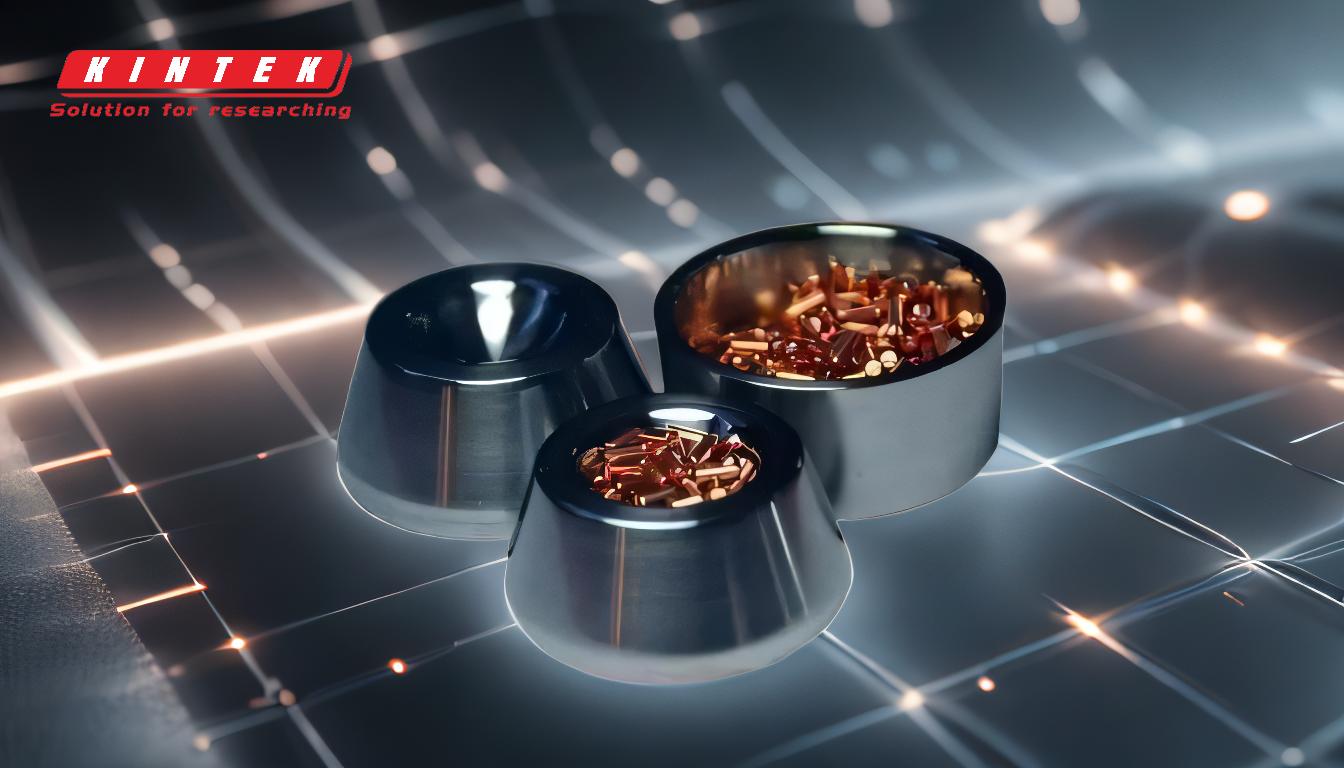
-
PVD 和 CVD 涂层工艺概述:
- PVD:包括在真空中蒸发固体材料并将其沉积到基底上。这是一种物理过程,工作温度较低(约 500 °C),适用于金属、合金和陶瓷。
- 化学气相沉积:利用气态前驱体在高温(800~1000 °C)下的化学反应沉积涂层。它通常仅限于陶瓷和聚合物,可产生更厚、更致密、更均匀的涂层。
-
PVD 涂层工艺的步骤:
- 步骤 1:清洁基底:清洁基材,去除污染物,确保涂层更好地附着。
- 步骤 2:预处理:对基材进行预处理,以提高涂层附着力,通常包括表面活化或蚀刻。
- 步骤 3:涂层:使用电子束、离子轰击或阴极电弧等技术蒸发目标材料。汽化后的材料被输送到基底,沉积成薄膜。
- 步骤 4:质量控制:检查涂层基材,确保涂层符合规定的标准,如厚度、均匀性和附着力。
- 步骤 5:涂饰:为提高涂层的外观或性能,还可进行其他处理,如抛光或退火。
-
CVD 涂层工艺步骤:
- 步骤 1:前体介绍:将气态前驱体引入反应室。
- 步骤 2:化学反应:前驱体在高温(800~1000 °C)下发生反应,形成所需的涂层材料。
- 步骤 3:沉积:反应产物沉积在基底上,形成致密均匀的涂层。
- 步骤 4:后处理:涂层基材可能会经过退火或表面抛光等额外处理,以改善其性能。
-
PVD 和 CVD 的主要区别:
- 温度:PVD 的工作温度较低(约 500 °C),而 CVD 需要较高的温度(800~1000 °C)。
- 涂层厚度:PVD 产生的涂层较薄(3~5μm),而 CVD 产生的涂层较厚(10~20μm)。
- 涂层密度和均匀性:与 PVD 涂层相比,CVD 涂层更致密、更均匀。
- 材料兼容性:PVD 可以沉积更广泛的材料,包括金属、合金和陶瓷,而 CVD 通常仅限于陶瓷和聚合物。
- 加工时间:PVD 速度更快,适合需要快速周转时间的应用,而 CVD 由于涉及化学反应,需要更长的时间。
-
PVD 和 CVD 的应用:
- PVD:常用于要求高耐磨性的应用领域,如切削工具、装饰涂层和航空航天部件。它还适用于铣削等断续切割工艺。
- CVD:适用于要求涂层厚、致密、均匀的应用,如半导体制造、车削等连续切削工艺的耐磨涂层以及高温应用。
-
优点和局限性:
- PVD 优势:加工速度更快、工作温度更低、与多种材料兼容。
- PVD 的局限性:与 CVD 相比,涂层的密度和均匀度较低。
- CVD 的优势:涂层更致密、更均匀,适合高温应用。
- CVD 的局限性:加工温度更高、加工时间更长、材料兼容性有限。
通过了解 PVD 和 CVD 涂层工艺的详细步骤和差异,设备和耗材采购人员可以根据其应用的具体要求(如所需涂层性能、材料兼容性和加工限制)做出明智的决定。
汇总表:
指标角度 | PVD | 气相沉积 |
---|---|---|
温度 | 较低(约 500 °C) | 较高(800~1000 °C) |
涂层厚度 | 较薄 (3~5μm) | 较厚(10~20μm) |
涂层密度 | 密度较低 | 密度更大、更均匀 |
材料兼容性 | 金属、合金、陶瓷 | 陶瓷、聚合物 |
加工时间 | 更快 | 更长 |
应用领域 | 切削工具、装饰涂层、航空航天部件 | 半导体制造、耐磨涂层、高温应用 |
需要帮助为您的应用选择正确的涂层工艺吗? 立即联系我们的专家 !