CVD 技术简介
定义和重要性
化学气相沉积(CVD)是一种关键的薄膜沉积技术,在半导体制造和其他众多行业中发挥着至关重要的作用。该技术可在各种基底上精确、可控地沉积薄膜,对于制造电子元件、光学涂层和保护层至关重要。
在半导体制造领域,CVD 是制造高质量、均匀薄膜不可或缺的技术,可提高集成电路的性能和可靠性。CVD 能够沉积具有特定性能(如导电性、绝缘性和光学透明度)的材料,因此成为生产先进微电子器件的重要工具。
除半导体外,CVD 还广泛应用于显示技术,用于沉积氧化铟锡 (ITO) 薄膜和铜膜,从而增强显示设备的功能性和耐用性。此外,CVD 还可用于生产透镜和反射镜的光学镀膜,以及金属表面的防腐蚀镀膜,显示了其在不同领域的多功能性。
CVD 的重要意义不仅在于其广泛的应用,还在于它能够生产出具有优异均匀性、附着力和可控性的薄膜。这些特性使 CVD 成为推动各行各业发展和材料科学创新不可或缺的技术。
CVD 的工作原理
化学反应过程
在化学气相沉积(CVD)过程中,薄膜的形成依赖于可控的化学反应。首先,将作为所需薄膜原材料的气体前驱体引入反应室。这些前驱体通常是容易气化的挥发性化合物。一旦进入反应室,这些气体就会受到加热,加热温度通常在几百摄氏度到几千摄氏度之间,具体取决于特定的前驱体和所需的薄膜特性。
加热过程至关重要,因为它提供了气体分子克服活化能障碍所需的能量,使它们能够发生反应。随着温度的升高,气体前驱体分解并相互反应或与基底表面反应。这种反应通常发生在基底表面,前驱体吸附在基底表面,然后进一步分解或结合。这些反应产生的产物包括沉积在基底上的所需薄膜材料和副产物,副产物通常为气态,并从系统中排出。
例如,在硅薄膜的沉积过程中,常见的前驱体是硅烷(SiH4)。加热时,硅烷分解成硅和氢气。硅原子随后沉积到基底上,形成连续的薄膜,而氢气则从反应室中排出。这个例子说明了 CVD 工艺的动态特性,要达到理想的薄膜质量和均匀性,必须精确控制温度和前驱体流速。
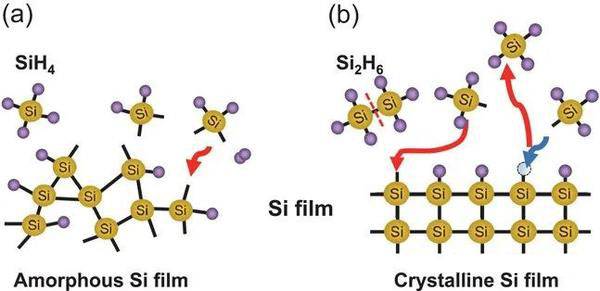
CVD 中的化学反应过程不仅限于简单的分解,还可能涉及氧化、氮化或形成复合材料等复杂反应。这些反应通常会因为额外反应气体(如氧气或氮气)的存在而得到促进,这些气体被引入腔室以改变薄膜的特性。例如,在沉积二氧化硅 (SiO2) 薄膜时,硅烷会与氧气反应形成氧化层。
反应实例
在化学气相沉积(CVD)过程中,主要反应之一是三氯硅烷(SiHCl₃)的分解。这一过程是形成薄膜的基础,尤其是在半导体制造中。当硅氢₃被加热时,会发生复杂的化学变化。硅源材料 SiHCl₃ 分解成元素硅,然后沉积到基底上。同时,副产品氯(Cl₂)和盐酸(HCl)气体被释放出来。这些气体通常从反应室排出,以确保它们不会干扰沉积过程。
该反应体现了 CVD 的核心原理,即通过受控化学反应将前驱气体转化为固体薄膜。SiHCl₃ 的分解不仅为薄膜的形成提供了所需的硅,而且还说明了气体管理在维持清洁高效的沉积环境方面的重要性。副产气体 Cl₂ 和 HCl 是监测和控制的关键,因为它们的存在会影响沉积薄膜的质量和均匀性。
CVD 的分类
热化学气相沉积
