溅射是一种广泛使用的薄膜沉积技术,以高纯度、精确控制和均匀性著称。然而,它也有一些缺点,会影响其效率、成本和应用适用性。主要缺点包括沉积速率较慢、设备和操作成本高、对热敏感、薄膜污染风险以及在实现均匀薄膜厚度方面的挑战。此外,溅射技术在材料选择、过程控制以及与其他制造技术的整合方面也面临着限制。这些因素使得溅射技术不太适合某些应用,尤其是那些要求高产量、低污染或复杂材料组合的应用。
要点说明:
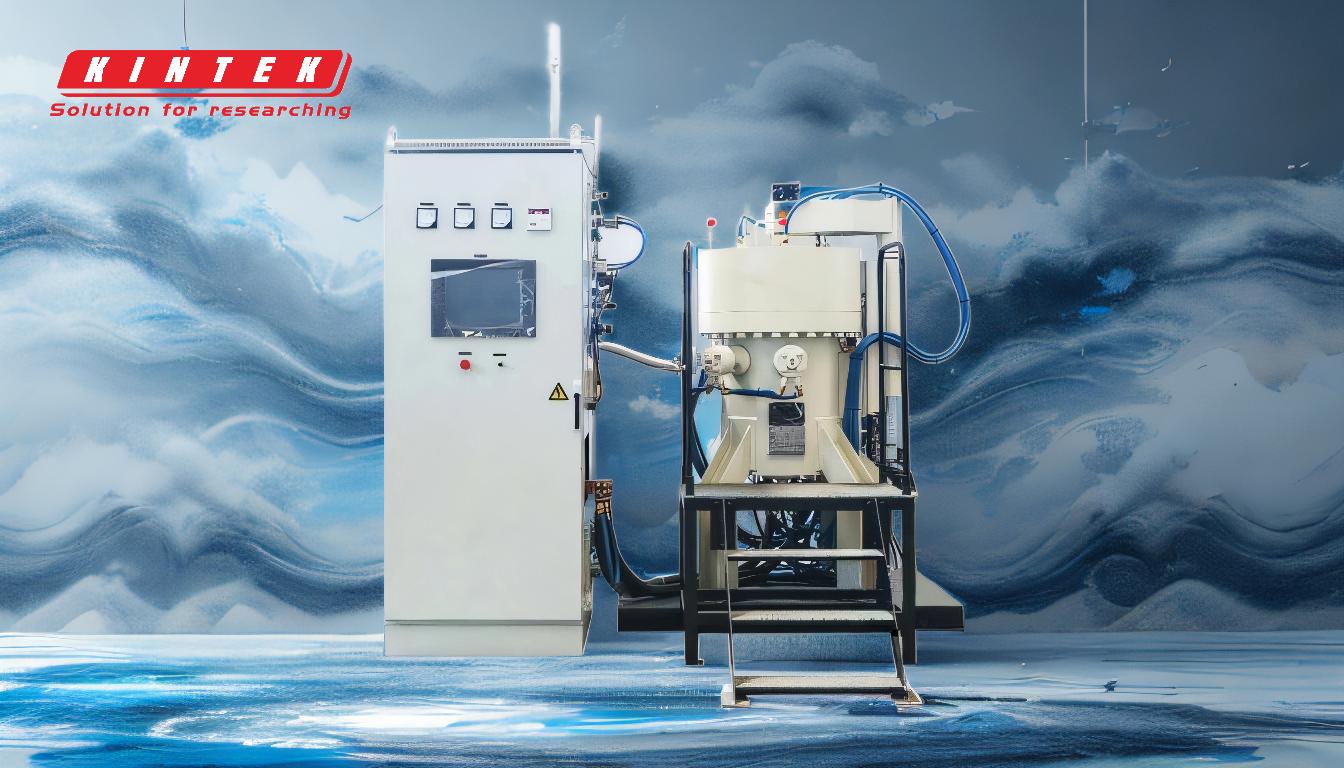
-
较慢的沉积速率
- 与热蒸发等方法相比,溅射法的沉积速率通常较低。这是由于该工艺的物理特性决定的,即原子从目标材料中喷射出来并沉积到基底上。较慢的速度会限制产量,使其不太适合大批量生产。
-
设备和运营成本高
- 溅射系统的购买和维护费用昂贵。需要高质量的真空系统、射频或直流电源以及冷却系统,这些都增加了总成本。此外,溅射靶材通常成本高昂,材料使用效率低,进一步增加了开支。
-
热敏感性和冷却要求
- 溅射过程中使用的能量有很大一部分转化为热量,必须有效地去除这些热量,以防止损坏基片或靶材。冷却系统是必需的,但它会降低生产速度,增加能耗,从而增加运行成本。
-
薄膜污染风险
- 溅射会给沉积薄膜带来污染。靶材中的杂质或等离子体中的气体污染物会被激活并融入薄膜中。这在反应溅射中尤为严重,因为在反应溅射中必须仔细控制气体成分,以避免靶材中毒。
-
实现均匀膜厚的挑战
- 溅射过程中的沉积流量分布往往不均匀,尤其是对于大型基底或靶材。为了达到均匀的厚度,可能需要移动夹具或进行复杂的设置,这就增加了工艺的复杂性和成本。
-
材料选择的限制
- 溅射受目标材料熔点和特性的限制。有些材料由于熔点低或其他物理特性可能不适合溅射,从而限制了可生产涂层的范围。
-
难以与掀离工艺相结合
- 要将溅射技术与薄膜成型中使用的掀离工艺结合起来是一项挑战。由于溅射原子的扩散传输,不可能形成完全的阴影,从而导致污染并难以实现精确的图案。
