磁控溅射简介
磁控溅射概述
磁控溅射是一种复杂的薄膜制备技术,包括在真空环境中将原子或分子从目标材料中喷射出来。然后将这些喷射出的粒子沉积到基底上,形成薄膜。根据所用电源的频率,该工艺可大致分为三大类:直流溅射、中频(MF)溅射和射频(RF)溅射。
磁控溅射背后的基本概念相对简单,但其基本机制却相当复杂。与基本的二极管或直流溅射系统相比,磁控溅射的一个主要特点是在靶区附近引入强磁场。该磁场通过使电子沿磁通线螺旋运动,从而将等离子体限制在非常靠近靶材的区域内,在此过程中发挥了至关重要的作用。这种限制可防止等离子体损坏基底上正在形成的薄膜。
在典型的磁控溅射装置中,首先要将腔室抽真空至高真空,以尽量减少背景气体和潜在污染物。随后,形成等离子体的溅射气体被引入腔室,压力被调节到毫托范围。溅射气体与目标材料相互作用产生的等离子体会导致目标表面被高能离子侵蚀。这些释放出的原子穿过真空,沉积在基底上,形成所需的薄膜。
在磁控溅射中加入磁场不仅能提高工艺的效率,还能使薄膜沉积更加可控和均匀。这使得磁控溅射成为要求高质量、均匀和致密薄膜应用的首选方法。
溅射技术类型
直流溅射
直流溅射是薄膜物理气相沉积(PVD)涂层工艺的基础技术。它采用直流 (DC) 电源电离目标材料,从而在其表面产生等离子体。这种等离子体至关重要,因为它有利于离子加速,然后轰击目标材料。这种高能轰击会导致原子或分子从目标材料中释放出来,然后凝结在附近的基底上形成薄膜。
直流溅射的突出特点之一是简单、成本效益高,因此是基本薄膜制备和对精确沉积速率控制要求不高的应用的理想选择。这种技术在各行各业都得到了广泛应用,包括用于微芯片电路的半导体行业,以及珠宝和手表镀金等装饰性应用。此外,直流溅射还可用于在玻璃和光学元件上制作非反射涂层,以及生产金属化包装塑料。
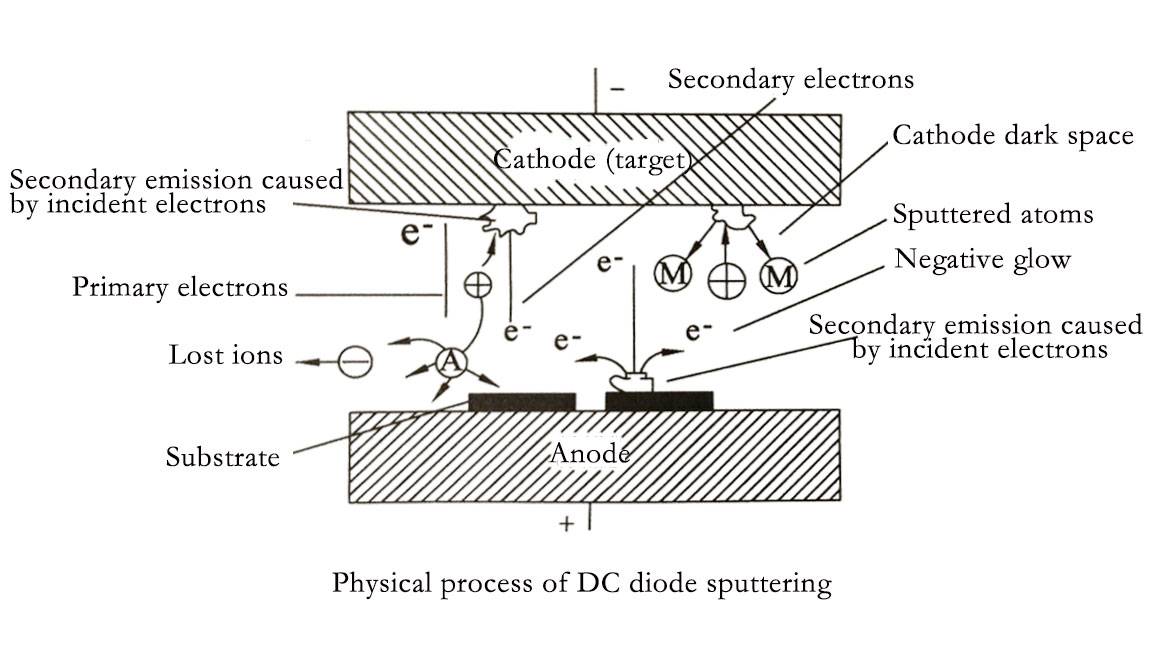
直流溅射工艺首先是在低压气体环境(通常是氩气)中对金属靶施加电压。气体离子与靶材碰撞后,会喷射出靶材的微小颗粒,然后沉积到基底上。这种方法确保了金属沉积的直接性和经济性,尤其适用于导电目标材料的涂层。
总之,直流溅射是一种多功能的、易于使用的薄膜沉积方法,它兼具简便性、成本效益和在不同行业的广泛适用性。
中频溅射
中频溅射利用频率通常在 50 kHz 至 5 MHz 之间的电源来产生稳定的等离子体环境。之所以战略性地选择这一频率范围,是因为它可以实现离子和电子动力学之间的平衡,确保离子仍能跟随交变磁场,而电子则对等离子体密度做出贡献。因此,与直流溅射相比,等离子体具有更高的离子轰击能量,从而实现更可控、更均匀的沉积率。