热化学气相沉积(CVD)是指在反应室中将前驱气体加热到高温(通常高于 700°C)。这种高温对促进前驱体气体的分解至关重要,前驱体气体分解后沉积到基底上形成薄膜。该工艺依靠热能推动薄膜形成所需的化学反应,确保沉积的薄膜具有更强的性能,如更高的结晶度、更高的密度和更快的沉积速率。
在热化学气相沉积过程中,气态反应物通常由氮气等惰性气体带入反应室,这有助于保持受控环境。高温不仅能促进前驱体的分解,还能实现在较低温度下无法实现的反应。不过,高温也会导致一些缺点,如薄膜内应力的形成、基底元素向薄膜内扩散的速度加快以及基底本身的潜在降解。
优点 | 缺点 |
---|---|
提高沉积速度 | 应力形成 |
提高结晶度 | 更高的扩散率 |
薄膜密度更大 | 基底降解 |
热化学气相沉积技术在半导体制造领域尤其具有优势,可用于在硅晶片上沉积二氧化硅、氮化硅和多晶硅等薄膜。这些薄膜对于集成电路和其他电子设备的制造至关重要。尽管热化学气相沉积具有很多优点,但它需要对温度和前驱体输送率进行精心管理,以优化沉积过程并减少潜在的缺点。
等离子体增强化学气相沉积(PECVD)
等离子体增强化学气相沉积(PECVD)是化学气相沉积(CVD)的一种特殊变体,它利用等离子体来提高反应速率,并对沉积过程进行细致的控制。传统的化学气相沉积法完全依靠热能分解前驱气体,而 PECVD 则不同,它利用等离子体激活反应气体,从而在更低的温度(通常在 100 到 600 °C 之间)下促进沉积。
在 PECVD 中,等离子体充当催化剂,将活性前驱体分解为其组成原子或分子,然后在基底表面发生反应并沉积。这种等离子体辅助分解可在低至 200-350 °C 的温度下沉积各种薄膜,包括硅 (Si)、二氧化硅 (SiO2)、氮化硅、氧氮化硅和碳化硅。这种较低的温度范围对于涉及铝等对温度敏感的材料的应用尤其有利,因为较高的温度可能会损害基底的完整性。
PECVD 工艺通常在平行板电容耦合等离子体系统中进行。在这种装置中,基片位于接地电极上,而等离子体则在两个电极之间产生。PECVD 中使用的气体可根据所需的薄膜特性而有所不同,常见的气体包括硅烷 (SiH4)、氧化亚氮 (N2O)、氨 (NH3)、氦 (He)、氩 (Ar)、三氟化氮 (NF3) 和磷化氢 (PH3)。每种气体在沉积过程中都起着特定的作用,有助于形成所需的薄膜。
PECVD 的主要技术指标之一是能在低于 540 °C 的温度下运行,因此适用于多种基底。工艺室通常配备多个气室,如硅烷室(A + C)和 TEOS(正硅酸四乙酯)室(B),每个气室都设计用于处理不同的气体混合物和沉积要求。这种模块化设计使沉积过程具有更大的灵活性和可控性,确保生产出具有精确特性的高质量薄膜。
金属有机化学气相沉积 (MOCVD)
金属有机化学气相沉积 (MOCVD) 是一种先进的外延生长技术,利用金属有机化合物作为前驱气体来沉积金属和半导体薄膜。这种方法的显著特点是能够生长各种化合物半导体,包括 Ⅲ-V 和 Ⅱ-VI 材料,以及它们的多层固溶体。
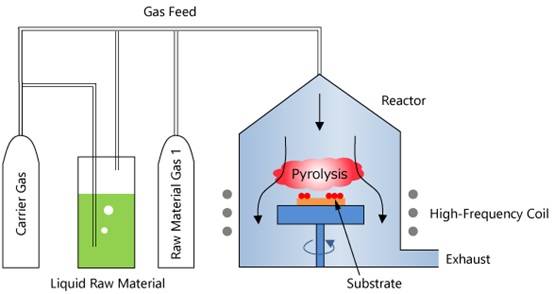
MOCVD 的主要特点
-
源材料:MOCVD 采用第 III 族和第 II 族元素的有机化合物以及第 V 族和第 VI 族元素的氢化物作为晶体生长的主要源材料。这些材料以气态形式进入反应室,经过热分解后在基底上形成单晶薄层。
-
