热蒸发是一种广泛使用的物理气相沉积(PVD)技术,尤其适用于沉积低熔点金属。虽然这种技术简单而稳定,但也存在一些缺点。这些缺点包括材料兼容性有限、污染风险、薄膜均匀性差以及控制薄膜成分方面的挑战。此外,热蒸发不太适合高温材料,舟裂和热冲击等问题也会影响工艺。尽管热蒸发在有机发光二极管和薄膜晶体管等应用中非常有用,但这些缺点使其不太适合某些先进材料的沉积。
要点说明:
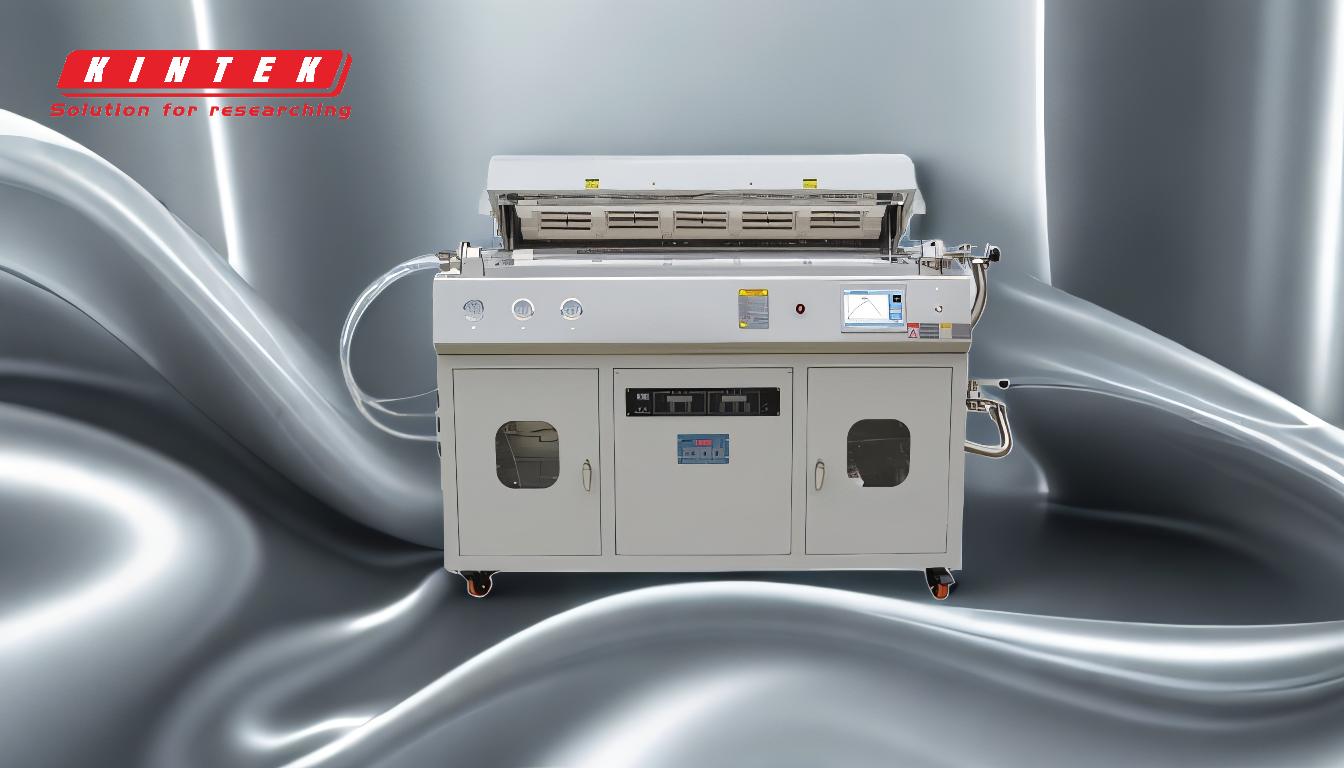
-
有限的材料兼容性
- 热蒸发主要适用于熔点相对较低的材料。难熔金属或需要很高温度的材料与这种方法不兼容。这一局限性限制了它在先进材料沉积中的应用。
- 该工艺依赖于熔化源材料,因此不适合在高温下分解或反应的材料。
-
高污染风险
- 坩埚或蒸发舟的污染是热蒸发过程中的一个重要问题。在高温下,坩埚舟和蒸发材料之间会发生合金化,从而导致沉积膜中出现杂质。
- 一旦蒸发舟因热应力或合金化而开裂,就必须将其丢弃,从而增加运行成本和停机时间。
-
薄膜均匀性差
- 如果没有行星基片支架或掩膜等额外设备,要实现均匀的薄膜厚度是一项挑战。这种限制会影响沉积薄膜的质量和一致性。
- 粗糙的基底表面会加剧不均匀性,导致薄膜特性不一致。
-
难以控制薄膜成分
- 与溅射等其他 PVD 方法相比,热蒸发对薄膜成分的控制能力较弱。这一限制对于需要精确化学计量的应用尤为重要。
- 蒸发过程中源材料的还原或分解会使成分控制更加复杂。
-
无法进行原位清洁
- 热蒸发无法对基底表面进行原位清洁,这会导致附着力差和沉积薄膜中的杂质增加。
-
阶跃覆盖的挑战
- 与其他 PVD 技术相比,热蒸发技术更难提高阶跃覆盖率,尤其是在复杂或不平整的表面上。
-
电子束蒸发中的 X 射线损伤
- 电子束蒸发是热蒸发的一种变体,在使用电子束蒸发时,基底或周围元件有可能受到 X 射线损坏。
