热蒸发沉积(TVD),尤其是热蒸发,因其简单和成本效益高而被广泛应用于薄膜沉积技术。然而,它也有一些缺点,限制了它在某些情况下的应用。这些缺点包括薄膜均匀性差、杂质含量高、薄膜质量密度低、薄膜应力适中以及可扩展性有限。此外,热蒸发仅限于熔点相对较低的材料,而且容易受到坩埚的污染。这些限制使其不太适合需要高纯度、高密度或多组分材料的高级应用。
要点说明:
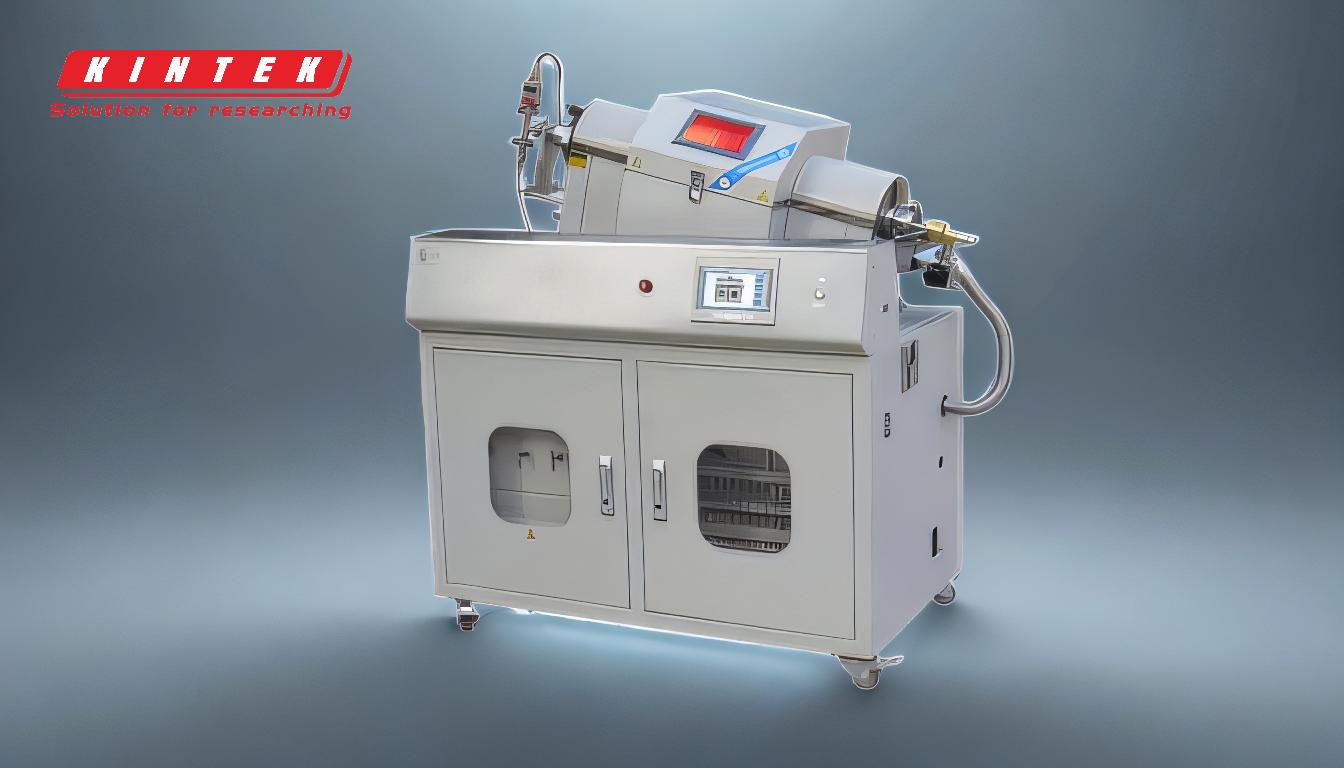
-
胶片均匀性差:
- 如果不使用行星系统和掩膜,热蒸发往往会导致基底上的薄膜厚度不均匀。这对于需要精确和均匀涂层的应用来说是一个重大缺陷。
- 缺乏均匀性会导致材料特性不一致,这在电子和光学等行业尤为严重。
-
杂质含量高:
- 在物理气相沉积 (PVD) 方法中,热蒸发法的杂质含量通常最高。这是由于坩埚和蒸发源材料造成的污染。
- 杂质含量高会降低沉积薄膜的性能,使其不适合半导体制造等高纯度应用。
-
低密度薄膜质量:
- 热蒸发法生产的薄膜通常密度较低,这会影响其机械和电气性能。虽然离子辅助技术可以改善这种情况,但却增加了工艺的复杂性和成本。
- 低密度薄膜更容易产生缺陷,可能无法提供某些应用所需的耐久性。
-
中等薄膜应力:
- 热蒸发沉积的薄膜通常具有中等应力,随着时间的推移,可能会出现裂纹或分层等问题。
- 在薄膜需要承受机械应力或热循环的应用中,这种问题尤为突出。
-
可扩展性有限:
- 热蒸发不容易扩展到大面积或高吞吐量应用。与溅射或化学气相沉积(CVD)等其他沉积方法相比,该工艺通常速度较慢,效率较低。
- 这一局限性使其对工业规模生产的吸引力大打折扣。
-
材料限制:
- 热蒸发主要适用于熔点相对较低的材料。它不能有效地沉积难熔金属或需要很高温度的材料。
- 这就限制了使用这种方法沉积的材料范围,限制了其通用性。
-
坩埚污染:
- 在热蒸发过程中使用坩埚会将污染物带入沉积薄膜,进一步降低薄膜的纯度和质量。
- 这对于需要高纯度材料的应用领域(如半导体或光学行业)来说是一个重大缺陷。
-
多组分材料面临的挑战:
- 由于不同成分之间的蒸汽压力、成核和生长速度存在差异,热蒸发对沉积多成分材料的效果较差。
- 这就很难获得均匀的成分,而这对于许多先进应用来说至关重要。
总之,虽然热蒸发是一种简单且经济高效的薄膜沉积方法,但其缺点--如均匀性差、杂质含量高、薄膜密度低、应力适中、可扩展性有限、材料限制、坩埚污染以及对多组分材料的挑战--使其不太适合高级或高精度应用。有关热蒸发的更多信息,请访问 热蒸发 .
总表:
缺点 | 描述 |
---|---|
薄膜均匀性差 | 厚度不均匀,材料特性不一致,对电子产品来说是个问题。 |
杂质含量高 | 来自坩埚和源材料的污染,不适合用于高纯度用途。 |
低密度薄膜质量 | 容易产生缺陷,影响机械和电气性能。 |
中度薄膜应力 | 导致开裂或分层,在机械或热应力下出现问题。 |
可扩展性有限 | 不适合大面积或高吞吐量的工业应用。 |
材料限制 | 仅限于低熔点材料,限制了通用性。 |
坩埚污染 | 引入杂质,降低薄膜纯度和质量。 |
多组分材料面临的挑战 | 难以实现先进应用中的均匀成分。 |
需要更好的薄膜沉积解决方案? 立即联系我们的专家 探索先进的替代方案!