粉末冶金中的孔隙率是影响最终产品机械性能和性能的关键因素。减少孔隙率可以通过优化制造过程中的几个关键参数来实现。这些参数包括增加压实压力、烧结温度和烧结时间,它们共同有助于降低表观孔隙率和增加体积密度。此外,控制颗粒大小也至关重要,因为较大的颗粒往往会增加孔隙率。通过仔细管理这些因素,制造商可以生产出高密度、低孔隙率的部件,并改善其机械性能。
要点说明:
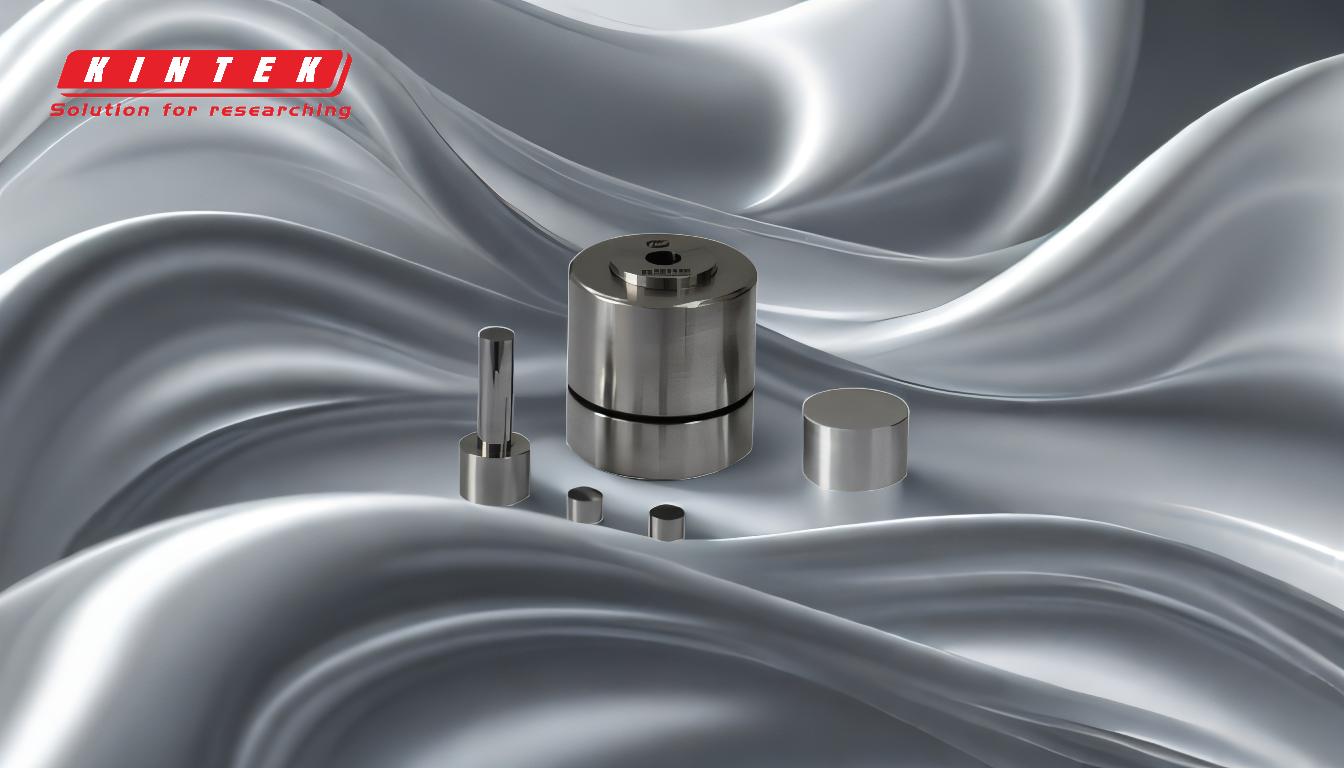
-
增加压实压力:
- 影响:较高的压实压力可减少粉末颗粒之间的间隙,从而使压实物更致密,孔隙率更低。
- 机理:在压实阶段施加压力时,颗粒会被迫靠拢,从而最大限度地减少空隙,提高绿色压实物的体积密度。
- 实际考虑因素:虽然压力越高越好,但必须与损坏模具或导致部件密度分布不均的风险相平衡。
-
优化烧结温度和时间:
- 影响:较高的烧结温度和较长的烧结时间可促进颗粒更好地结合和扩散,减少孔隙率并提高密度。
- 机理:烧结:烧结是将压实的粉末加热到熔点以下,使原子在颗粒边界扩散,从而闭合孔隙并强化材料。
- 实际考虑:温度过高或时间过长会导致晶粒长大或变形,因此有必要进行仔细优化。
-
控制颗粒大小:
- 影响:粒径越小,孔隙率越低,因为它们的堆积效率更高,留下的空隙更少。
- 机理:细颗粒的表面积与体积比更大,从而提高了烧结和粘合效果。而较大的颗粒则会产生更多的间隙,增加孔隙率。
- 实际考虑:颗粒越小越好,但也会增加结块的风险,在加工过程中必须加以控制。
-
粉末生产方法:
- 影响:生产金属粉末的方法会影响金属粉末的大小、形状和分布,进而影响孔隙率。
- 机理:雾化等技术产生的粉末具有可控的尺寸范围,可将孔隙率降至最低。粉碎和研磨可能会产生形状不规则的颗粒,包装效率较低。
- 实际考虑:选择适当的粉末生产方法对于获得理想的颗粒特性和减少孔隙率至关重要。
-
材料选择:
- 影响:由于颗粒形状、大小和烧结行为的不同,基底材料(如铜基底或铁基底)的选择会影响孔隙率。
- 机理:有些材料比其他材料更容易烧结,因此密度更高,孔隙率更低。
- 实际考虑:材料选择应符合预期应用和所需的机械性能。
通过解决这些关键因素,制造商可以有效减少粉末冶金中的孔隙率,从而提高部件的强度、耐用性和性能。
汇总表:
关键因素 | 影响 | 机制 | 实际考虑因素 |
---|---|---|---|
增加压实压力 | 减少颗粒之间的间隙,使压实物更密实,孔隙率更低。 | 压力迫使颗粒靠得更近,最大限度地减少空隙,提高堆积密度。 | 平衡压力以避免模具损坏或密度分布不均。 |
优化烧结温度和时间 | 促进颗粒结合,减少孔隙,提高密度。 | 加热至熔点以下可使原子扩散,封闭孔隙并强化材料。 | 避免温度过高或时间过长,以防晶粒长大或变形。 |
控制颗粒大小 | 较小的颗粒能有效堆积,减少孔隙。 | 细颗粒具有更高的表面积与体积比,可提高烧结和粘结效果。 | 用较小的颗粒控制结块风险。 |
粉末生产方法 | 影响颗粒大小、形状和分布,并影响孔隙率。 | 雾化可产生受控的粒度范围;粉碎/研磨则可能产生不规则颗粒。 | 请选择正确的方法来实现所需的颗粒特性。 |
材料选择 | 由于烧结行为的不同,基础材料会影响孔隙率。 | 有些材料更容易烧结,因此致密性更好,孔隙率更低。 | 根据应用和所需的机械性能选择材料。 |
准备好优化您的粉末冶金工艺了吗? 立即联系我们的专家 获取量身定制的解决方案!