精确控制:MOCVD 的显著优势之一是可精确控制沉积薄膜的成分和掺杂浓度。这种精度是通过调节气体前驱体的流速和开/关时间来实现的,从而可以高精度地生长薄层和超薄层材料。
-
快速切换:反应腔内相对较快的气体流速可快速改变多种化合物的成分和掺杂浓度。这种快速切换能力降低了产生记忆效应的可能性,有利于形成陡峭的界面,使 MOCVD 成为生长异质结构、超晶格和量子阱材料的理想选择。
与其他外延技术相比的优势
与其他外延生长方法相比,MOCVD 具有几个明显的优势:
优势 | 描述 |
---|---|
成分控制 | 前驱体的气态可实现对成分、掺杂浓度和外延层厚度的精确控制。 |
快速调整 | 气体流速的快速变化可实现化合物成分的快速调整,从而减少记忆效应并提高界面质量。 |
多功能性 | 适用于多种化合物半导体,包括Ⅲ-V 和Ⅱ-VI 材料,使其在各种应用中具有高度的通用性。 |
CVD 的应用
半导体制造
在半导体制造中,化学气相沉积(CVD)在创造先进材料以提高设备性能和可靠性方面发挥着关键作用。该工艺涉及各种薄膜的沉积,包括硅化物、氮化物薄膜和金属薄膜,每种薄膜都是为半导体行业的特定应用而量身定制的。
硅化物
硅化物是硅与金属反应形成的,对于降低接触电阻和提高半导体器件的效率至关重要。它们通常用于栅极、互连和接触垫。例如,硅化钨(WSi₂)因其低电阻率和热稳定性而常被用于 CMOS 技术。
氮化物薄膜
氮化硅(Si₃N₄)等氮化物薄膜在半导体制造中具有多种用途。它们既是扩散屏障,防止掺杂剂和杂质的迁移,又是钝化层,保护器件不受环境因素的影响。此外,氮化膜还是形成 DRAM 器件中电容器不可或缺的一部分,可确保高电容和低漏电流。
金属膜
包括铝(Al)和铜(Cu)在内的金属薄膜对于在集成电路中形成促进电信号流动的互连是必不可少的。铜因电阻率低、能降低功耗和发热量而受到青睐。使用 CVD 沉积这些金属膜可确保均匀的覆盖率和出色的附着力,这对保持半导体器件的完整性和性能至关重要。
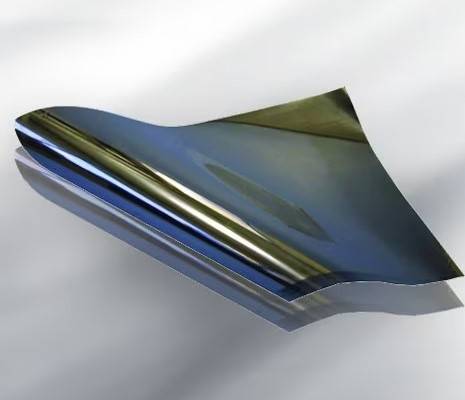
利用 CVD 技术,半导体制造商可以实现对沉积过程的精确控制,从而生产出符合现代电子设备严格要求的高质量薄膜。
显示技术
在显示技术领域、氧化铟锡 (ITO) 薄膜 和铜薄膜 发挥着举足轻重的作用。这些材料是制造各种显示设备、提高其性能和功能所不可或缺的。
氧化铟锡(ITO)薄膜
ITO 薄膜以其卓越的导电性和光学透明度而闻名。这种独特的组合使其成为以下应用的理想材料:
- 触摸屏:为触摸感应显示器提供必要的导电层。
- 电致发光面板:促进显示器发光。
- 太阳能电池:在导电的同时允许光线通过,从而提高光伏设备的效率。
铜膜
铜薄膜则以其高导电性和机械强度而著称。这些特性可用于
- 柔性显示器:提供耐用性和高效信号传输。
- 高分辨率显示器:确保最小的信号损失和高速数据处理。
- 先进的封装:支持复杂电子系统的互连。
通常采用以下方法沉积 ITO 和铜膜化学气相沉积(CVD) 技术,可精确控制薄膜厚度和均匀性,确保显示设备的最佳性能。
其他领域
化学气相沉积 (CVD) 技术的应用范围已超出半导体制造和显示技术,渗透到需要精密耐用涂层的各个行业。其中一个突出的应用领域是光学镀膜在光学镀膜领域,CVD 被用来在透镜、反射镜和其他光学元件上沉积薄膜。这些涂层可增强透光性、减少反射并提高整体光学性能,因此在电信、航空航天和医学成像等领域不可或缺。
