类金刚石涂层 (DLC) 采用先进的沉积技术,主要是物理气相沉积 (PVD) 和化学气相沉积 (CVD)。这些方法是在工具或部件表面形成一层薄而耐用的类金刚石碳 (DLC)。PVD 包括蒸发源材料,使其凝结在工具上,形成通常 0.5 至 2.5 微米厚的单层 DLC。而 CVD 则是在一个腔室中使用氢气和甲烷气体,将钨丝加热到 2300 摄氏度以上,分解气体,使碳原子重新结合,在工具表面形成纯金刚石薄膜。这两种方法都需要精确控制温度、压力和气体成分,以达到最佳效果。
要点说明:
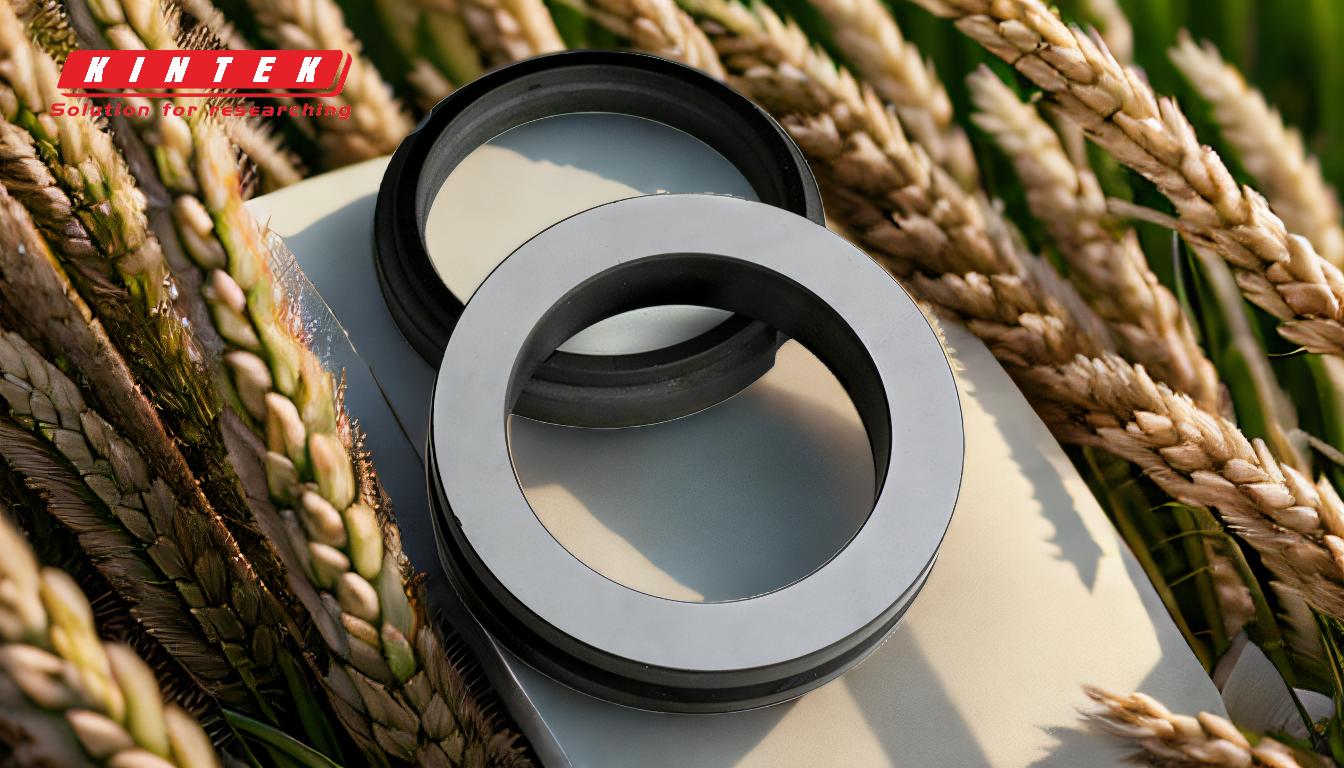
-
类金刚石涂层(DLC)概述:
- DLC 涂层是涂在工具或部件上的薄而坚硬的耐磨层,用于提高工具或部件的性能和使用寿命。
- 这些涂层是无定形的,也就是说它们没有晶体结构,但却具有与金刚石类似的特性,如高硬度和低摩擦。
-
主要涂层方法:
-
物理气相沉积(PVD):
- PVD 是应用 DLC 涂层的一种广泛方法。
- 该工艺包括在真空室中蒸发源材料(通常为碳基)。
- 蒸发后的材料凝结在工具表面,形成一层薄而均匀的 DLC 涂层。
- 涂层厚度通常在 0.5 至 2.5 微米之间。
- PVD 因其能够生产出具有出色耐磨性的高质量附着涂层而闻名。
-
化学气相沉积(CVD):
- CVD 是应用 DLC 涂层的另一种常见方法。
- 在这一工艺中,工具被放置在充满氢气和甲烷气体的腔室中。
- 加热到 2300°C 以上的钨丝为分解气体分子提供了所需的能量。
- 然后,活性碳原子在工具表面重新结合,形成纯净的金刚石薄膜。
- CVD 尤其适用于制造更厚、更耐用的涂层。
-
物理气相沉积(PVD):
-
应用 DLC 涂层的工艺步骤:
-
准备:
- 要涂覆的工具或部件必须彻底清洁和准备,以确保涂层的正确附着。
- 这通常包括通过化学或机械方法去除任何表面污染物,如油或氧化物。
-
装入沉积室:
- 将准备好的工具装入沉积室。
- 在 PVD 技术中,沉积室被抽空以形成真空;而在 CVD 技术中,沉积室充满了适当的气体。
-
沉积:
- 对于 PVD,源材料被蒸发,蒸汽凝结在工具表面。
- 对于 CVD,气体被激活,碳原子沉积到工具上。
-
