PVD 涂层工艺的基本原理
蒸发
在真空环境中,被称为靶材的固体材料通过各种方法(主要是加热)转变为气态。这一过程称为蒸发,是物理气相沉积(PVD)镀膜工艺的基础。有几种技术可用于实现这种转化:
-
热蒸发:这种方法是使用电阻或其他加热元件将目标材料加热到其蒸发温度。一旦材料达到蒸发点,就会变成气体,然后在基底上扩散和凝结,形成薄膜。
-
电子束蒸发:将高能电子束射向目标材料,使其蒸发。这种技术特别适用于熔点较高的材料,因为局部加热效应可以精确控制蒸发过程。
-
激光蒸发:这种方法利用高能激光脉冲使目标材料蒸发。激光蒸发法在制备复杂薄膜材料方面具有优势,因为它精度高,可用于蒸发传统方法难以处理的材料。
每种方法都有其独特的优势,要根据涂层工艺的具体要求来选择,如所用材料的类型和所需薄膜的性能。
运输
气态材料转化为蒸汽状态后,会在真空室中进行扩散。这种扩散是 PVD 过程中的一个关键阶段,因为它直接影响到后续薄膜沉积的均匀性和质量。有几个关键因素会对这一扩散阶段产生重大影响:
-
气体压力:真空室内的压力起着关键作用。较低的压力通常会提高扩散效率,确保气态材料在基底上更均匀地扩散。反之,较高的压力会导致气体分子间的碰撞,从而可能降低整体扩散速度并影响薄膜的均匀性。
-
温度:真空环境中的温度是另一个关键变量。较高的温度可以加速扩散过程,但必须小心控制,以防止对基底造成热损伤或形成不均匀的沉积物。平衡温度与其他工艺参数对于实现最佳扩散效果至关重要。
-
基底位置:基底相对于气态材料源的空间布置也很重要。正确的排列可确保气态材料均匀地到达基底的所有区域,防止局部过度沉积或沉积不足。旋转或倾斜基底等技术有助于实现更均匀的覆盖。
总之,在真空中传输气体材料是一个微妙的过程,需要对气体压力、温度和基底定位进行细致的控制,以确保成功沉积出高质量的薄膜。
沉积
在沉积阶段,已输送到基底的气态材料开始冷却和凝结。这一冷却过程至关重要,因为它会将气体转化为固态薄膜,附着在基底表面。沉积过程不仅是一个物理变化过程,也是一个转换过程,它根据具体应用大大改变了基底的特性。
沉积过程中使用的气体类型对薄膜的最终结构和特性起着至关重要的作用。例如,氩气和氦气等惰性气体通常用于保持薄膜的纯度,确保不会发生不必要的化学反应。另一方面,引入氧气、氮气和氟气等活性气体可生成特定的化合物,如氧化物、氮化物和氟化物,从而增强薄膜在特定应用中的功能。
此外,沉积室中的气体压力也是影响沉积速度和薄膜质量的关键参数。较低的气体压力通常会产生更致密、更均匀的薄膜,而这正是许多应用所需要的。相反,较高的气体压力会导致较粗糙的薄膜,这在某些情况下可能是有益的,例如当需要增加表面积以获得更好的粘附性或反应性时。
总之,沉积过程是冷却、气体类型和压力之间复杂的相互作用,每个因素都经过精心控制,以达到所需的薄膜特性。这种精心的协调可确保生成的薄膜符合从电子到光学等各个行业所要求的严格标准。
PVD 工艺的主要类型
蒸发沉积
蒸发沉积是一种复杂的技术,通过将目标材料加热到其汽化点来生产薄膜。这种工艺对金属和某些合金特别有效,通过热能将它们从固态转化为气态。气化后的原子会凝结在基底上,形成均匀的保形薄膜。这种方法通常在高真空环境中进行,以尽量减少碰撞和污染,确保沉积薄膜的纯度和完整性。
蒸发沉积法的主要优势之一是能够生成具有极佳均匀性和保形性的高质量薄膜。这种技术用途广泛,能够沉积包括金属、陶瓷和半导体在内的多种材料。不过,该工艺需要高真空环境,对环境因素高度敏感,这可能会限制其在某些情况下的适用性。
溅射沉积