-
主动控制挑战
- 与脉冲激光沉积等其他沉积方法相比,溅射法对逐层生长的主动控制能力较弱。这可能会限制其在需要精确原子级控制的应用中的使用。
-
高工作压力和密封问题
- 传统溅射工艺在相对较高的压力下运行,这可能导致弹性体密封件渗透和其他真空系统问题。这些问题会影响沉积过程的质量和效率。
-
等离子密度不均匀
- 对于大型矩形阴极(例如大于 1 米),实现均匀的等离子体密度可能比较困难,从而导致层厚度分布不均匀。这需要额外的工程解决方案来解决。
-
能源效率低
- 入射到靶材上的大部分能量都转化为热量,而不是用于沉积,因此与其他技术相比,该工艺的能效较低。
-
反应溅射的并发症
- 在反应溅射中,精确控制气体成分对避免靶材中毒至关重要,因为靶材表面会发生化学变化,从而降低沉积效率和薄膜质量。
通过了解这些缺点,设备和耗材购买者可以在考虑成本、产量和材料要求等因素的基础上,就溅射技术是否适合其特定应用做出明智的决定。
汇总表:
劣势 | 关键细节 |
---|---|
沉积速度较慢 | 与热蒸发等方法相比,吞吐量较低。 |
设备和运营成本高 | 昂贵的系统、真空要求和昂贵的溅射靶材。 |
热敏感性 | 需要冷却系统,降低了生产率,增加了能源消耗。 |
薄膜污染风险 | 靶材或等离子体中的杂质会影响薄膜质量。 |
均匀膜厚的挑战 | 沉积流量不均匀,尤其是在大型基底上。 |
材料选择限制 | 受目标材料特性和熔点的限制。 |
与脱模工艺相结合 | 难以与精确的薄膜结构技术相结合。 |
主动控制挑战 | 与其他方法相比,逐层生长的精度较低。 |
操作压力高 | 可能导致真空系统挑战和密封问题。 |
等离子体密度不均匀 | 大型阴极很难达到均匀的等离子体密度。 |
能量效率低 | 大部分能量转化为热量,而非沉积。 |
反应溅射的并发症 | 需要精确的气体控制以避免靶材中毒。 |
需要帮助决定溅射是否适合您的应用? 立即联系我们的专家 获取量身定制的建议!