真空镀膜技术的历史发展
早期挑战与 CVD 技术
20 世纪 60 年代,随着化学气相沉积(CVD)技术的出现,真空镀膜技术迈出了重要的第一步。这项开创性的技术虽然在当时具有革命性意义,但也并非没有挑战。最重要的障碍之一是对高温的要求,这限制了可有效镀膜的基材类型。CVD 工艺的高热要求意味着只有热稳定性高的材料才能承受沉积条件,这大大缩小了潜在应用领域。
此外,早期的 CVD 技术还受限于其所能生产的涂层种类有限。CVD 所涉及化学反应的复杂性和特殊性意味着只有少数材料可以可靠地沉积,这进一步限制了它的应用。这些限制给真空镀膜技术的发展和广泛应用带来了巨大挑战,因此必须寻找能够克服这些障碍的替代方法。
在随后的几十年中,这些早期的挑战为开发更通用、更高效的镀膜技术铺平了道路,例如 20 世纪 70 年代出现的物理气相沉积(PVD)技术,它提供了一种适应性更强、更环保的解决方案。
PVD 技术的出现
到 20 世纪 70 年代,随着物理气相沉积(PVD)技术的出现,真空镀膜技术的格局发生了重大转变。这种新方法不仅解决了与其前身化学气相沉积(CVD)相关的一些环境问题,还引入了以前无法实现的多种表面特性。从 CVD 到 PVD 的转变标志着操作温度的降低和可应用涂层范围的扩大,从而拓宽了其在各行各业的应用。
PVD 在环境方面的优势尤为显著。与通常需要高温和潜在危险化学品的 CVD 不同,PVD 在更受控制的条件下运行,从而降低了能耗和排放。这种环境友好性,再加上其生产硬度、耐磨性和防腐性能优异的涂层的能力,迅速赢得了研究人员和工业家的关注。
PVD 技术在这一时期的快速发展归功于它的适应性以及对涂层质量和耐久性的显著改善。从汽车到航空航天等行业都开始采用 PVD 技术,因为它能提高工具和部件的性能,从而提高效率,延长产品寿命。这种广泛应用进一步推动了 PVD 技术的进步,推动了该技术的发展,巩固了其在现代工业流程中的地位。
现状与挑战
发展不平衡
尽管真空镀膜技术被广泛用于装饰目的,但在工业模具制造中应用这些涂层仍然充满挑战。主要障碍在于工业模具对附着力的严格要求,这就要求涂层与基材之间的粘合力更加坚固耐用。目前的涂层技术很难满足这一更高的要求,因为这些技术通常将美观性放在首位,而不是功能性的耐用性。
此外,缺乏专门针对工业模具涂层的综合工艺技术也进一步加剧了这些挑战。与装饰涂料不同,装饰涂料的应用方法可以不那么严格,而工业模具涂料则需要精确可控的工艺来确保最佳性能和使用寿命。这种技术发展上的差异导致了真空镀膜行业的不平衡发展,装饰涂料的进步并没有在工业应用中得到充分体现。
为了解决这些问题,迫切需要开发能够满足工业模具涂层独特需求的专业技术和方法。这不仅包括提高涂层的附着力,还包括完善从预处理到涂装后质量控制的整个工艺链。通过专注于这些领域,该行业可以弥合装饰涂料和工业涂料之间的差距,促进更均衡、更全面的发展轨迹。
技术差距
在真空镀膜技术领域,尤其是在 PVD(物理气相沉积)方面,国内的技术能力往往落后于国际标准。这种差距不仅仅是设备先进性的问题,还包括工艺优化、材料科学进步和质量控制方法等更广泛的因素。
为了缩小这一差距,国内工业不仅迫切需要引进先进设备,还需要吸收和整合尖端技术。这需要采取多方面的措施,包括
- 设备升级:投资最先进的真空室、电源和气体输入系统,以精确处理复杂的 PVD 工艺。
- 技术吸收:与国际合作伙伴开展合作研发,了解并实施 PVD 技术的最佳实践。
- 工艺优化:改进现有工艺,确保涂层质量的一致性,解决附着力和涂层一致性等问题。