另一个重要应用领域是防腐蚀涂层.CVD 技术用于在金属和合金上形成保护层,使其免受恶劣环境条件的影响,并延长其使用寿命。这在汽车、航空航天和海洋工程等行业尤为重要,因为这些行业的材料都暴露在腐蚀性元素中。
应用领域 | 行业影响 |
---|---|
光学涂层 | 增强光学设备的性能,对电信和医疗成像至关重要。 |
防腐蚀涂层 | 保护汽车、航空航天和航海领域的金属,延长使用寿命。 |
这些应用凸显了 CVD 技术的多功能性和坚固性,使其成为现代工业流程的基石。
CVD 工艺特点
高温要求
化学气相沉积(CVD)工艺的高温要求至关重要,原因有以下几点。首先,高温对以下方面至关重要提高反应速度 前驱气体的反应速度。加热时,这些气体会在基底表面发生分解和随后的化学反应,从而形成所需的薄膜。热量提供的动能可确保分子有足够的能量进行反应并形成稳定的键。
此外,高温还有助于提高反应物在基底上的扩散速度 反应物在基底上的扩散速度。这种扩散对于在整个表面实现均匀的薄膜沉积至关重要。如果没有足够的热量,扩散过程就会缓慢,导致薄膜不均匀,并可能产生缺陷。
此外,高温还能起到以下作用去除杂质 反应环境中的杂质。水分或残留气体等杂质可在高温下被驱除,从而确保沉积过程更加清洁。在制造半导体器件中使用的高纯度材料时,这种净化作用尤为重要。
温度范围 | 效果 |
---|---|
低(<400°C) | 反应速率慢,扩散受限,可能产生不均匀薄膜。 |
中温(400-800°C) | 优化了许多 CVD 工艺,平衡了反应和扩散速率。 |
高(>800°C) | 反应速度快,扩散速率高,但可能超过基底热极限。 |
真空环境
CVD 过程通常在真空环境下进行。这种受控气氛至关重要,原因有以下几点。首先,真空可最大限度地减少氧气和水蒸气等污染物的存在,否则这些污染物可能会干扰化学反应并降低沉积薄膜的质量。其次,保持真空有助于管理沉积腔内的压力,确保气体前驱体以最佳速率流动,并在基底表面进行有效反应。
在真空中,气体分子的平均自由路径增加,从而减少了分子间的碰撞。碰撞的减少使气体前驱体更有方向性地流向基底,从而增强了沉积过程。此外,真空环境有利于更好地控制温度和压力条件,而这正是 CVD 过程中的关键参数。
优点 | 说明 |
---|---|
减少污染物 | 最大限度地减少氧气和水蒸气的干扰。 |
压力管理 | 确保气体前驱体的最佳流动和反应。 |
增加平均自由路径 | 减少分子碰撞,提高沉积效果。 |
温度控制 | 便于更好地控制关键参数。 |
真空环境不仅是一项技术要求,也是支撑 CVD 工艺效率和精度的基本要素。通过保持真空,制造商可以获得具有所需特性的高质量、均匀的薄膜,这也是 CVD 技术不可或缺的一部分。
表面处理
在任何涂层工艺,尤其是化学气相沉积 (CVD) 工艺之前,基材表面必须经过严格的制备,以确保最佳的附着力和薄膜质量。这一步骤至关重要,因为它直接影响到沉积薄膜的性能和使用寿命。
有机残留物、氧化物和水分等杂质必须仔细去除。这些杂质会阻碍薄膜形成所需的化学反应,并导致针孔或涂层不均匀等缺陷。表面处理的技术各有不同,但常见的方法包括化学清洗,蚀刻和等离子处理.
