气相沉积生长是一种通过气相沉积材料在基材上形成薄膜或涂层的过程。该技术广泛应用于半导体、光学、防护涂层等行业。该工艺大致可分为两种主要类型:化学气相沉积(CVD)和物理气相沉积(PVD)。 CVD 涉及产生气相的化学反应,而 PVD 则依赖于蒸发或溅射等物理过程。两种方法都有不同的步骤和机制,但它们有一个共同的目标:创造高质量、均匀且粘附的薄膜。 CVD 和 PVD 之间的选择取决于具体应用、所需的薄膜特性以及所涉及的材料。
要点解释:
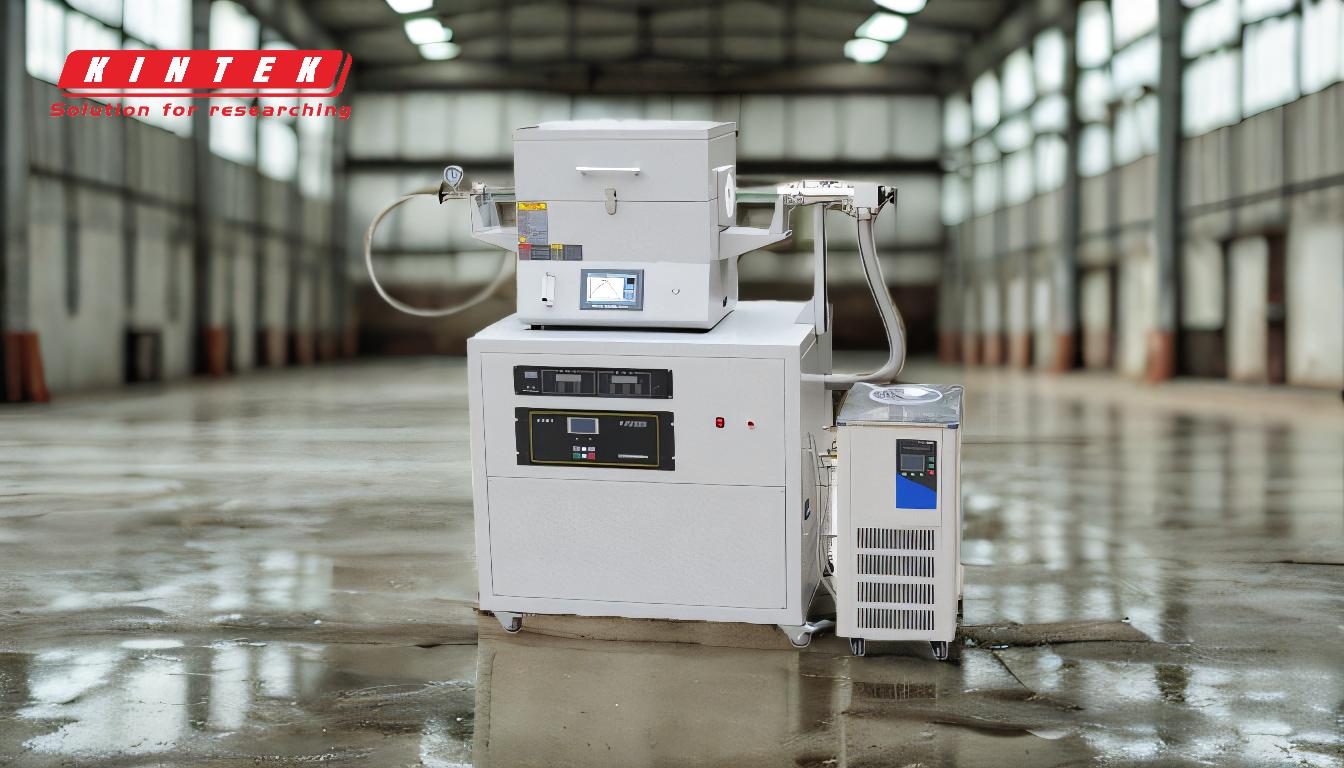
-
化学气相沉积 (CVD):
- 流程概述: CVD 涉及使用挥发性前体进行化学反应,在基材上形成固体材料。该过程通常发生在高温高压的受控环境中。
-
涉及步骤:
- 反应气体的传输: 气态物质被输送至基材表面。
- 吸附: 气体吸附到基材表面上。
- 表面反应: 在热量或等离子体的促进下,表面发生化学反应,从而形成所需的薄膜。
- 成核和生长: 当反应产物积聚在基材上时,薄膜成核并生长。
- 解吸和去除: 反应的副产物被解吸并从室中除去。
- 优点: CVD 生产的薄膜具有化学计量、致密且高质量。通过调节沉积时间和功率可以精确控制薄膜厚度。
-
物理气相沉积 (PVD):
- 流程概述: PVD 涉及材料从源到基材的物理转移。这是通过蒸发或溅射等工艺实现的。
-
涉及步骤:
- 蒸发: 源材料被加热或用高能离子轰击,使其蒸发。
- 运输: 汽化的原子穿过真空室到达基板。
- 反应: 在反应性 PVD 中,汽化的原子可能与引入腔室中的气体发生反应,形成氧化物、氮化物或碳化物等化合物。
- 沉积: 原子或化合物沉积在基板上,形成薄膜。
- 优点: PVD 允许沉积多种材料,包括金属、合金和陶瓷。该过程在真空下进行,最大限度地减少污染并产生高纯度的薄膜。
-
热气相沉积:
- 流程概述: 这是 PVD 的一个子集,其中源材料被加热以产生蒸气,然后蒸气在基材上凝结。