优势 | 国内现状 | 国际标准 |
---|---|---|
设备 | 基本或过时 | 先进和高精度 |
过程控制 | 手动或半自动 | 人工智能支持下的全自动 |
材料科学 | 研究重点有限 | 广泛的研究和创新 |
质量控制 | 临时方法 | 系统、严格的 FQC |
在实现平等的过程中,不仅需要获取技术,还需要发展一个强大的生态系统,以支持持续创新和改进。这种整体方法对于提升国内能力并确保其能够在全球范围内竞争至关重要。
PVD 涂层的基本概念和特点
方法和技术
物理气相沉积(PVD)包含几种先进的方法,每种方法都有独特的特点和应用。多弧电镀和磁控溅射是 PVD 的两种主要技术。
多弧电镀是利用电弧蒸发目标材料,使材料电离并推向基底。这种方法以其高沉积率和复杂几何形状涂层能力而闻名。然而,这种方法也存在颗粒污染和涂层厚度不均匀等问题。
另一方面,磁控溅射利用磁场增强目标原子的电离,然后将其加速推向基底。这种技术能更好地控制涂层特性,包括密度和均匀性,因此非常适合需要精确涂层的应用。尽管磁控溅射具有这些优点,但与多弧电镀相比,磁控溅射速度更慢,能耗更高。
方法 | 优点 | 缺点 |
---|---|---|
多弧电镀 | 沉积速率高,适合复杂几何形状 | 颗粒污染,涂层厚度不均匀 |
磁控溅射 | 涂层性能控制出色,密度高且均匀 | 工艺较慢,能耗较高 |
了解这些方法及其各自的优缺点,对于为特定工业应用选择最合适的 PVD 技术至关重要。
技术组合
多弧和磁控管技术的结合是真空镀膜领域的一大进步。这种结合不仅仅是各部分的总和,而是一种协同方法,可最大限度地发挥两种技术的优势,确保生产出稳定、高质量的涂层。
多弧电镀以其高沉积率和生产致密涂层的能力而著称,与磁控溅射相辅相成,后者在生产均匀和保形涂层方面表现出色,而且基底加热程度极低。通过将这些方法结合起来,制造商可以在沉积速度和涂层均匀性之间取得平衡,这对于既要求效率又要求精度的应用来说至关重要。
此外,这些技术的混合使用还能优化涂层性能。例如,在磁控溅射工艺中加入多弧离子可以增强涂层的附着力和硬度,从而解决工业模具涂层中的常见难题,因为在这种工艺中,附着力和耐用性是最重要的。
这种整合还为材料选择和工艺控制开辟了新的途径。利用这两种技术的优势,可以沉积出更多具有定制特性的材料,从坚硬的耐磨涂层到更复杂的多层结构。因此,涂层解决方案的用途更广,性能更强,可满足各种工业应用的不同需求。
总之,多弧和磁控管技术的结合不仅提高了涂层的质量和稳定性,还扩大了可实现的材料特性和工艺效率的范围。这一进步是推动真空镀膜技术发展的关键,使其成为工业涂料发展的基石。
现代涂层设备和工艺
组件和系统
现代镀膜设备是由各种重要部件组成的精密组件,每个部件都在真空镀膜过程中发挥着至关重要的作用。该系统的核心是真空室真空室是一个密封环境,可将基材与大气条件隔离,确保镀膜表面纯净。真空室通常由不锈钢等材料制成,这些材料以耐用和耐腐蚀而著称。
为了达到所需的真空度,真空室需要真空获得部件 使用。这些部件包括真空泵,如旋片泵和涡轮分子泵,它们协同工作,将真空室的压力降至 PVD 过程所需的超低水平。这些泵的效率至关重要,因为它直接影响涂层的质量和均匀性。
电源是另一个关键部件,可提供使涂层材料气化所需的电能。现代系统通常使用中频电源 或脉冲技术可精确控制沉积过程,从而获得更高质量的涂层。这些先进的电源有助于减少电弧和不均匀沉积等问题,这些都是传统 PVD 设置中常见的难题。
