直流和射频磁控溅射是薄膜沉积中广泛使用的两种技术,各有不同的特点、优势和应用。直流溅射使用直流电源,主要适用于导电材料,沉积率高,成本效益高,适用于大型基底。另一方面,射频溅射采用交流电源,频率通常为 13.56 MHz,因此既适用于导电材料,也适用于非导电材料,尤其是电介质靶材。虽然射频溅射的沉积率较低,运行成本较高,但它可以避免电荷积累和电弧等问题,而直流溅射在使用非导电材料时,电荷积累和电弧是常见的问题。这两种方法都利用磁场来提高等离子体的生成和沉积效率,但它们在电源和材料兼容性方面的差异使其适用于不同的应用。
要点说明:
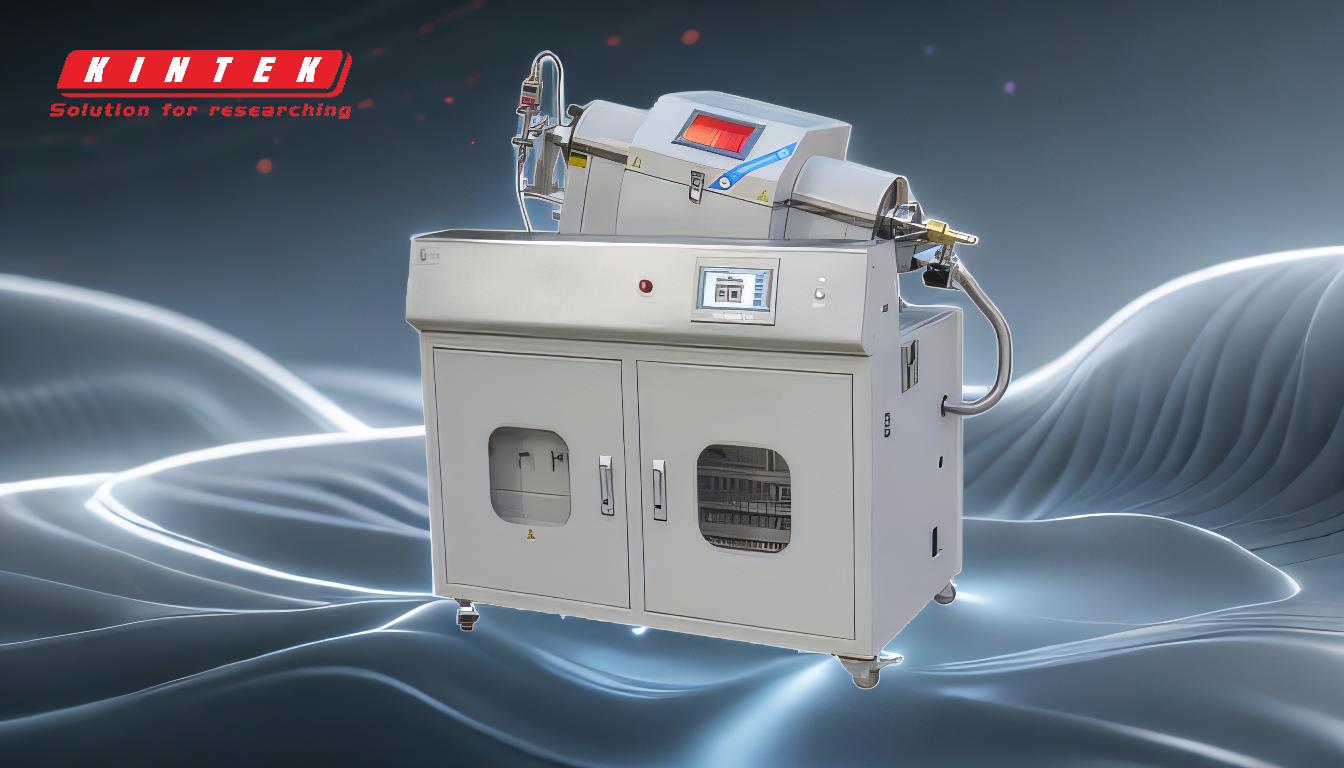
-
电源和等离子体生成:
- 直流磁控溅射:使用直流电源在低压气体环境中产生等离子体。带正电荷的气体离子被加速冲向带负电荷的靶材,导致靶材溅射。
- 射频磁控溅射:利用交流电源(通常为 13.56 MHz)产生等离子体。交变电荷可防止目标上的电荷积累,因此既适用于导电材料,也适用于非导电材料。
-
材料兼容性:
- 直流磁控溅射:最适合纯金属(如铁、铜、镍)等导电材料。由于电荷积累和电弧问题,它不是电介质材料的理想选择。
- 射频磁控溅射:适用于导电和非导电材料,尤其是介质目标。交变电荷可防止电荷积聚,因此对绝缘材料非常有效。
-
沉积率和效率:
- 直流磁控溅射:沉积率高,可高效地用于大型基底和工业应用。对于导电材料而言,它具有较高的成本效益。
- 射频磁控溅射:与直流溅射相比,沉积率较低。不过,它能为较小的基底和复杂的材料提供更好的控制和均匀性。
-
运行成本和应用:
- 直流磁控溅射:操作成本低,设置简单,是大规模生产导电薄膜的理想选择。它广泛应用于要求高产量的行业。
- 射频磁控溅射:由于射频电源的复杂性,运行成本较高。对于需要精确控制薄膜特性的应用,如半导体和光学镀膜,它是首选。
-
电荷累积和电弧:
- 直流磁控溅射:与电介质材料一起使用时容易产生电荷积累和电弧,从而损坏电源和薄膜。
- 射频磁控溅射:交变电荷可防止电荷积累,消除电弧问题,适用于电介质材料。
-
磁场利用:
- 直流和射频磁控溅射都利用磁场在靶材表面附近捕获电子,从而提高等离子体的生成和沉积效率。这种磁束缚可在较低气体压力下产生较大电流,从而改善整个沉积过程。
-
薄膜质量和控制:
- 直流磁控溅射:生产的薄膜纯度高、致密性好、厚度均匀,尤其适用于导电材料。对于大面积基板而言,易于实现工业化生产。
- 射频磁控溅射:能更好地控制薄膜特性,如颗粒大小和均匀性,因此适合高精度应用。它是沉积合金和氧化物等复杂材料的理想选择。
总之,选择直流还是射频磁控溅射取决于应用的具体要求,包括要沉积的材料类型、所需的沉积速率和薄膜质量。对于导电材料而言,直流溅射更具成本效益和效率,而射频溅射则为导电和非导电材料提供了更大的灵活性和控制,尽管成本较高。
汇总表:
特征 | 直流磁控溅射 | 射频磁控溅射 |
---|---|---|
电源 | 直流电 (DC) | 13.56 MHz 交流电 (AC) |
材料兼容性 | 最适合导电材料(如金属) | 适用于导电和非导电材料(如电介质) |
沉积速率 | 沉积速率高,适合大型基底 | 沉积率较低,更适合较小基底和复杂材料 |
运行成本 | 成本更低,设置更简单 | 射频电源复杂,成本较高 |
电荷积累 | 使用非导电材料时容易产生电荷积聚和电弧 | 防止电荷积聚,无电弧问题 |
应用 | 大规模生产导电薄膜 | 高精度应用,如半导体和光学镀膜 |
薄膜质量 | 高纯度、厚度均匀的导电材料 | 更好地控制薄膜特性,是合金和氧化物的理想选择 |
还不确定哪种溅射方法适合您的应用? 立即联系我们的专家 获取个性化指导!