物理气相沉积(PVD)和化学气相沉积(CVD)是在基底上沉积薄膜的两种广泛使用的技术,但它们在机理、工艺和应用上有很大不同。PVD 是将固体材料物理转化为蒸汽,然后沉积到基底上,而 CVD 则是依靠气态前驱体之间的化学反应在基底上形成固体薄膜。CVD 通常在较高温度下运行,会产生腐蚀性副产品,而 PVD 在较低温度下运行,可避免此类问题。这两种方法都具有独特的优势,例如 CVD 能够生产高纯度薄膜,而 PVD 在沉积技术方面具有多样性。
要点说明:
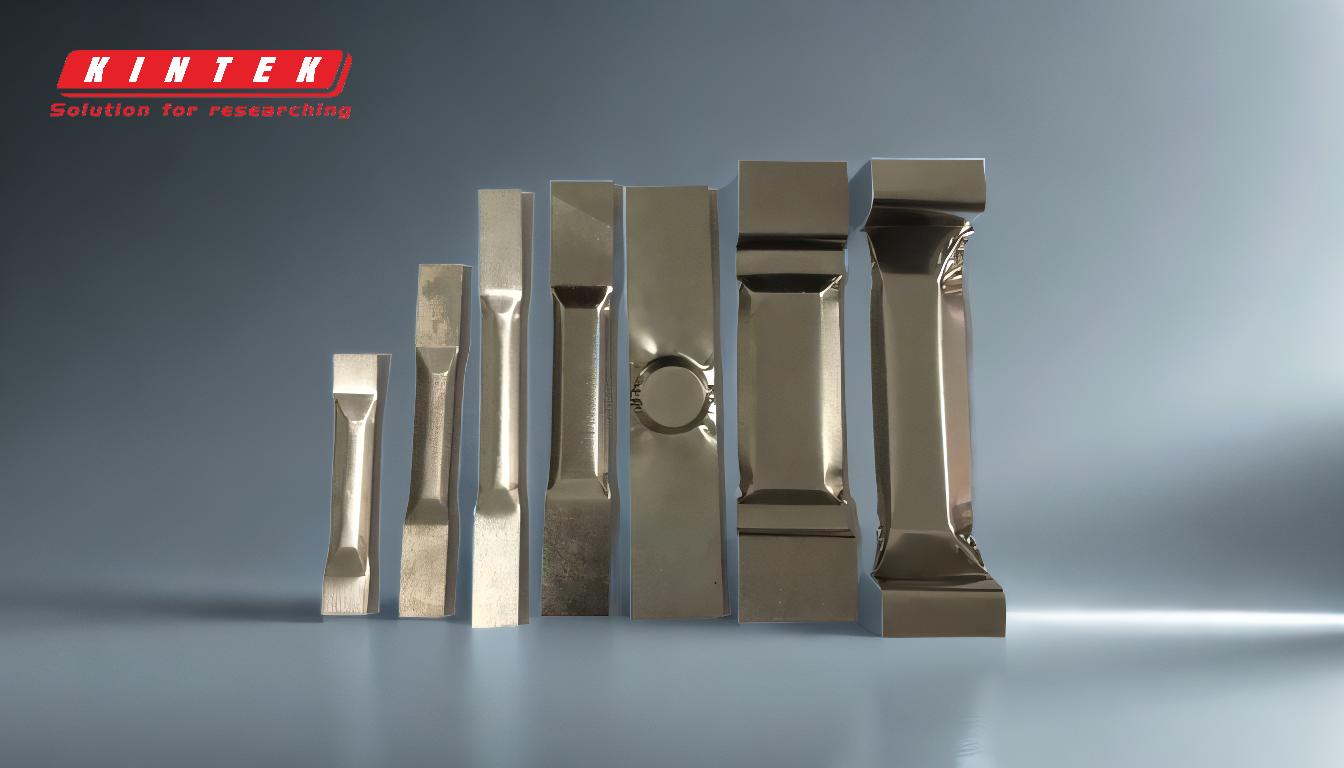
-
沉积机制:
- PVD:包括通过蒸发、溅射或升华等过程将固体材料物理转化为蒸汽。气化后的原子或分子凝结在基底上形成薄膜。
- 化学气相沉积:依靠气态前驱体之间的化学反应。这些前驱体在基底表面发生反应或分解,形成固态薄膜。这一过程通常需要高温来促进化学反应。
-
温度要求:
- PVD:与 CVD 相比,PVD 的工作温度通常较低。因此,PVD 适用于无法承受高温的基底。
- CVD:一般需要高温(通常在 500°C 至 1100°C 之间)来激活薄膜沉积所需的化学反应。
-
沉积速率和效率:
- PVD:沉积速率通常较低,但电子束物理气相沉积(EBPVD)等技术可实现较高的沉积速率(0.1 至 100 μm/min)和较高的材料利用效率。
- 气相沉积:可实现较高的沉积率,但该工艺可能会产生腐蚀性气体副产品,从而使工艺复杂化,并需要额外的处理。
-
材料利用:
- PVD:材料利用效率高,特别是在 EBPVD 等技术中,材料在蒸发和沉积过程中产生的废料极少。
- 化学气相沉积:由于涉及化学反应,可能会产生不属于最终薄膜的副产品,因此材料利用效率可能较低。
-
副产品和杂质:
- PVD:不产生腐蚀性副产品,在化学处理方面是一种更清洁的工艺。
- 化学气相沉积:会产生腐蚀性气体副产品,可能需要采取额外的安全措施,有时还会在薄膜中留下杂质。
-
应用:
- PVD:常用于要求高纯度薄膜的应用领域,如半导体工业、光学镀膜和装饰性表面处理。
- CVD:常用于需要复杂化学成分的应用领域,如生产石墨烯、碳纳米管和先进陶瓷。
-
技术和变体:
- PVD:包括溅射、蒸发和升华等技术。每种技术都有自己的优势,并根据应用的具体要求进行选择。
- 化学气相沉积:包括等离子体增强化学气相沉积(PECVD)等变体,该技术使用等离子体激活源气体,可降低加工温度,更精确地控制薄膜特性。
总之,虽然 PVD 和 CVD 都是薄膜沉积的基本技术,但它们在机理、温度要求和可沉积的材料类型上有本质区别。PVD 通常更清洁,工作温度较低,因此适用于各种基底,而 CVD 则能沉积复杂的化学成分,通常用于高温应用。选择 PVD 还是 CVD 取决于应用的具体要求,包括所需的薄膜特性、基底材料和加工条件。
汇总表:
指标角度 | PVD | 气相沉积 |
---|---|---|
机制 | 固体向蒸汽的物理转化(如溅射、蒸发)。 | 气态前驱体之间的化学反应形成固态薄膜。 |
温度 | 较低温度,适用于热敏基底。 | 高温(500°C-1100°C),适合高温工艺。 |
沉积速率 | 一般较低,但 EBPVD 可达到较高的速率(0.1-100 μm/min)。 | 沉积速率高,但可能产生腐蚀性副产品。 |
材料利用 | 效率高,浪费少。 | 由于化学副产品的存在,效率较低。 |
副产品 | 无腐蚀性副产品,工艺更清洁。 | 可能产生腐蚀性副产品,需要额外处理。 |
应用 | 高纯薄膜(半导体、光学镀膜、装饰性表面处理)。 | 复杂的化学成分(石墨烯、碳纳米管、陶瓷)。 |
技术 | 溅射、蒸发、升华。 | PECVD、等离子体增强型 CVD 可实现更低的温度和更精确的控制。 |
还不确定哪种沉积方法适合您的应用? 立即联系我们的专家 获取个性化指导!