最后工艺气体输入系统 是运行中不可或缺的部分。这些系统将活性气体引入真空室,从而形成具有定制特性的复杂涂层。通过对气体流速和成分的精确控制,可以形成具有特定机械、化学和光学特性的涂层,从而提高了该技术的多功能性和适用性。
总之,现代涂层设备是真空室、真空获取部件、电源和工艺气体输入系统的复杂组合,每一个部件都有助于提高 PVD 工艺的精度和质量。
先进技术
在真空镀膜技术领域,出现了几种先进技术,大大提高了镀膜的质量和适用性。其中一项技术是利用非平衡磁场.这些磁场可以更精确地控制沉积过程,从而制造出具有优异均匀性和附着力的涂层。这在对涂层的耐用性和性能要求极高的工业应用中尤为有益。
另一个关键进步是引入了中频电源.与传统电源不同,这些中频系统具有更高的稳定性和效率。它们有助于沉积更厚、更坚固的涂层,而不会影响底层材料的完整性。这一创新尤其适用于需要为模具和工具涂上高性能涂层的行业。
此外还有脉冲技术 彻底改变了涂层工艺。脉冲技术以短时间、可控的爆发方式提供能量,最大限度地减少了基材上的热应力,防止了翘曲和降解。这种方法对于易碎材料或需要复杂表面处理的材料尤为有利。精确的能量传输还能确保涂层更有效地附着,从而获得更持久、更可靠的效果。
这些先进的技术共同推动了真空镀膜技术的发展,使其在各种工业应用中更加广泛和有效。非平衡磁场、中频电源和脉冲技术的整合不仅提高了涂层的质量,还拓宽了涂层的应用范围,满足了现代工业日益严格的要求。
模具 PVD 的应用和质量控制
前处理和涂层工艺
前处理方法是物理气相沉积 (PVD) 涂层表面处理的关键步骤。这些方法包括高温蒸汽清洗,可有效去除污染物,确保基底清洁。喷砂是另一项重要技术,可提供粗糙的表面,增强涂层的附着力。PVD 涂层工艺本身在很大程度上依赖于精确的温度控制和均匀的加热,以达到最佳效果。
均匀加热至关重要,因为它能确保基底均匀受热,进而使涂层材料均匀沉积。温度控制同样重要,因为温度偏差会导致涂层厚度和质量不一致。通常采用中频电源和脉冲技术等先进技术来保持稳定一致的加热条件,从而提高 PVD 涂层的整体质量。
这些前处理和涂层工艺是 PVD 在工业模具中成功应用的关键。它们不仅能提高模具的耐用性和性能,还能延长模具的使用寿命,因此在高精度制造环境中不可或缺。
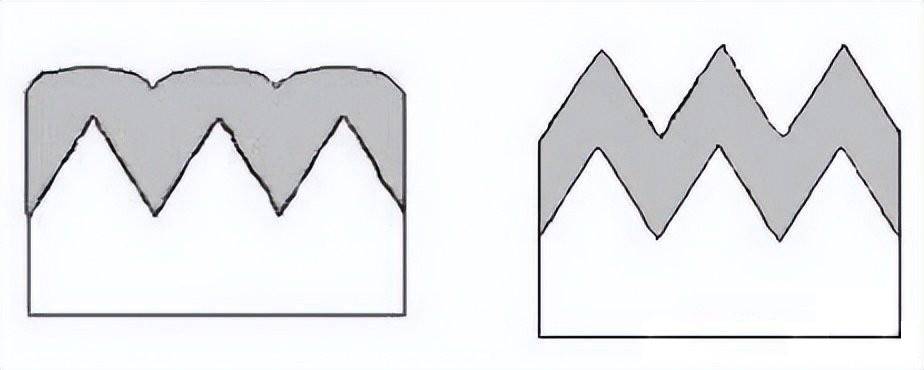
质量控制措施
功能质量控制 (FQC) 是确保涂层模具可靠性和性能的关键环节。这一过程包括多项细致的检查,以确保涂层符合规定的标准。
FQC 的主要方法之一是外观检查.这包括彻底的目视检查,以发现任何表面缺陷,如划痕、凹坑或变色。这些缺陷会严重影响模具的功能和使用寿命,因此这一步骤必不可少。
另一个关键方法是层深度检查.这项技术测量涂层的厚度,以确保它们符合规定的参数。使用轮廓仪和扫描电子显微镜等各种仪器可准确确定涂层的深度和均匀性。
附着力检测附着力检测 也至关重要。该工序评估涂层与模具基体之间的粘合强度。常用的方法包括划痕测试、拉力测试和横切测试。这些测试有助于识别任何潜在的分层或剥离问题,确保涂层的耐用性和有效性。
通过整合这些 FQC 方法,制造商可以确保其涂层模具不仅符合而且超过行业标准,为各种工业应用提供可靠的高性能工具。
联系我们获取免费咨询
KINTEK LAB SOLUTION 的产品和服务得到了世界各地客户的认可。我们的员工将竭诚为您服务。如需免费咨询,请与我们的产品专家联系,以找到最适合您应用需求的解决方案!