等离子氮化层的厚度通常在几百纳米到几微米之间,具体取决于具体应用和工艺参数。等离子渗氮是一种表面硬化技术,可提高金属部件的耐磨性、疲劳强度和耐腐蚀性。氮化层的厚度受到材料成分、工艺温度、持续时间和所用等离子体类型等因素的影响。对于大多数工业应用,氮化层厚度都经过仔细控制,以确保最佳性能而不损害基材的完整性。
要点解释:
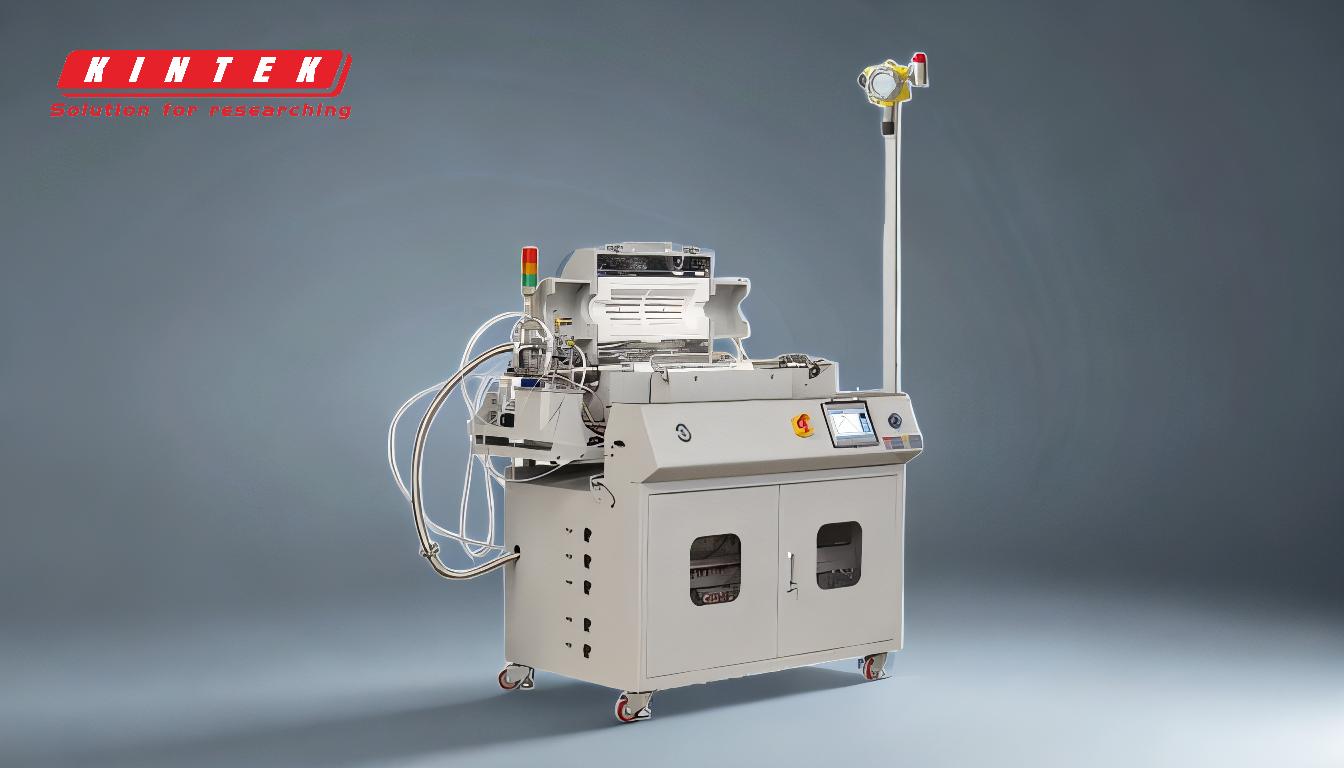
-
典型厚度范围:
- 等离子渗氮层厚度一般为 0.25微米至5微米 。该系列适用于大多数工业应用,在表面硬度和部件耐用性之间提供平衡。
- 在某些情况下,特别是对于特殊应用,厚度可以延伸至 10微米 或更多,具体取决于材料和工艺条件。
-
影响厚度的因素:
- 材料成分 :被处理材料的类型显着影响氮化层厚度。例如,由于氮扩散增强,合金元素较高的钢往往会形成较厚的层。
- 过程温度 :较高的温度通常会增加氮的扩散速率,导致氮化层更厚。然而,过高的温度会降低基材的性能。
- 过程持续时间 :较长的氮化时间允许更大的氮扩散,从而形成更厚的层。时间与厚度在一定范围内往往呈线性关系。
- 等离子体参数 :等离子气体(例如氮气、氢气或氩气混合物)的功率、压力和成分会影响氮化动力学,从而影响层厚度。
-
测量与控制:
- 氮化层的厚度通常使用以下技术测量 显微硬度测试 , 光学显微镜 , 或者 扫描电子显微镜 (SEM) 。这些方法为质量控制提供了准确可靠的数据。
- 氮化过程的精确控制对于实现所需的层厚度和均匀性至关重要。先进的等离子氮化系统通常包括实时监控和反馈机制,以确保结果一致。
-
应用和注意事项:
- 耐磨性 :较厚的氮化层通常用于需要高耐磨性的应用,例如齿轮、轴承和切削工具。
- 疲劳强度 :对于承受循环载荷的部件,精心控制的氮化层可以显着提高疲劳寿命。
- 耐腐蚀 :虽然等离子渗氮主要提高了耐磨性,但它也提供了一定程度的耐腐蚀性,特别是与氧化等后处理工艺结合使用时。
-
与其他表面处理的比较:
- 与渗碳或物理气相沉积 (PVD) 等其他表面硬化技术相比,等离子渗氮提供了硬度、附着力和均匀性的独特组合。氮化层的厚度通常比其他方法更一致且更容易控制。
通过了解这些关键点,设备和耗材购买者可以就等离子氮化工艺做出明智的决策,确保所选参数和设备满足其应用的特定要求。
汇总表:
方面 | 细节 |
---|---|
典型厚度范围 | 0.25 微米至 5 微米(特殊应用可达 10 微米) |
影响厚度的因素 | 材料成分、工艺温度、持续时间和等离子体参数 |
测量技术 | 显微硬度测试、光学显微镜、SEM |
关键应用 | 耐磨性、疲劳强度、耐腐蚀性 |
与其他方法的比较 | 比渗碳或 PVD 更一致且更容易控制 |
需要帮助优化您的等离子氮化工艺吗? 立即联系我们的专家 定制解决方案!