溅射沉积是一种复杂的物理气相沉积(PVD)技术,包括用高能粒子(通常是等离子体中的离子)轰击目标材料。这种轰击会使目标材料喷射出原子或分子,然后这些原子或分子穿过真空,凝结在基底上,形成薄膜。该工艺用途广泛,适用于金属、氧化物和氮化物等多种材料。
在溅射沉积过程中,目标材料暴露在通常由氩离子和电子组成的等离子体中。这些高能粒子 "击落 "目标材料上的原子,形成源原子云。原子云随后凝结在基底上,形成薄膜。靶材的选择和等离子体的条件对沉积薄膜的特性有很大影响。
溅射沉积的一个显著特点是重溅射现象,即已沉积的材料会在随后的离子或原子轰击中重新释放。这可能会影响薄膜的均匀性和厚度,因此需要仔细控制沉积参数,以获得理想的结果。
由于溅射沉积能生成高质量、致密且与基底附着力极佳的薄膜,因此被广泛应用于各行各业。溅射沉积尤其适用于多种材料,是制造先进的电子、光学和机械部件薄膜的多功能工具。
脉冲激光沉积(PLD)
脉冲激光沉积 (PLD) 是一种复杂的蒸发工艺,它利用高能激光脉冲在真空室中蒸发目标材料。这种方法尤其擅长制备复杂的薄膜材料,因此成为各种科学和工业应用的首选。
PLD 工艺开始时,激光束瞄准材料,使其汽化并形成一股等离子体。然后,等离子体沉积到基底上,在那里凝结成薄膜。这一过程非常复杂,涉及蒸发、烧蚀、等离子体形成和剥离,因此必须进行仔细的优化。尽管管理所涉及的众多变量需要花费更多的时间和精力,但脉冲激光沉积仍具有一些优势。
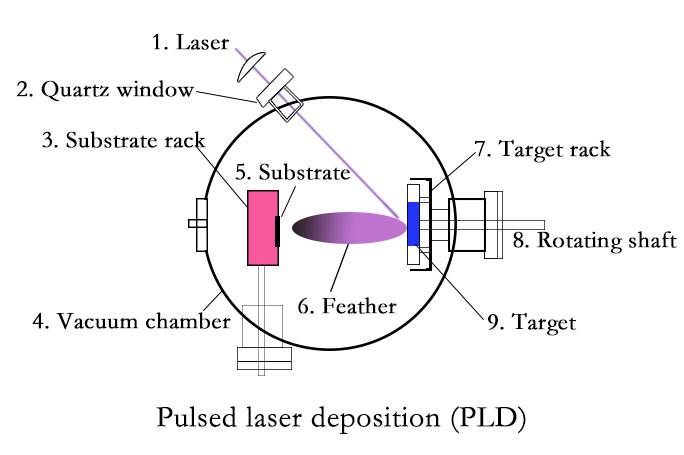
PLD 的主要优点之一是沉积率高,与其他方法相比,可大大简化工艺流程。此外,PLD 无需使用灯丝,从而简化了维护工作并减少了潜在的污染源。这使得 PLD 特别适合要求高精度和高纯度的应用,如电子和光学行业。
总之,虽然 PLD 的复杂性要求精细控制,但其高效生产高质量复杂薄膜的能力和最少的维护使其成为 PVD 涂层工艺领域的重要工具。
化学气相沉积(CVD)
虽然化学气相沉积 (CVD) 与物理气相沉积 (PVD) 有本质区别,但在某些情况下,这两种技术相结合可实现卓越的薄膜特性。CVD 是一种真空沉积方法,以生产高质量、高性能的固体材料而闻名,尤其是半导体行业使用的薄膜。该工艺将晶片(基底)暴露在一种或多种挥发性前驱体中,前驱体在基底表面发生反应和/或分解,形成所需的沉积物。这种方法用途广泛,能够沉积各种形式的材料,包括单晶、多晶、非晶和外延结构。
与依靠蒸发或溅射等物理过程的 PVD 相比,CVD 利用化学反应沉积材料。这种化学方法可以更好地控制沉积薄膜的成分和特性。不过,在某些应用中,CVD 和 PVD 的互补使用可以生成具有更强特性的薄膜,如更好的附着力、更好的机械性能或更均匀的涂层。例如,初步的 PVD 层可用于为后续的 CVD 层创造更容易接受的表面,从而优化整体薄膜质量。
在复杂的微加工过程中,CVD 与 PVD 的结合尤为有利,化学沉积技术与物理沉积技术的结合可以解决任何一种方法都无法单独应对的特定挑战。这种混合方法不仅扩大了可沉积材料的范围,还提高了最终产品的功能和性能。
气体在 PVD 过程中的应用
惰性气体
氩气(Ar)和氦气(He)等惰性气体作为载气在溅射沉积工艺中发挥着至关重要的作用。这些气体能够在不引起任何化学反应的情况下提高目标材料的溅射效率,因而备受青睐。这种非反应性确保了沉积薄膜的纯度,这对获得高质量涂层至关重要。
惰性气体的使用不仅限于溅射沉积,还可用于防止可能导致样品降解的不良化学反应。常见的不良反应包括氧化和水解,通常由空气中的氧气和湿气引发。用惰性气体代替这些活性元素,可以保持样品的完整性。
氩气是各种应用中最常用的惰性气体,因为其天然含量高且成本相对较低。氩气约占地球大气的 1%,因此很容易在工业中使用。虽然氩是最常用的惰性气体,但根据工艺的具体要求,也可以使用氦和氖等其他惰性气体。
