与热蒸发相比,电子束蒸发具有多项优势,因此成为许多薄膜沉积应用的首选。其主要优势包括:沉积薄膜的纯度更高、对蒸发过程的控制更好、能够处理熔点更高的材料以及沉积速率更快。电子束蒸发还能保持坩埚冷却,只加热目标材料,从而最大限度地降低污染风险。这些特点使其适用于需要高纯度、致密和均匀涂层的应用,尤其是在半导体、光学和先进材料等行业。
要点说明
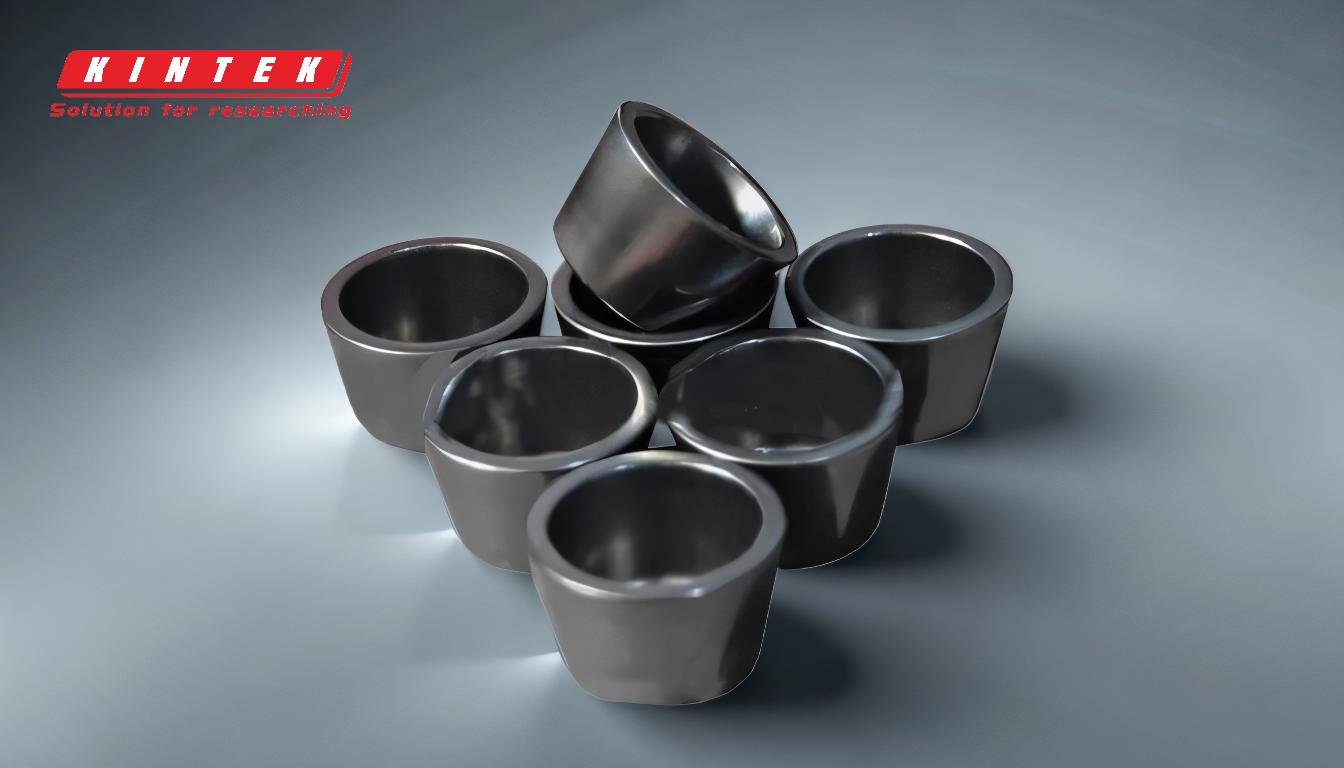
-
更高纯度的薄膜:
- 与热蒸发法相比,电子束蒸发法生产的薄膜纯度要高得多。这是因为电子束只直接加热目标材料,而坩埚则保持室温,从而避免了杂质的污染。
- 在热蒸发过程中,整个坩埚都会被加热,这可能会导致源材料和坩埚在高温下发生反应而污染沉积薄膜。
-
处理高熔点材料的能力:
- 电子束蒸发可以沉积具有高熔点的材料,如氧化物和难熔金属,而热蒸发很难或根本无法加工这些材料。
- 热蒸发仅限于熔化温度较低的材料,限制了其对先进材料的适用性。
-
精确控制蒸发过程:
- 在电子束蒸发中使用高能电子束可以精确控制蒸发速率和沉积过程。这种精确性对于要求薄膜均匀一致的应用至关重要。
- 热蒸发依靠加热坩埚,控制能力较差,可能导致蒸发率不一致。
-
更高的沉积率:
- 与热蒸发相比,电子束蒸发的沉积率更高,因此在大规模或高通量应用中更为高效。
- 沉积速率的提高尤其有利于对时间和成本效率要求较高的工业应用。
-
涂层更致密、更均匀:
- 电子束蒸发可产生更致密的薄膜涂层,并与基底具有极佳的附着力。这得益于高能量工艺和精确控制沉积参数的能力。
- 在电子束蒸发过程中使用掩膜和行星系统可进一步提高涂层的均匀性,这对光学和电子领域的应用至关重要。
-
降低污染风险:
- 电子束蒸发中的坩埚冷却可防止杂质污染,确保薄膜的高纯度。这对于半导体和其他高科技行业的应用尤为重要。
- 另一方面,热蒸发需要加热坩埚,这可能会引入杂质并降低薄膜质量。
-
与离子辅助沉积 (IAD) 兼容:
- 电子束蒸发系统可与离子辅助源集成,用于预清洁或离子辅助沉积(IAD)。这种功能可增强薄膜的特性,如附着力和密度,使其适用于高级应用。