- 温度范围: 通常,源材料被加热至 250 至 350 摄氏度之间的温度。
- 应用: 该方法对于在相对较低温度下容易汽化的材料特别有用。
-
气溶胶沉积:
- 流程概述: 在这种方法中,细小的陶瓷颗粒被加速到高速并与基材碰撞,形成致密的涂层。
- 优点: 该工艺不需要额外的热处理,因此节能且适用于温度敏感的基材。
-
溅射:
- 流程概述: 溅射涉及用高能离子轰击靶材料,导致原子喷射并沉积到基材上。
- 优点: 这种方法用途广泛,可用于沉积多种材料,包括金属、半导体和绝缘体。
-
CVD与PVD的比较:
- 化学气相沉积: 更适合生产高质量、化学计量的薄膜,并精确控制厚度。然而,它通常需要更高的温度和更复杂的设备。
- 物理气相沉积: 就可沉积的材料而言更加通用,并且通常在较低的温度下运行。它也更适合沉积纯金属和合金。
总之,气相沉积生长过程是现代制造和材料科学的关键技术。无论是使用 CVD 还是 PVD,制造薄而均匀的高质量薄膜的能力对于从电子产品到保护涂层的广泛应用至关重要。了解每种方法的具体步骤和优点可以为给定应用选择最合适的技术。
汇总表:
方法 | 流程概览 | 优点 |
---|---|---|
化学气相沉积 (CVD) | 利用化学反应在基材上形成固体薄膜。需要高温和高压。 | 生产具有精确厚度控制的化学计量、致密且高质量的薄膜。 |
物理气相沉积 (PVD) | 依靠蒸发或溅射等物理过程将材料转移到基材上。 | 多才多艺的;在真空下沉积金属、合金和陶瓷,污染最小。 |
热气相沉积 | PVD 的子集;加热源材料产生蒸气,蒸气在基材上凝结。 | 非常适合在低温 (250–350°C) 下汽化的材料。 |
气溶胶沉积 | 加速细陶瓷颗粒形成致密涂层,无需热处理。 | 节能且适用于温度敏感基材。 |
溅射 | 用高能离子轰击目标材料,喷射原子进行沉积。 | 用途广泛;沉积金属、半导体和绝缘体。 |
发现最适合您的应用的气相沉积方法 - 立即联系我们的专家 !