值得注意的是,"惰性气体 "一词与上下文有关。虽然惰性气体通常被认为是惰性的,但它们在某些条件下会发生反应,尽管概率很低。这种特性主要是由于这些气体具有完整的价层,通常不会发生反应。不过,这并不是绝对规则,因为即使是惰性气体,在特定条件下也会形成化合物。
在规定惰性气体的纯度时,通常会以百万分之一(ppm)为单位标明污染水平。例如,污染水平为 100 ppm 意味着在每一百万个惰性气体分子中,有 100 个是外来分子。这一指标对于确保惰性气体有效保持沉积薄膜的纯度至关重要。
总之,氩气和氦气等惰性气体在溅射沉积和其他工艺中是不可或缺的,在这些工艺中,保持材料的纯度和完整性至关重要。它们的非反应性和可用性使其成为广泛工业应用的理想选择。
反应气体
反应气体在 PVD 过程中制备各种薄膜时起着至关重要的作用。这些气体包括氧气 (O₂)、氮气 (N₂) 和氟气 (F₂),分别是制备氧化物、氮化物和氟化物薄膜的关键。为了在沉积薄膜中获得所需的化学成分和性能,通常需要引入这些反应气体。
例如,在制备氧化铝(Al₂O₃)薄膜时,通常会引入氧气作为反应气体。这可确保气相中的铝原子与氧气发生反应,形成稳定、均匀的铝₂O₃薄膜。反应气体的使用并不局限于氧化铝,还可用于其他材料,如氮化硅 (Si₃N₄) 和二氧化钛 (TiO₂),在这两种材料中分别使用氮气和氧气。
反应气体的选择及其浓度会极大地影响薄膜的特性,包括密度、硬度和化学稳定性。例如,氧气浓度越高,薄膜的多孔性和致密性越差,而氧气浓度越低,则可能导致氧化不完全,从而影响薄膜的整体质量。
总之,合理使用反应气体是 PVD 工艺的一个关键环节,可以为各种应用制造出具有定制特性的高性能薄膜。
有机气体
在某些特殊应用中,乙烯和丙烯等有机气体对聚合物薄膜和复合材料的制备起着至关重要的作用。这些气体通常被引入 PVD 工艺,以促进特定薄膜结构的形成,而仅使用惰性气体或活性气体是无法实现这种效果的。
在 PVD 工艺中使用有机气体尤其有利于制作需要特定化学功能的聚合物薄膜。例如,乙烯可用于形成聚乙烯薄膜,这种薄膜以其优异的机械性能和耐化学性而著称。同样,丙烯也可用于制造聚丙烯薄膜,这种薄膜具有很强的耐热性和耐化学性。
此外,有机气体还可与其他气体结合,制成复合薄膜,显示出有机和无机成分的混合特性。这种混合方法可以定制薄膜的特性,从而使薄膜能够满足电子、光学和机械工程等行业的特定应用。
总之,在 PVD 工艺中加入有机气体为制造先进的聚合物薄膜和复合材料开辟了新的可能性,使开发具有独特和增强特性的材料成为可能。
调节气体压力
PVD 工艺中的气体压力在决定沉积速率和薄膜质量方面起着关键作用。该参数直接影响气态材料从靶材移动到基材时的行为。
在较低的气体压力下,气态材料会更均匀地扩散,从而提高薄膜的致密性和均匀性。这是因为压力降低可最大限度地减少气体分子之间的碰撞,使沉积过程更加有序。因此,生成的薄膜缺陷更少,结构更一致。
相反,较高的气体压力会导致薄膜粗糙度增加。在这些条件下,气体材料会经历更频繁的碰撞,从而破坏有序的沉积过程。这将导致薄膜的均匀度降低,表面粗糙度可能增大。不过,值得注意的是,较高的压力也能提高沉积速率,尽管会牺牲薄膜质量。
气体压力 | 薄膜质量 | 沉积速率 |
---|---|---|
更低 | 提高致密性和均匀性 | 更慢 |
较高 | 粗糙度增加 | 更快 |
最佳气体压力通常由应用的具体要求决定,在对高质量薄膜的需求和对高效沉积速率的渴望之间取得平衡。这种微妙的平衡对于实现最终产品的理想性能至关重要。
PVD 涂层工艺的应用领域
电子行业