- 热蒸发不具备这种集成度,限制了其多功能性。
-
更好的台阶覆盖率:
- 与溅射或化学气相沉积(CVD)相比,电子束蒸发能提供更出色的阶跃覆盖。这对于复杂几何形状或具有复杂特征的基底镀膜尤其有利。
- 热蒸发通常难以实现阶梯式覆盖,导致此类基底上的涂层不均匀。
-
更高的材料利用效率:
- 与溅射法相比,电子束蒸发具有更高的材料利用效率,可减少材料浪费并降低成本。
- 这种效率也是电子束蒸发技术成为高价值材料和大规模生产首选的另一个原因。
-
适用于多种材料的多功能性:
- 电子束蒸发可与多种材料兼容,包括金属、氧化物和合金。这种多功能性使其适用于多个行业的各种应用。
- 热蒸发法可加工的材料范围较为有限,因此只能用于较为简单的应用。
总之,电子束蒸发在纯度、控制、材料多样性和沉积效率方面都优于热蒸发。这些优势使其成为要求高质量、均匀和无污染薄膜应用的首选方法。
总表:
优势 | 电子束蒸发 | 热蒸发 |
---|---|---|
薄膜的纯度 | 由于目标材料和冷却坩埚直接加热,纯度更高。 | 纯度较低,因为要加热整个坩埚,有污染的风险。 |
高熔点材料 | 可处理氧化物和难熔金属等材料。 | 仅限于熔点较低的材料。 |
控制蒸发 | 精确控制蒸发速度和沉积过程。 | 控制较少,导致蒸发率不一致。 |
沉积率 | 沉积率更高,是大规模应用的理想选择。 | 沉积率较低,效率较低,无法满足高吞吐量需求。 |
涂层均匀性 | 涂层更致密、更均匀,附着力极佳。 | 涂层不够均匀,尤其是在复杂几何形状上。 |
污染风险 | 冷却坩埚可减少污染。 | 加热坩埚造成污染的风险更高。 |
离子辅助沉积(IAD) | 与 IAD 兼容,可增强薄膜性能。 | 与 IAD 不兼容,限制了通用性。 |
步骤覆盖范围 | 卓越的阶跃覆盖率,适用于复杂几何形状。 | 步骤覆盖率低,导致涂层不均匀。 |
材料利用效率 | 提高效率,减少浪费,降低成本。 | 效率较低,造成更多的材料浪费。 |
材料多样性 | 与金属、氧化物和合金兼容,适用于各种应用。 | 仅限于较简单的材料,限制了其使用。 |
准备好提升您的薄膜沉积工艺了吗? 立即联系我们 了解电子束蒸发如何满足您的需求!