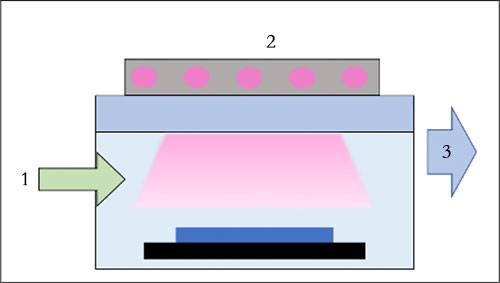
-
化学清洗:这包括使用溶剂或酸来溶解和去除有机和无机污染物。例如,RCA 清洁是一种使用过氧化氢和硫酸混合物清洁硅晶片的标准方法。
-
蚀刻:这种方法利用化学反应选择性地去除表面层。例如,氢氟酸通常用于去除硅基板上的原生二氧化硅。
-
等离子处理:这种技术使用等离子体激活表面,增强其反应能力并清除残留污染物。它对去除有机残留物和提高表面能特别有效。
上述每种方法在确保基底无污染物方面都起着至关重要的作用,从而有助于成功沉积高质量的薄膜。正确的表面处理不仅能增强沉积薄膜的附着力,还能确保薄膜的特性(如均匀性和密度)符合所需的规格。
基底限制
在化学气相沉积(CVD)工艺中,温度和反应性限制是严重限制适用基底范围的关键因素。发生化学反应所需的高温会对基底材料造成热限制,从而使基底材料只能选择那些能够承受这种极端条件而不会降解或变形的材料。例如,某些有机材料或低熔点金属可能因无法在高温下保持结构完整性而不适用。
此外,前驱体气体的反应性以及由此产生的与基底表面的化学作用会进一步缩小合适材料的选择范围。某些基底可能会与沉积气体发生不利的反应,导致不良的副反应或形成不均匀的薄膜。这种反应性限制要求对基底进行仔细选择和预处理,以确保与 CVD 工艺的兼容性。
覆盖和遮蔽
在化学气相沉积(CVD)过程中,覆盖和掩蔽过程对沉积薄膜的最终质量和功能起着至关重要的作用。虽然 CVD 能确保基底的所有区域都均匀地覆盖所需的材料,但有选择地掩蔽特定区域的能力成为实现精确图案和结构的关键因素。
CVD 的覆盖能力非常有效,因为它通常能使材料在整个基底表面均匀沉积。这种均匀性对于需要均匀薄膜厚度的应用(如半导体制造和显示技术)至关重要。然而,当需要保护基底的特定区域不受沉积过程影响时,难题就来了。这就是掩膜技术发挥作用的地方。
CVD 中的掩膜技术包括使用物理屏障或光阻层来防止材料在特定区域沉积。虽然这种技术普遍有效,但也有其局限性。例如,掩蔽工艺的精度会受到基底类型、图案复杂程度和所用特定 CVD 参数等因素的影响。此外,掩膜材料本身也必须谨慎选择,以确保它们不会与沉积气体发生反应,或在 CVD 工艺通常涉及的高温下降解。
薄膜厚度限制
通过化学气相沉积 (CVD) 工艺沉积的薄膜厚度本身受到几个因素的限制,主要是工艺参数和相关材料的物理状态。这些限制对于了解 CVD 技术的实际应用和界限至关重要。
工艺参数
沉积过程本身会对薄膜厚度造成若干限制。关键因素包括
- 温度和压力:CVD 反应所需的高温会限制沉积薄膜的厚度。极端温度会导致薄膜热降解或不均匀。同样,进行工艺的压力也会影响薄膜的生长速度和均匀性。
- 反应动力学:前驱气体反应并形成所需薄膜的速度是另一个限制因素。如果工艺控制不严,较快的反应速度会导致薄膜变薄。