在半导体器件、集成电路和显示器领域,物理气相沉积 (PVD) 工艺在各种薄膜的制造中发挥着举足轻重的作用。具体来说,PVD 主要用于制备三种类型的薄膜:导电薄膜、绝缘薄膜和光学薄膜。
导电薄膜
导电薄膜对于确保电子设备内的电流流动至关重要。这些薄膜通常由铝、铜和金等金属制成,通过热蒸发或溅射等技术沉积而成。金属和沉积方法的选择会对薄膜的导电性、附着力和整体性能产生重大影响。
绝缘薄膜
另一方面,绝缘薄膜对于防止电路短路和保护敏感元件至关重要。二氧化硅(SiO₂)和氮化硅(Si₃N₄)等材料通常用于制作这些薄膜。PVD 工艺可精确控制薄膜的厚度和均匀性,这对保持设备的完整性和可靠性至关重要。
光学薄膜
光学薄膜旨在管理光与设备表面的相互作用,提高显示清晰度并减少眩光。这些薄膜通常包括抗反射涂层和透射率增强层。PVD 工艺可制造出具有特定光学特性(如折射率和透射率)的薄膜,以满足设备的要求。
总之,PVD 工艺在电子工业中不可或缺,它为生产现代电子设备所需的导电、绝缘和光学薄膜提供了一种通用而精确的方法。
光学设备
PVD(物理气相沉积)工艺在光学镀膜的生产中起着至关重要的作用,而光学镀膜对于提高各种光学设备的性能至关重要。这些涂层包括抗反射涂层、透射率增强薄膜和保护层,所有这些涂层都是为了优化光与设备表面的相互作用而设计的。
光学镀膜的类型
-
抗反射涂层:这些涂层的设计目的是尽量减少光反射,从而增加通过光学表面的光量。这在相机镜头、眼镜和太阳能电池板等应用中尤为重要。
-
透射率增强薄膜:这些薄膜旨在提高特定波长光的透过率,这对光学过滤器和传感器等设备至关重要。
-
保护层:这些涂层可保护底层材料免受潮湿、灰尘和机械损伤等环境因素的影响,从而确保光学设备的使用寿命和性能。
PVD 光学镀膜的优点
- 精密:PVD 工艺可精确控制薄膜厚度,这对实现所需的光学性能至关重要。
- 耐用性:与使用其他方法镀膜的光学设备相比,PVD 镀膜光学设备具有更高的耐用性,因此非常适合在各种环境中长期使用。
- 多功能性:PVD 工艺可用于制造各种涂层,满足不同光学应用的特定需求。
在光学设备中的应用
设备类型 | 镀膜用途 |
---|---|
相机镜头 | 用于改善成像的抗反射涂层 |
眼镜 | 抗反射和抗划伤涂层 |
太阳能电池板 | 抗反射涂层,最大限度地捕捉能量 |
滤光片 | 增强特定波长的透射率 |
传感器 | 确保性能稳定的保护层 |
PVD 工艺不仅能提高这些设备的功能,还能延长其使用寿命,是光学行业不可或缺的技术。
机械部件
在机械部件的表面处理领域,物理气相沉积(PVD)工艺在提高机械部件的使用寿命和性能方面发挥着举足轻重的作用。物理气相沉积技术被精心用于增强这些部件的耐磨性、耐腐蚀性和抗氧化性。这大大延长了它们的使用寿命,使它们在苛刻的工业环境中更加可靠耐用。
在机械部件中应用 PVD 不仅仅是增加一层保护层,而是要结合先进的材料科学,创造出能够承受极端条件的表面。例如,汽车发动机、航空涡轮机和工业机械中的部件经常要经受可能导致快速降解的苛刻条件。通过使用 PVD 涂层,这些部件可以抵御摩擦、化学反应和高温暴露造成的磨损。
此外,PVD 涂层还可以量身定制,以满足不同机械部件的特定要求。无论是制造业中的高精度工具还是医疗设备中的关键部件,定制涂层的能力都能确保每个部件在其独特的条件下发挥最佳性能。这种定制水平是通过改变沉积参数(如目标材料类型、气体压力和温度)来实现的,目的是对生成薄膜的性能进行微调。
总之,在机械部件的表面处理中使用 PVD 工艺是一项战略性投资,可提高部件的耐用性和性能,最终有助于提高各种工业应用的效率和可靠性。
装饰涂层