在中频溅射中,交变磁场可同时加速离子和电子,但由于离子的电荷质量比较小,因此在频率超过约 50 kHz 时开始出现滞后。这种滞后是有益的,因为它能增强离子对目标的轰击,从而更有效地释放原子或分子。另一方面,电子在等离子体内振荡,增加了与氩原子的碰撞频率,从而提高了等离子体速率。等离子体速率的提高可以降低工作压力,通常在 10^-1 到 10^-2 Pa 之间,同时保持较高的溅射速率。

中频溅射的低压环境有利于形成具有独特微观结构的薄膜,这是在较高压力下无法实现的。这种方法对于制备具有高沉积率、优异的均匀性和最小内应力等特性的高质量薄膜尤为有利。这些特性使中频溅射成为光学薄膜、磁性薄膜和透明导电薄膜等对精度和均匀性要求极高的应用领域的理想选择。
参数 | 中频溅射 |
---|---|
电源频率 | 50 千赫 - 5 兆赫 |
离子轰击能量 | 高于直流溅射 |
沉积速率 | 更稳定、更均匀 |
工作压力 | 10^-1 至 10^-2 Pa |
应用 | 光学薄膜、磁性薄膜、透明导电薄膜 |
射频溅射
射频溅射(RF Sputtering)是一种复杂的技术,它采用射频电源(通常工作频率为 13.56 MHz)来创造稳定的等离子体环境。这种方法特别适用于沉积本身不导电的绝缘材料。该工艺涉及以无线电频率交变电势,通过防止电荷积聚来有效 "清洁 "目标材料表面。在正循环期间,电子被吸引到靶材上,使其产生负偏压,而在负循环期间,离子轰击有增无减。
这种技术可确保靶材不产生电荷积聚,这对保持沉积薄膜的均匀性和密度至关重要。在需要对绝缘材料进行镀膜而又不影响薄膜质量的环境中,使用射频溅射技术大有裨益。由于能够精确控制等离子体和离子轰击能量,薄膜不仅均匀,而且密度极高,因此射频溅射非常适合需要高质量和高均匀性薄膜的应用。
射频溅射从 20 世纪 60 年代开始应用,早期应用包括美国 BM 公司在硅基板上沉积 SiO₂ 薄膜。这一领域的历史和技术进步凸显了其在生产高性能薄膜(如金属膜、合金膜、压电薄膜、铁电薄膜和高温超导薄膜)方面的可靠性和有效性。
不同溅射方法的应用和特点
直流溅射应用
直流溅射是一种多用途技术,可为各种工业应用量身定制具有特定性能的薄膜。这些薄膜通常呈现出非晶或微晶晶体结构,从而形成了独特的机械和化学特性。
直流溅射薄膜的突出特点之一是内应力高。这种特性使其特别适用于耐磨涂层,因为耐久性和抗机械磨损性是最重要的。例如,在半导体行业中,直流溅射被用于在分子水平上创建微芯片电路,以确保薄膜能够经受住生产和操作的严格考验。
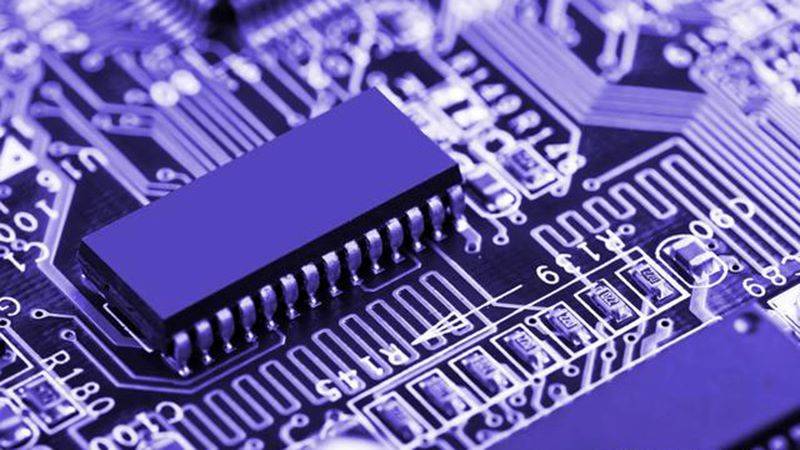
除了耐磨性,直流溅射还擅长生产抗氧化薄膜。这些薄膜在材料暴露于氧化条件的环境中至关重要,例如在某些化学加工或高温应用中。制作具有特定微观结构的表面薄膜的能力进一步提高了其实用性,使其成为一系列表面工程应用的理想选择。