材料状态
前驱体材料的物理和化学特性也起着重要作用:
- 前驱体稳定性:前驱体气体在高温下的稳定性会限制薄膜的厚度。不稳定的前驱体可能会过早分解,导致薄膜不完整或不均匀。
- 基底兼容性:基底材料能否承受沉积条件至关重要。某些基底可能无法承受较厚薄膜沉积所需的高温或反应性。
这些限制不仅仅是局限性,而且是整个工艺不可或缺的一部分,可确保沉积的薄膜质量上乘,适合预期应用。
附着力
出色的附着力是化学气相沉积(CVD)技术的一大特点,这对其生产的薄膜的耐用性和功能性至关重要。这些薄膜的附着力受多种因素的影响,包括基底的表面处理、前驱气体的化学反应性以及温度和压力等工艺条件。
例如,适当的表面制备可确保去除污染物,形成清洁和活性表面,从而增强薄膜与基底之间的粘合力。这一步骤在半导体制造中尤为重要,因为即使是微小的杂质也会导致严重的性能问题。
前驱气体的化学性质也起着至关重要的作用。前驱气体和基底表面之间的反应会形成强大的化学键,这是 CVD 薄膜具有出色附着力的基础。这种化学键机制确保沉积的薄膜即使在苛刻的操作条件下也能牢固地附着在基底上。
CVD 所需的高温等工艺条件进一步促进了强附着力。这些高温不仅能促进形成薄膜所需的化学反应,还能使薄膜材料更好地扩散到基底中,形成更坚固的界面。
CVD 技术的优势
均匀性
化学气相沉积 (CVD) 的均匀性是确保大面积基底上薄膜质量一致的关键属性。这种均匀性是通过对温度、压力和前驱体流速等工艺参数的精细控制实现的。保持均匀性的能力在半导体制造中尤为重要,因为在半导体制造中,即使是微小的变化也会导致最终产品出现严重的性能问题。
举例说明,在典型的 CVD 设置中,基底暴露在均匀的前驱体气体流中。气体分子在基片表面扩散和反应,形成薄膜。通过精确管理这些气体的分布,制造商可以确保沉积在整个基底上均匀地进行,无论其大小如何。先进的反应器设计通常能促进气体的均匀分布,并最大限度地减少局部变化。
参数 | 对均匀性的影响 |
---|---|
温度 | 确保前驱体均匀分解和沉积。 |
压力 | 有助于保持一致的气体流量和反应速率。 |
前驱体流量 | 控制反应物的浓度和分布。 |
总之,CVD 工艺的均匀性不仅是一个理想的特性,也是生产高质量薄膜的基本要求。它强调了精确工艺控制和先进反应器技术在大型基底上实现一致结果的重要性。
可控性
化学气相沉积(CVD)技术的突出特点之一是对沉积过程的高度可控性。这种可控性对于实现精确的薄膜特性和沉积速率至关重要,而这对于半导体制造、显示技术等领域的各种应用至关重要。
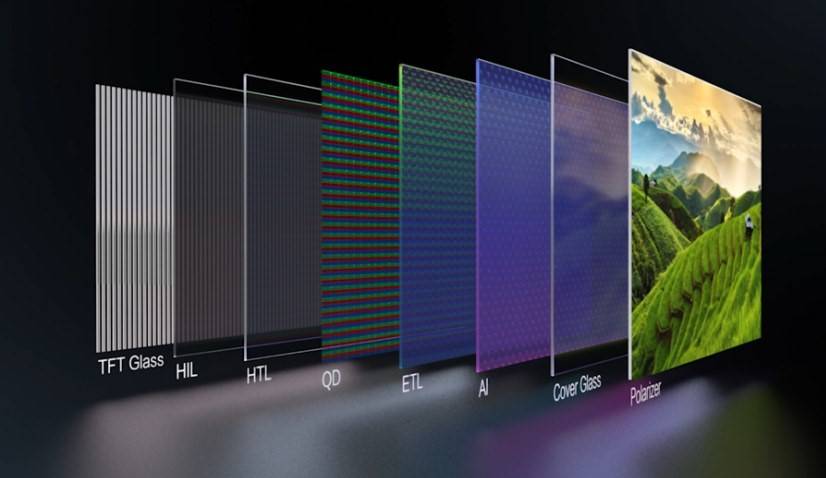
沉积速率控制
CVD 中的沉积速率可通过调整几个参数进行精细控制。这些参数包括
