物理气相沉积(PVD)是现代制造业中的一项关键工艺,尤其适用于在基底上形成薄膜和涂层。出于多种原因,在真空环境中进行 PVD 至关重要,其中包括减少污染、增加颗粒的平均自由路径以及实现对沉积过程的精确控制。真空可最大限度地减少不良原子和分子的存在,确保高质量涂层所需的清洁和受控环境。此外,真空还能实现高效的材料转移和附着,这对微电子、光学和其他先进技术的应用至关重要。
要点说明
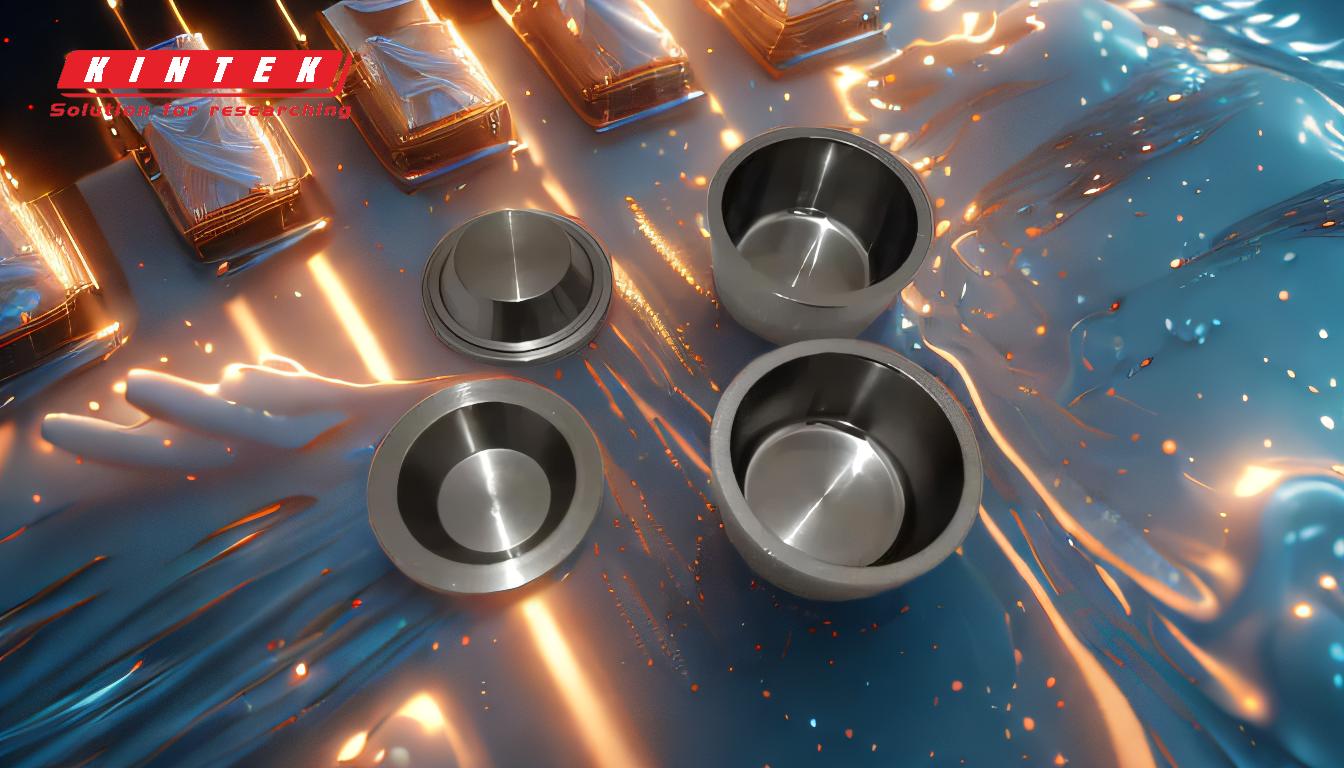
-
降低粒子密度,增加平均自由路径:
- 在真空环境中,气体分子的密度大大降低。这种降低增加了粒子的平均自由路径,即一个粒子在与另一个粒子碰撞之前的平均移动距离。较长的平均自由路径可确保气化材料直接到达基底,而不会因与气体分子碰撞而分散或减慢速度。这种直接路径对于获得均匀和高质量的涂层至关重要。
-
尽量减少污染:
- 真空环境可减少氧、氮和水蒸气等不良原子和分子对沉积薄膜的污染。污染物会降低涂层的质量,导致缺陷、附着力降低和性能受损。通过保持高真空度,该工艺可确保更清洁、更可控的环境,这对于微芯片制造等应用尤为重要,因为在这些应用中,即使是微小的污染物也会造成严重问题。
-
受控气体和蒸汽成分:
- 真空可精确控制加工室内的气体和蒸汽成分。这种控制对于调整沉积薄膜的特性(如厚度、均匀性和化学成分)至关重要。通过调整压力和气体成分,制造商可以获得不同应用所需的特定材料特性,如光学镀膜、耐磨层或导电膜。
-
高热蒸发率:
- 在真空中,材料的热蒸发率明显高于大气条件。这是因为压力的降低降低了材料的沸点,使其能够在较低的温度下蒸发。高蒸发率可确保高效的材料转移和沉积,这对于在合理的时间内获得所需的薄膜厚度和质量至关重要。
-
增强材料粘性:
- 真空环境中没有空气或其他流体,因此气化材料到达基底的能量更大。能量的增加会增强材料与基体的附着力,从而形成更坚固、更耐用的涂层。对于涂层需要承受机械应力、热循环或腐蚀环境的应用来说,提高附着力尤为重要。
-
可重复、可控的沉积工艺:
- 真空环境可提供稳定且可重复的工艺,这对工业应用至关重要。通过保持稳定的压力和温度条件,制造商可以获得具有可预测特性的均匀涂层。这种可重复性对于大规模生产至关重要,因为在大规模生产中,一致性和质量控制是最重要的。
-
低压等离子体环境:
- 真空有利于创造低压等离子体环境,这种环境通常用于溅射等 PVD 工艺。等离子体可增强气化材料的电离,提高颗粒沉积到基底上时的能量和方向性。从而提高薄膜密度、附着力和整体质量。
-
具体应用要求:
- 某些应用,如微型芯片、CD 和 DVD 的生产,需要极其洁净和受控的环境。高真空可确保去除最小的颗粒,防止出现可能影响最终产品功能的缺陷。这种洁净度在大气条件下是无法达到的。
总之,在真空环境中进行 PVD 对获得高质量、均匀和无污染的涂层至关重要。真空为高效的材料传输、受控沉积和增强附着力提供了必要条件,因此在广泛的工业和技术应用中不可或缺。
总表:
主要优势 | 说明 |
---|---|
减少污染 | 最大限度地减少不需要的原子/分子,确保涂层更清洁、质量更高。 |
增加平均自由路径 | 增强粒子移动距离,实现均匀、精确的沉积。 |
受控气体成分 | 可定制薄膜特性,如厚度、均匀性和化学成分。 |
高热蒸发率 | 可实现高效的材料传输和更快的沉积。 |
增强粘合力 | 提高涂层强度和耐久性,满足苛刻的应用要求。 |
可重复流程 | 确保批量生产结果的一致性和可预测性。 |
低压等离子体环境 | 通过增强电离,提高薄膜密度和质量。 |
特定应用的清洁度 | 符合微电子和光学等行业的严格要求。 |
需要真空 PVD 解决方案来满足您的制造需求? 立即联系我们 了解更多信息!