直流溅射不仅限于工业用途,还可应用于消费品领域。例如,它可用于珠宝、手表和其他装饰品的金溅射涂层,使其表面光亮,既耐用又美观。同样,玻璃和光学元件上的非反射涂层也是直流溅射技术的另一个应用领域,它能增强这些产品的功能和性能。
此外,直流溅射还可用于制造金属化包装塑料,这对于食品包装和其他需要防潮防气的应用至关重要。利用直流电源控制和优化沉积过程的能力,使其成为这些应用中经济、可靠的选择。
总之,直流溅射能够生产出具有可控内应力、定制微结构和特定机械性能的薄膜,这使其成为从半导体到消费品等多个行业的重要工具。
中频溅射应用
中频溅射的突出特点是能够生产出具有高沉积率、优异的均匀性和最小内应力的高质量薄膜。这种技术尤其适用于各种先进的薄膜应用,包括光学薄膜、磁性薄膜和透明导电薄膜。
中频溅射的主要优势之一是能够处理需要精确控制沉积过程的材料。例如,光学薄膜要求高度均匀和低内应力,以确保透镜和反射镜等设备的最佳性能。用于数据存储和磁性传感器的磁性薄膜得益于高沉积率和低应力,这有助于提高其耐用性和性能。同样,在触摸屏和太阳能电池中必不可少的透明导电薄膜也需要高透明度和导电性,而中频溅射可以有效地实现这一点。
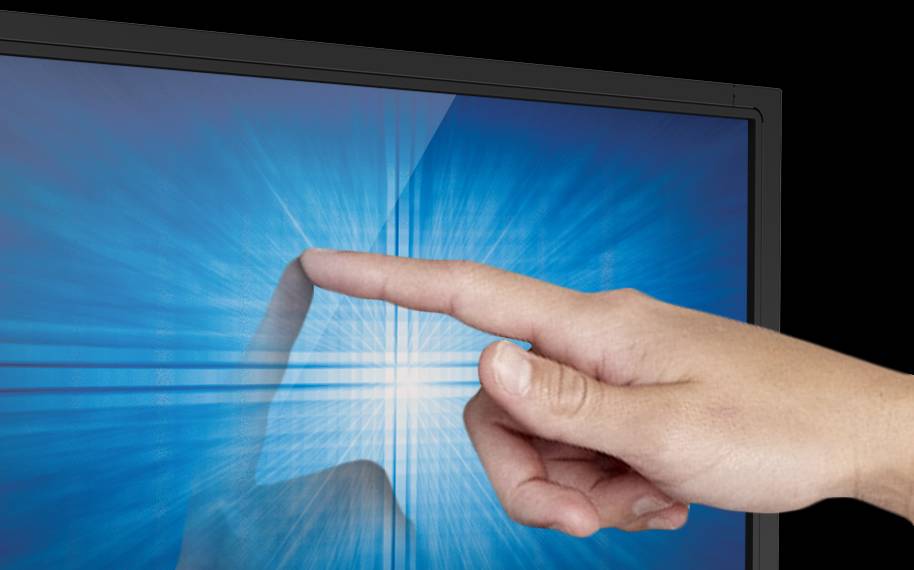
在溅射中使用中频功率可以获得稳定的等离子体环境,提高离子轰击能量,使薄膜沉积更可控、更均匀。这种稳定性对于制备必须满足严格性能标准的薄膜至关重要,使中频溅射成为生产先进薄膜不可或缺的工具。
射频溅射应用
射频溅射由于能够生产高密度、高均匀度的薄膜,已成为各种高科技行业不可或缺的多功能技术。这种方法尤其适用于制作高质量、高性能的薄膜,如金属膜、合金膜、压电薄膜、铁电薄膜和高温超导薄膜。射频溅射的独特优势,如较低的腔体压力和使用射频电源,使其非常适合处理具有绝缘性能的目标材料,而这些材料往往是直流溅射等替代方法所难以处理的。
射频溅射技术最重要的进步之一是应用于高绝缘氧化物的沉积。这些氧化物包括氧化铝、氧化钽和氧化硅,对于提高计算机和半导体行业微芯片电路的性能至关重要。通过仔细控制沉积过程,射频溅射可确保这些绝缘层均匀地涂敷在金属目标表面之间,从而提高设备的整体效率和可靠性。
受薄膜设备小型化需求不断增长和纳米技术应用不断进步的推动,射频溅射薄膜的需求预计将在未来几年内激增。这种增长不仅限于半导体领域,还扩展到能源、光电子、生命科学、机械和化学工业等多个领域。射频溅射的适应性和精确性使其成为广泛应用的首选技术,巩固了其在现代制造工艺中的基石技术地位。
联系我们获取免费咨询
KINTEK LAB SOLUTION 的产品和服务得到了世界各地客户的认可。我们的员工将竭诚为您服务。如需免费咨询,请与我们的产品专家联系,以找到最适合您应用需求的解决方案!