-
热冲击和舟裂
- 快速加热和冷却循环会造成热冲击,从而导致艇体开裂。因此,有必要对功率斜坡进行仔细调节,以确保加热均匀并防止损坏。
-
可扩展性限制
- 与其他 PVD 方法相比,热蒸发的可扩展性较差,因此不太适合大规模工业应用。
-
低密度薄膜质量
- 通过热蒸发沉积的薄膜往往密度较低,但通过离子辅助技术可以提高密度。
-
适度的薄膜应力
- 生产出的薄膜通常具有中等应力,这会影响其机械性能和与基底的粘附性。
-
操作挑战
- 如何平衡艇或袋中的材料量与断裂、爆炸或有害反应的风险,是一项长期的挑战。
总之,虽然热蒸发在某些应用中是一种简单有效的方法,但其缺点,如污染风险、均匀性差和材料兼容性有限,使其不太适合高级或高精度沉积。有关热蒸发的更多详情,请浏览 热蒸发 .
总表:
缺点 | 描述 |
---|---|
有限的材料兼容性 | 仅适用于低熔点材料;与难熔金属不相容。 |
高污染风险 | 合金化和舟裂导致杂质和运营成本增加。 |
薄膜均匀性差 | 需要额外的设备才能达到均匀的厚度;粗糙的基底会使问题更加严重。 |
成分控制困难 | 与其他 PVD 方法相比,化学计量不够精确。 |
无法进行原位清洁 | 无法清洁基底,导致附着力差和杂质。 |
阶梯式覆盖的挑战 | 在复杂或不平整的表面上性能不佳。 |
X 射线损坏(电子束) | 基底或元件有受到 X 射线损坏的风险。 |
热冲击和舟裂 | 快速加热/冷却会导致艇体开裂,因此需要谨慎调整功率。 |
可扩展性限制 | 不太适合大规模工业应用。 |
低密度薄膜质量 | 薄膜密度较低;离子辅助技术可改善薄膜质量。 |
薄膜应力适中 | 薄膜表现出中等应力,影响机械性能和附着力。 |
运营挑战 | 在材料数量与断裂或爆炸风险之间取得平衡非常困难。 |
您需要更好的物料沉积解决方案吗? 立即联系我们的专家 探索先进的 PVD 替代技术!