- 温度:通过改变基底和前驱气体的温度,可对化学反应的速率进行微调。温度越高,反应速度越快,沉积速度也越快。
- 压力:在不同的压力下运行会影响前驱气体的流动动态以及它们到达基底表面的速度。
- 气体流速:通过控制前驱气体的流速,可精确调整基底上反应物的浓度,从而影响沉积速率。
薄膜特性定制
除了沉积速率外,CVD 还能对生成薄膜的特性进行广泛控制。可定制的主要特性包括
- 薄膜厚度:通过仔细管理工艺参数,可将沉积薄膜的厚度控制在较小的范围内,从而确保大型基底上薄膜的均匀性。
- 化学成分:使用不同的前驱气体或混合物,可沉积出不同化学成分的薄膜,以满足特定的应用要求。
- 晶体结构:温度和压力条件可影响沉积薄膜的结晶度,从而根据需要形成无定形或晶体结构。
- 应力:可控制薄膜内部的应力,以防止出现缺陷,并确保薄膜的完整性和与基底的粘附性。
工艺灵活性
CVD 的可控性还包括工艺本身的灵活性。不同类型的 CVD(如热 CVD、等离子体增强 CVD (PECVD) 和金属有机 CVD (MOCVD))具有独特的优势和控制机制。例如,PECVD 使用等离子体来提高反应速度,并提供对沉积过程的额外控制,而 MOCVD 允许使用金属有机化合物来沉积复杂的材料。
多功能性
化学气相沉积(CVD)技术因其卓越的多功能性而脱颖而出,成为各行各业的基石。这种多功能性主要归功于其沉积各种材料的能力,每种材料都是为特定应用量身定制的。无论是制造高质量的半导体薄膜、增强显示技术,还是开发保护涂层,CVD 都证明了其对不同材料类型和功能要求的适应性。
材料多样性
CVD 处理不同材料的能力是其一大优势。从硅和金属膜到氮化物和氧化物等复杂化合物,可加工的材料范围非常广泛。这一广泛的范围确保了 CVD 能够满足从微电子到先进光学等现代技术应用的严格要求。
应用灵活性
除了材料的多样性,CVD 的灵活性还体现在它在多个领域的应用上。在半导体制造领域,CVD 是制造硅化物、氮化物薄膜和金属层不可或缺的工具,每种材料都对设备性能起着至关重要的作用。在显示技术领域,CVD 可用于沉积氧化铟锡(ITO)和铜膜,从而增强屏幕的功能性和耐用性。此外,CVD 还可用于光学涂层和防腐蚀处理等不太传统的领域,这进一步说明了它的多功能性。
工艺适应性
CVD 工艺的适应性是其多功能性的另一个方面。热化学气相沉积、等离子体增强化学气相沉积(PECVD)和金属有机化学气相沉积(MOCVD)等技术都具有独特的优势,可以精确控制沉积过程。这种适应性确保了 CVD 能够针对不同的基底和环境条件进行优化,使其成为研究人员和工程师手中的多功能工具。
联系我们获取免费咨询
KINTEK LAB SOLUTION 的产品和服务得到了世界各地客户的认可。我们的员工将竭诚为您服务。如需免费咨询,请与我们的产品专家联系,以找到最适合您应用需求的解决方案!