冷却和抛光:
- 沉积完成后,让涂层工具缓慢冷却,以防止产生热应力。
- 对最终涂层的质量、厚度和附着力进行检查。
-
准备:
-
关键参数和注意事项:
-
温度:
- PVD 和 CVD 工艺都需要很高的温度,通常从 750°C 到超过 2,300°C 不等,具体取决于哪种方法。
- 适当的温度控制对确保涂层的质量和附着力至关重要。
-
气体成分:
- 在 CVD 过程中,必须仔细控制氢气和甲烷气体的成分,以达到理想的碳沉积效果。
-
涂层厚度:
- DLC 涂层的厚度是决定其性能的关键因素。
- 较厚的涂层可能具有更好的耐磨性,但也可能更容易开裂或分层。
-
附着力:
- 确保涂层与底层之间有很强的附着力对涂层的耐久性至关重要。
- 这通常需要对基材进行预处理或使用中间层。
-
温度:
-
DLC 涂层的应用:
- DLC 涂层广泛应用于汽车、航空航天、医疗设备和切削工具等行业。
- 它们具有减少摩擦、抗磨损和延长恶劣条件下部件寿命的能力,因此尤其受到重视。
-
优点和局限性:
-
优点
- 硬度高,耐磨性强。
- 摩擦系数低,降低能耗,提高效率。
- 优异的耐腐蚀性。
- 可涂覆复杂几何形状。
-
局限性:
- 设备和工艺成本高。
- 由于可能产生内应力和裂纹,厚度有限。
- 需要精确控制工艺参数。
-
优点
-
未来趋势:
- 目前的研究重点是提高 DLC 涂层的附着力、厚度和均匀性。
- 纳米技术和混合涂层方法的进步有望进一步提高类金刚石涂层的性能和在各行各业的适用性。
通过了解这些关键点,设备和耗材采购人员可以就类金刚石涂层的应用做出明智的决定,确保他们选择最适合其特定需求的方法和参数。
汇总表:
方面 | 详细信息 |
---|---|
主要方法 | PVD(物理气相沉积)、CVD(化学气相沉积) |
涂层厚度 | 0.5 至 2.5 微米(PVD),CVD 更厚 |
关键参数 | 温度(750°C 至 2300°C)、气体成分、附着力、涂层厚度 |
应用领域 | 汽车、航空航天、医疗设备、切削工具 |
优点 | 高硬度、低摩擦、耐腐蚀、几何形状复杂 |
局限性 | 成本高、厚度有限、需要精确的参数控制 |
使用先进的 DLC 涂层优化您的工具 今天就联系我们的专家 获取量身定制的解决方案!