PVD 工艺有助于制作装饰膜,增强各种产品的美感。这些薄膜具有金属光泽和鲜艳色彩,被广泛应用于珠宝、手表和家居用品等领域。该工艺可精确控制薄膜厚度和均匀性,确保最终产品符合这些行业对视觉吸引力和耐用性的高标准要求。
在珠宝领域,PVD 涂层可提供仿贵金属外观的精致饰面,而成本仅为贵金属的一小部分。这对于大批量生产尤其有利,因为在大批量生产中,保持奢华的外观至关重要。另一方面,PVD 涂层不仅能增强手表的视觉效果,还能防止划痕和腐蚀,延长手表的使用寿命。
厨具和装饰品等家用产品也可利用 PVD 涂层获得现代时尚的外观。在涂层中加入各种颜色和图案的能力为设计提供了广泛的可能性,使 PVD 成为制造消费品的多功能工具。
此外,PVD 工艺还非常环保,因为它是在真空条件下操作的,最大限度地减少了浪费,降低了传统涂层方法对环境的影响。这种可持续发展的特性进一步增强了 PVD 工艺在美学和环境责任都至关重要的行业中的吸引力。
PVD 工艺的优势和挑战
优势
PVD 涂层工艺具有多项令人信服的优势,使其成为各行各业的首选。其中最重要的优势之一是可以生产出高质量薄膜.这些薄膜具有卓越的附着力,均匀性和结构完整性这对提高涂层材料的性能至关重要。例如,在电子工业中,PVD 涂层导电薄膜可确保卓越的导电性和最小的信号损耗;而在光学设备中,涂层可提供精确的光学特性,从而提高设备性能。
另一个显著优势是环保 PVD 工艺对环境的友好性。与其他一些镀膜方法不同,PVD 是在真空条件下进行的,最大限度地减少了向环境中释放有害物质。这使得 PVD 成为一种可持续的选择,尤其是在环保法规严格的行业。此外,氩气和氦气等惰性气体的使用可确保薄膜的纯度,而不会产生任何可能危害环境的反应性副产品。
薄膜的多功能性 PVD 工艺的多功能性也是其主要优势之一。PVD 可应用于多种材料,包括金属、陶瓷和聚合物,因此适用于多种应用。无论是制备半导体薄膜、提高机械部件的耐用性,还是为消费品制作装饰涂层,PVD 都能提供灵活的解决方案,满足特定需求。例如,使用氧气和氮气等活性气体可以生成复杂的氧化物和氮化物薄膜,从而进一步扩大了可能的应用范围。
总之,高质量薄膜生产、环境可持续性和广泛适用性的结合,使 PVD 涂层工艺在多个领域成为一项极具优势的技术。
挑战
物理气相沉积 (PVD) 工艺面临的主要挑战之一是高昂的设备成本.先进的 PVD 系统(如利用电子束蒸发或脉冲激光沉积的系统)需要精密的机械和精确的控制系统,这对于规模较小的企业来说可能过于昂贵。此外,这些系统的维护和校准需要专业知识,进一步增加了总体成本。
另一个关键挑战是沉积率.实现最佳沉积速率对高效生产至关重要,但它会受到气体压力、基底温度和所用目标材料类型等众多因素的影响。较慢的沉积速率会导致加工时间延长,增加运营成本,并可能影响沉积薄膜的质量。相反,较高的沉积速率可能会导致薄膜具有次优特性,如密度降低或粗糙度增加。
薄膜厚度控制 也是 PVD 过程中的一个重要障碍。确保基底上的薄膜厚度均匀一致对最终产品的性能和可靠性至关重要。然而,保持对薄膜厚度的精确控制是一项挑战,尤其是在处理复杂的几何形状或大面积基底时。厚度的变化会导致薄膜性能的不一致性,如光学、机械或电气特性,从而对预期应用造成损害。
为了应对这些挑战,目前的研究和技术进步主要集中在开发更具成本效益的设备、优化沉积参数和改进薄膜厚度控制机制上。这些努力旨在提高物理气相沉积工艺的效率和可靠性,使其在各行各业中更加普及和有效。
联系我们获取免费咨询
KINTEK LAB SOLUTION 的产品和服务得到了世界各地客户的认可。我们的员工将竭诚为您服务。如需免费咨询,请与我们的产品专家联系,以找到最适合您应用需求的解决方案!